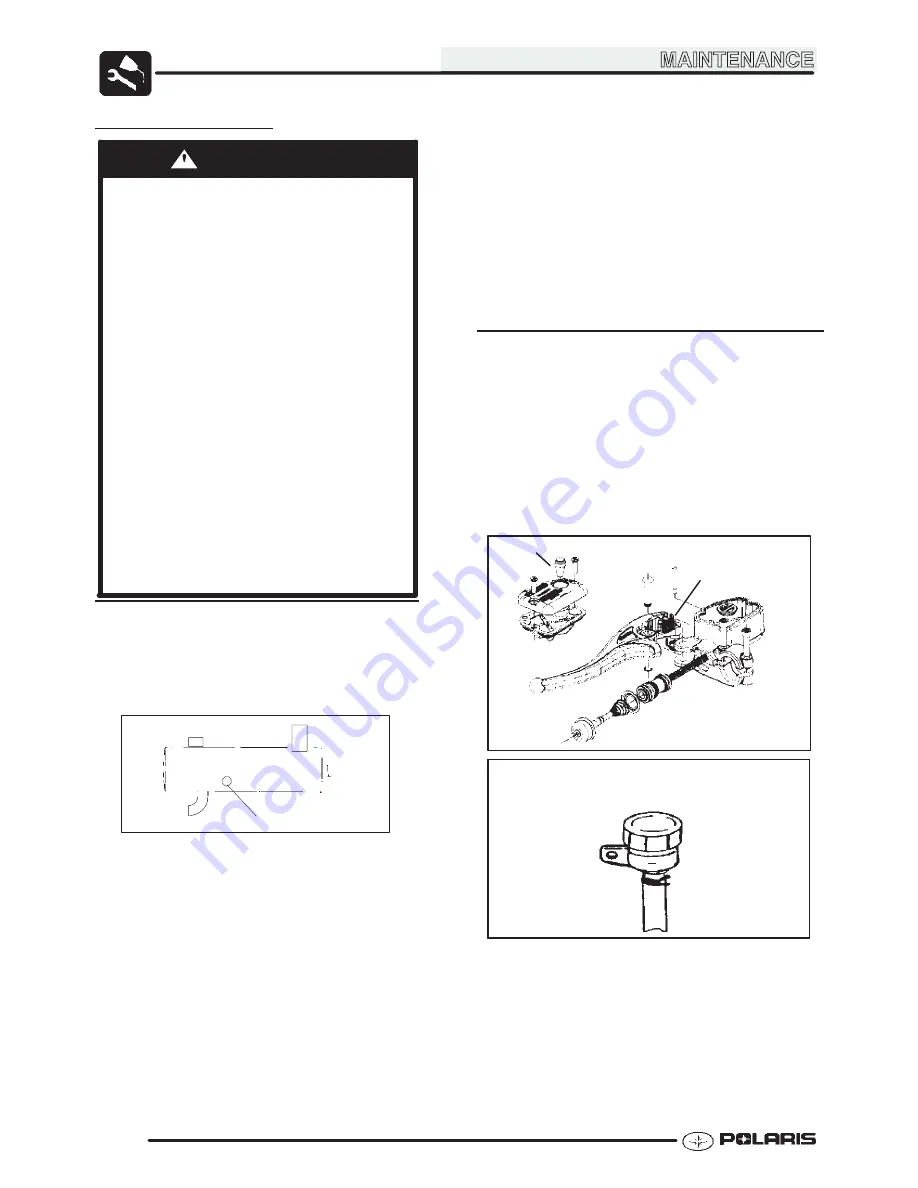
MAINTENANCE
2.26
EXHAUST PIPE
WARNING
G
Do not perform clean out immediately
after the engine has been run, as the ex-
haust system becomes very hot. Serious
burns could result from contact with ex-
haust components.
G
To reduce fire hazard, make sure that
there are no combustible materials in the
area when purging the spark arrestor.
G
Wear eye protection.
G
Do not stand behind or in front of the ve-
hicle while purging the carbon from the
spark arrestor.
G
Never run the engine in an enclosed
area. Exhaust contains poisonous car-
bon monoxide gas.
G
Do not go under the machine while it is
inclined. Set the hand brake and block
the wheels to prevent roll back.
Failure to heed these warnings could result in
serious personal injury or death.
The exhaust pipe must be periodically purged of
accumulated carbon as follows:
1.
Remove the clean out plugs located on the
bottom of the muffler as shown in illustration 1.
Clean Out Plug
Ill.1
2.
Place the transmission in neutral and start the
engine.
Purge accumulated carbon from the
system by momentarily revving the engine
several times.
3.
If some carbon is expelled, cover the exhaust
outlet and rap on the pipe around the clean out
plugs while revving the engine several more
times.
4.
If particles are still suspected to be in the muffler,
back the machine onto an incline so the rear of the
machine is one foot higher than the front. Set the
hand brake and block the wheels. Make sure the
machine is in neutral and repeat Steps 2 and 3.
SEE WARNING
5.
If particles are still suspected to be in the muffler,
drive the machine onto the incline so the front of
the machine is one foot higher than the rear. Set
the hand brake and block the wheels. Make sure
the machine is in neutral and repeat Steps 2 and
3.
SEE WARNING
6.
Repeat Steps 2 through 5 until no more particles
are expelled when the engine is revved.
7.
Stop the engine and allow the arrestor to cool.
8.
Reinstall the clean out plugs.
BRAKE SYSTEM INSPECTION
The following checks are recommended to keep the
brake system in good operating condition. Service life
of brake system components depends on operating
conditions. Inspect brakes in accordance with the
maintenance schedule and before each ride.
G
Keep fluid level in the master cylinder
reservoir to the indicated level inside
reservoir.
G
Use Polaris DOT 3 Brake Fluid (
PN
2870990
).
Parking Brake
Lock
Sight
Glass
Min
Max
Rear Master Cylinder Reservoir
G
Check brake system for fluid leaks.
G
Check brake for excessive travel or
spongy feel.
G
Check
friction
pads
for
wear,
damage or looseness.
G
Check surface condition of the disc.
G
Inspect thickness of brake pad
friction material.
Enfocus Software - Customer Support
Содержание SPORTSMAN 600 2003
Страница 1: ...2003 SPORTSMAN 600 2002 2003 SPORTSMAN 700 SERVICE MANUAL PN 9918066 ...
Страница 52: ...MAINTENANCE MAINTENANCE 2 30 ...
Страница 160: ...CLUTCH CLUTCH 6 26 NOTES ...
Страница 204: ...TRANSMISSION TRANSMISSION 8 16 NOTES ...
Страница 254: ...ELECTRICAL ELECTRICAL 10 30 NOTES ...
Страница 255: ...ELECTRICAL 10 31 WIRING DIAGRAM 2002 SPORTSMAN 700 ...
Страница 256: ...ELECTRICAL 10 32 WIRING DIAGRAM 2003 SPORTSMAN 600 700 ...
Страница 262: ...PN 9918066 Printed in USA ...