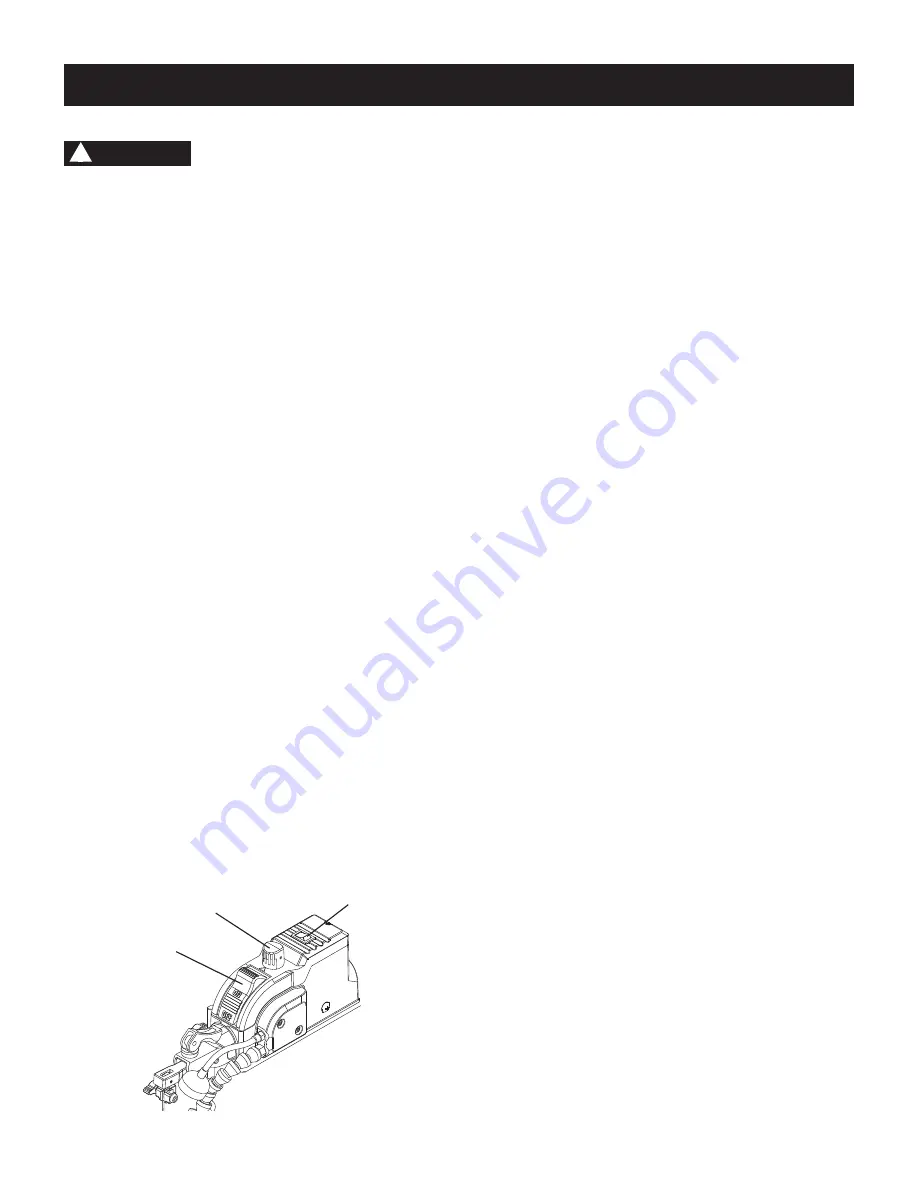
7
OPERATION
RECOMMENDATIONS fOR CUTTING
1. When feeding the workpiece into the blade do not
force the leading edge of the workpiece into the
blade because the it will deflect the blade, reduce
the accuracy of cutting and possibly break the
blade. Allow the saw to cut material by guiding the
workpiece into the blade as it cuts.
. The blade teeth cut material ONLY on the down
stroke.
3. You must guide the wood into the blade slowly
because the teeth of the blade are very small and
they can only remove wood when they are on the
down stroke.
4. There is a learning curve for each person who
wants to use this saw. During that period of time it is
expected that some blades will break until you learn
how to use the saw and receive the greatest benefit
from the blades.
5. Best results are achieved when cutting wood less
than one inch (5.4 mm) thick.
6. When cutting wood thicker than one inch (25.4 mm),
the user must guide the wood very slowly into the
blade and take extra care not to bend or twist the
blade while cutting in order to maximize blade life.
7. When teeth of scroll saw blade worn out, must
replace the new blade. Check the blade frequently
for best cutting results. Scroll saw blades generally
stay sharp for 1/2 to 2 hours of cutting.
8. To get accurate cuts, be prepared to compensate for
the blade’s tendency to follow the wood grain as you
are cutting.
9. This scroll saw is intended to cut wood or wood
products.
10. When choosing a blade to use with your scroll saw,
consider very fine, narrow blades to scroll cut in thin
wood in /4 in. (6.4 mm) thick or less. Use wider
blades for thicker materials but this will reduce the
ability to cut tight curves.
11. This saw uses 5 in. (127 mm) long pin or plain end
type blades.
12. Blades wear faster when cutting plywood or particle
board which is very abrasive. Angle cutting in
hardwoods reduces blade tooth set faster due to the
blade deflection.
VARIABLE SPEED CONTROL AND ON/Off SWITCH
CAUTION
!
for your own safety, always push the switch
“Off” when the scroll saw is not in use. Also, in the
case of power failure (all of your lights go out) push the
knob “OFF”. Remove the plug from the power source
outlet to avoid accidental starting.
ON/Off SWITCH (fIG. P)
. To turn power ON, press on/off switch () to “ON”
position.
. To turn power Off, press on/off switch () to “Off”
position.
VARIABLE SPEED CONTROL KNOB (fIG. P)
The variable speed control allows greater versatility to
cut a variety of materials such as wood, plastics, non-
ferrous metals, etc. Depending on the hardness and
thickness of material, the speed should be reduced to
allow the blade teeth to remove cut material from the
kerf.
. Your saw is equipped with a variable speed control
knob (). The blade stroke rate may be adjusted by
simply rotating the
variable speed control knob ().
. Turn the speed control knob clockwise to increase up
to ,500 strokes per minute (SPM). Turn the speed
control knob counterclockwise to reduce down to 500
strokes per minute (SPM).
WORK LIGHT (fIG. P)
1. To turn work light on, press the rocker switch (3) to
“ON” position.
2. To turn work light off, press the rocker switch (3) to
“Off” position.
fig. P
3
Содержание PCB375SS
Страница 9: ... UNPACKING YOUR SCROLL SAW A B C D E F H G ...
Страница 25: ...25 18 IN 457 MM VARIABLE SPEED SCROLL SAW SCHEMATIC B Hareware Bag ...
Страница 27: ...27 notes ...