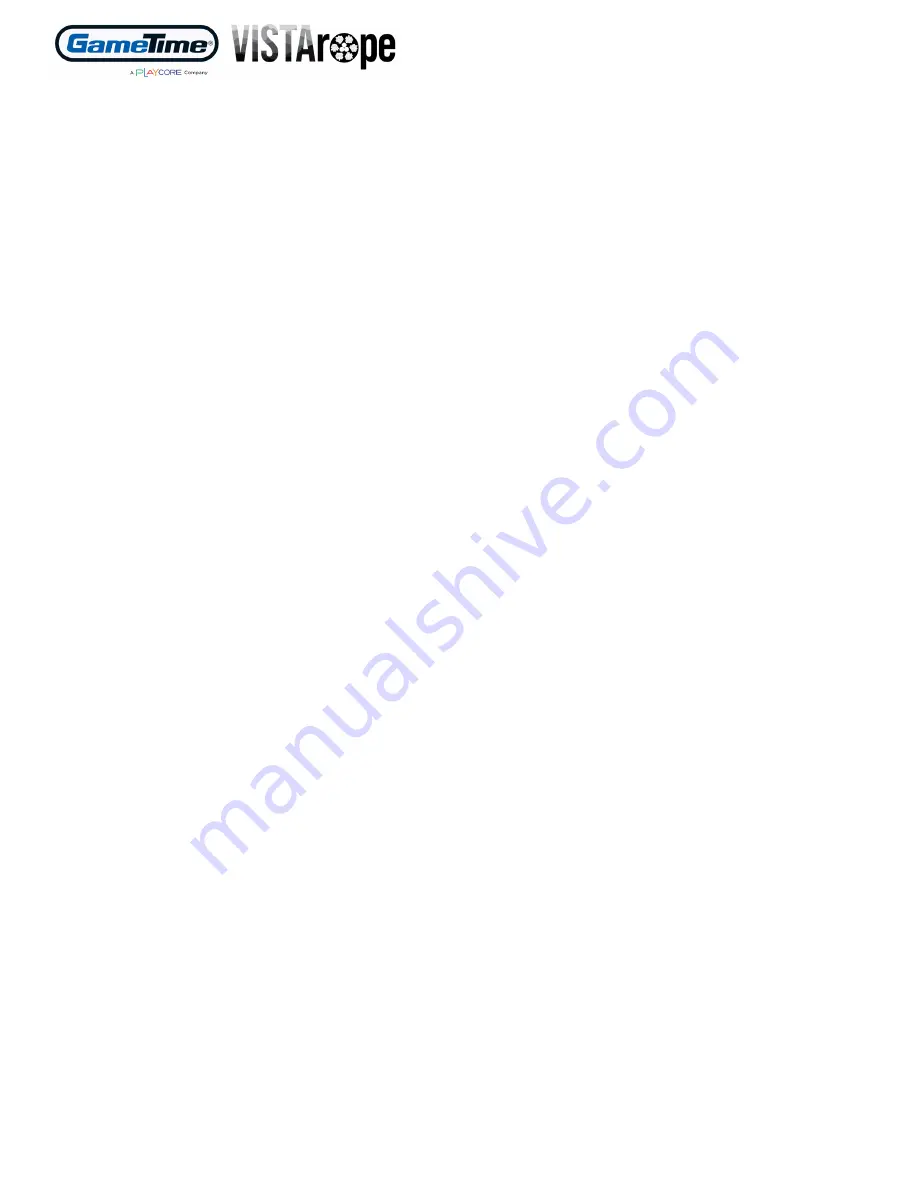
This equipment should be installed, inspected for proper
installation, maintained and operated in accordance with
applicable safety standards.
Regular maintenance is necessary on all park and play-
ground equipment, including the protective surfacing.
Proper maintenance extends equipment life. Maintenance
of play environments requires commitment from dedicated
and trained individuals with some mechanical ability and
common sense.
With regards to overall safety, if you ever feel a piece of
equipment or portion of the protective surfacing is broken or
dangerous, immediately take the equipment out of service.
If necessary, post personnel or fence the equipment to
prevent use until the necessary repairs can be made. This
is an important precaution that can potentially prevent an
injury.
Maintenance Inspection – Frequency and Process
Because play equipment and surfacing are subject to
changes from use, abuse, and climate, they must be in-
spected on a regular basis. The frequency of inspection will
be determined by many factors including equipment age,
use, and materials, and external factors like the age of the
users, climate, and vandalism. Regardless of site-specific
attributes of the playground, two types of inspections should
be performed on all playgrounds: low frequency and high
frequency.
Low Frequency Inspections
Often performed quarterly or semi-annually, low frequency
inspections are in-depth investigations of the equipment
and surfacing looking for wear and tear. This inspection
requires a staff member with mechanical knowledge and
extensive knowledge about play equipment and surfacing
standards. During or immediately after the inspection, staff
should do preventive maintenance and repairs and/or re-
move damaged equipment to remedy problems discovered
in the inspection.
High Frequency Inspections
Often performed daily or weekly, high frequency inspec-
tions look at frequently changing conditions caused by
use, weather, and/or vandalism. During a high frequency
inspection, staff checks and corrects playground conditions
such as loose-fill surfacing depths, sanitation issues, and
the presence of trash and debris. If any hazards are discov-
ered, staff should follow school or agency procedures such
as completing documentation, taking the area out of use,
and/or correcting the problem.
Loose hardware
Loose hardware can cause quality problems and put safety
at risk. Therefore, loose hardware should always be tight-
ened, and checks carried out to ensure that there are no
missing parts.
Identifying replacement parts
All replacement parts are listed in the parts list. The parts
list follows the installation requirements.
Actions to be taken during the break-in period
No later than 2 weeks after assembly, all hardware connec-
tions should be checked and tightened if necessary. One of
the most important factors in proper maintenance is main-
taining proper net tension. Net re-tensioning will be required
after the first 60-90 days of use and then must be checked
again on an annual basis.
Maintenance of protective surfaces
Surfaces providing fall protection must also be maintained
regularly. It is particularly important to maintain the correct
level of loose surface material and add more if necessary
(refer to applicable standards).
Damage
Damaged equipment must be repaired as soon as possi-
ble. If serious defects that affect the safety and cannot be
repaired immediately, the equipment then must be closed to
prevent further use.
PAGE 13
5960SP
MAINTENANCE