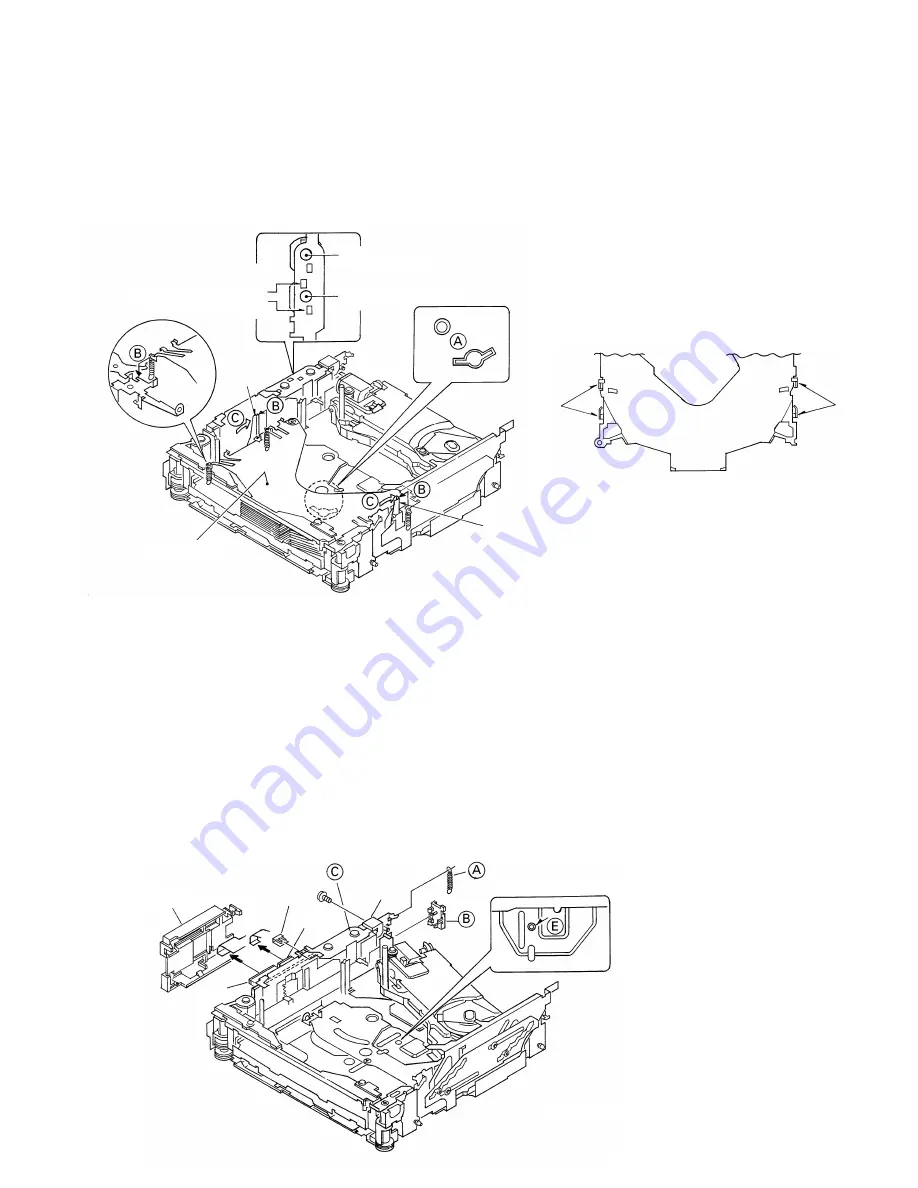
43
YPM-MG2196ZF
7.1.2 DISASSEMBLY
-
How to remove the Tray Assy
1. Apply about 6V current to the Cam gear motor until
all holes match at the position (A) (elevation OK posi-
tion).
2. Hook the three springs B temporarily as shown in Fig.
1. While pushing the Tray holder lock arms (right and
left) in the direction (C), remove the Tray holder.
3. Lift up the Tray assy to remove it.
* Be careful not to remove the Tray hooks from the Tray
assy.
-
How to remove the Carriage Mech Assy
1. Insert a short pin into the flexible PCB of the Pickup
unit.
2. While opening the resin hooks, remove the cover
from the Side PCB.
3. Disconnect the flexible PCBs from the connectors
CN863 and CN864.
4. Remove the Tray holder and the Tray assy. (See
above)
5. Rotate the Cam gear motor until the positions of all
holes (E) match, then stop the motor.
(The Carriage Mech assy will stop as shown in the
Fig.3.)
* When the positions of all holes match, they will be
completely covered by the Carriage mech assy.
* To rotate the Cam Gear motor, see "How to remove
the Tray assy".
6. Unhook the spring A.
7. Remove the flexible holder B (while opening the
hooks).
8. Remove the flexible PCB (C) from the motor. (The
flexible PCB (C) has been stuck on the motor with
double-sided adhesive tape.)
9. Loosen the fixing screw and remove the flexible
holder.
ELV motor
Cam gear motor
Approximately DC 6V
Tray holder
Tray holder lock arm
Tray holder
lock arm
Tray
hooks
Tray Assy
Cover
CN863
CN864
Match the hole positions
Flexible
holder
Fig.1
Fig. 2
Fig. 3
Short pin
Tray
hooks
Содержание YPM-MG2196ZF
Страница 3: ...3 YPM MG2196ZF ...
Страница 4: ...4 YPM MG2196ZF 2 EXPLODED VIEWS AND PARTS LIST 2 1 CD MECHANISM ...
Страница 17: ...17 YPM MG2196ZF ...
Страница 19: ...19 1 2 3 4 1 2 3 4 D C B A SIDE B E E E E E E E E 16 1 5 8 9 A CD CORE UNIT A YPM MG2196ZF ...
Страница 20: ...20 YPM MG2196ZF 1 2 3 4 1 2 3 4 D C B A CN801 PU UNIT A C D 4 2 SIDE PCB B SIDE PCB SIDE A B ...
Страница 22: ...22 YPM MG2196ZF 1 2 3 4 1 2 3 4 D C B A D 4 4 MOTOR PCB B SPINDLE MOTOR M5 MOTOR PCB B D ...
Страница 23: ...23 YPM MG2196ZF 1 2 3 4 1 2 3 4 D C B A D M M4 CARRIAGE 1 12 B CN864 ...
Страница 25: ...25 YPM MG2196ZF 1 2 3 4 1 2 3 4 D C B A M M2 LOADING 1 1 4 2 I M 4 6 LOAD MOTOR PCB LOAD MOTOR PCB G H J G ...
Страница 28: ...28 YPM MG2196ZF 1 2 3 4 1 2 3 4 D C B A LOAD DOOR MODE E 4 9 FORDSW PCB I FORDSW PCB I SIDE A ...
Страница 29: ...29 YPM MG2196ZF 5 6 7 8 5 6 7 8 D C B A I FORDSW PCB I SIDE B ...
Страница 35: ...35 YPM MG2196ZF Grating waveform Ech Xch 20mV div AC Fch Ych 20mV div AC 45 0 75 60 30 90 ...