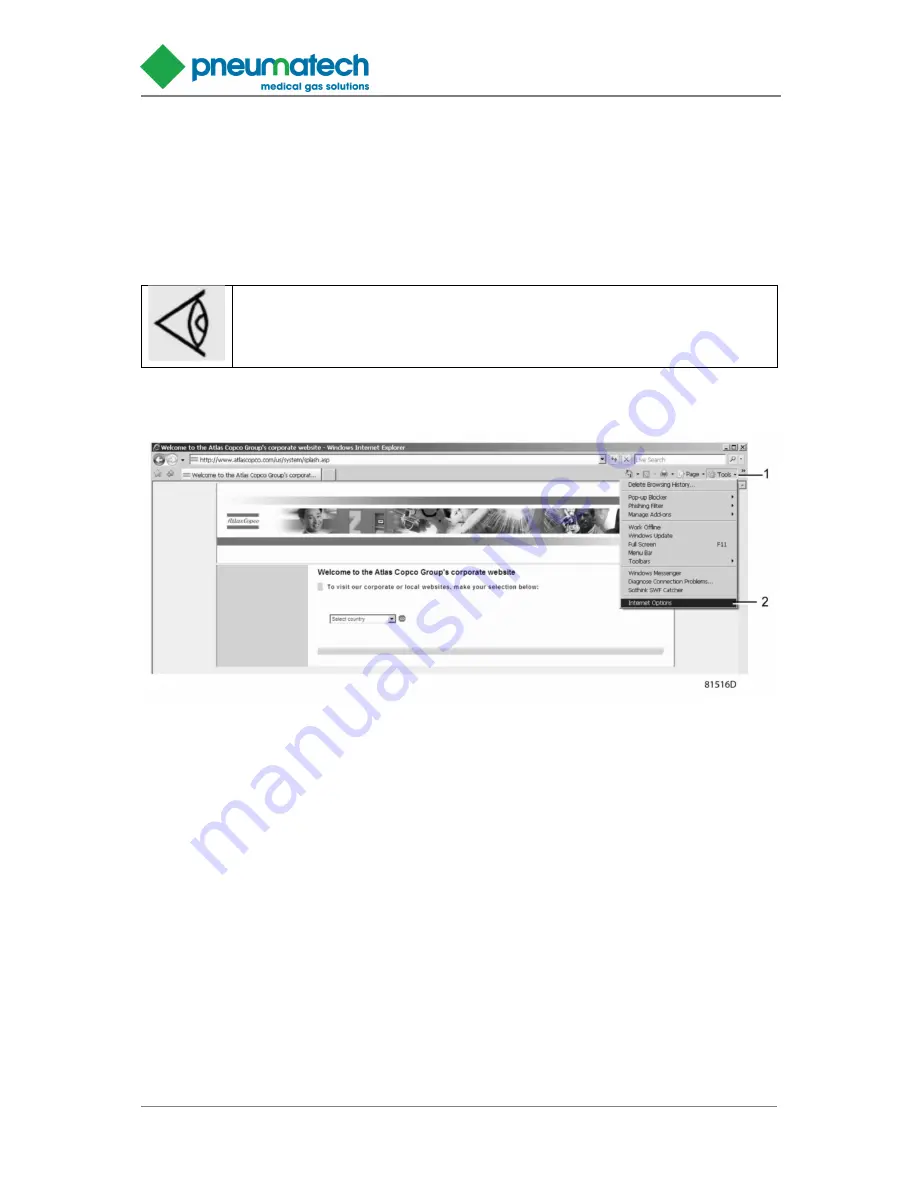
Installation, Operation and Maintenance Manual
Medical Vacuum Plant
Page 55
•
Use the following settings:
•
IP Address 192.168.100.200
•
Subnetmask 255.255.255.0
Click OK and close network connections.
Configuration of the web server
Configure the web interface
The internal web server is designed and tested for Microsoft® Internet Explorer 6,
7 and 8. Other web browsers like Opera and Firefox do not support this internal
web server. When using Opera or Firefox, a redirect page opens. Click on the
hyperlink to connect to the download server from Microsoft® to download the
latest version of Internet Explorer, and install this software.
When using Internet Explorer:
Open Internet Explorer and click on Tools - Internet options (2).
Figure 8-45; Web server – Internet explorer
•
Click on the Connections tab (1) and then click on the LAN settings button (2).
Содержание HTM02-01
Страница 1: ...Medical Vacuum Plant HTM2022 HTM02 01 Plant Systems Operation and Maintenance Manual ...
Страница 2: ......
Страница 73: ...Installation Operation and Maintenance Manual Medical Vacuum Plant Page 55 ...
Страница 74: ...Installation Operation and Maintenance Manual Medical Vacuum Plant Page 18 ...
Страница 75: ...Installation Operation and Maintenance Manual Medical Vacuum Plant Page 55 ...
Страница 76: ...Installation Operation and Maintenance Manual Medical Vacuum Plant Page 20 ...
Страница 77: ...Installation Operation and Maintenance Manual Medical Vacuum Plant Page 55 ...
Страница 78: ...Installation Operation and Maintenance Manual Medical Vacuum Plant Page 22 ...
Страница 80: ...Installation Operation and Maintenance Manual Medical Vacuum Plant Page 24 ...
Страница 81: ...Installation Operation and Maintenance Manual Medical Vacuum Plant Page 55 ...
Страница 82: ...Installation Operation and Maintenance Manual Medical Vacuum Plant Page 26 ...
Страница 83: ...Installation Operation and Maintenance Manual Medical Vacuum Plant Page 55 ...
Страница 84: ...Installation Operation and Maintenance Manual Medical Vacuum Plant Page 28 ...
Страница 85: ...Installation Operation and Maintenance Manual Medical Vacuum Plant Page 55 ...
Страница 87: ...Installation Operation and Maintenance Manual Medical Vacuum Plant Page 55 ...
Страница 88: ...Installation Operation and Maintenance Manual Medical Vacuum Plant Page 32 ...
Страница 89: ...Installation Operation and Maintenance Manual Medical Vacuum Plant Page 55 ...
Страница 90: ...Installation Operation and Maintenance Manual Medical Vacuum Plant Page 34 ...
Страница 91: ...Installation Operation and Maintenance Manual Medical Vacuum Plant Page 55 ...
Страница 92: ...Installation Operation and Maintenance Manual Medical Vacuum Plant Page 36 ...