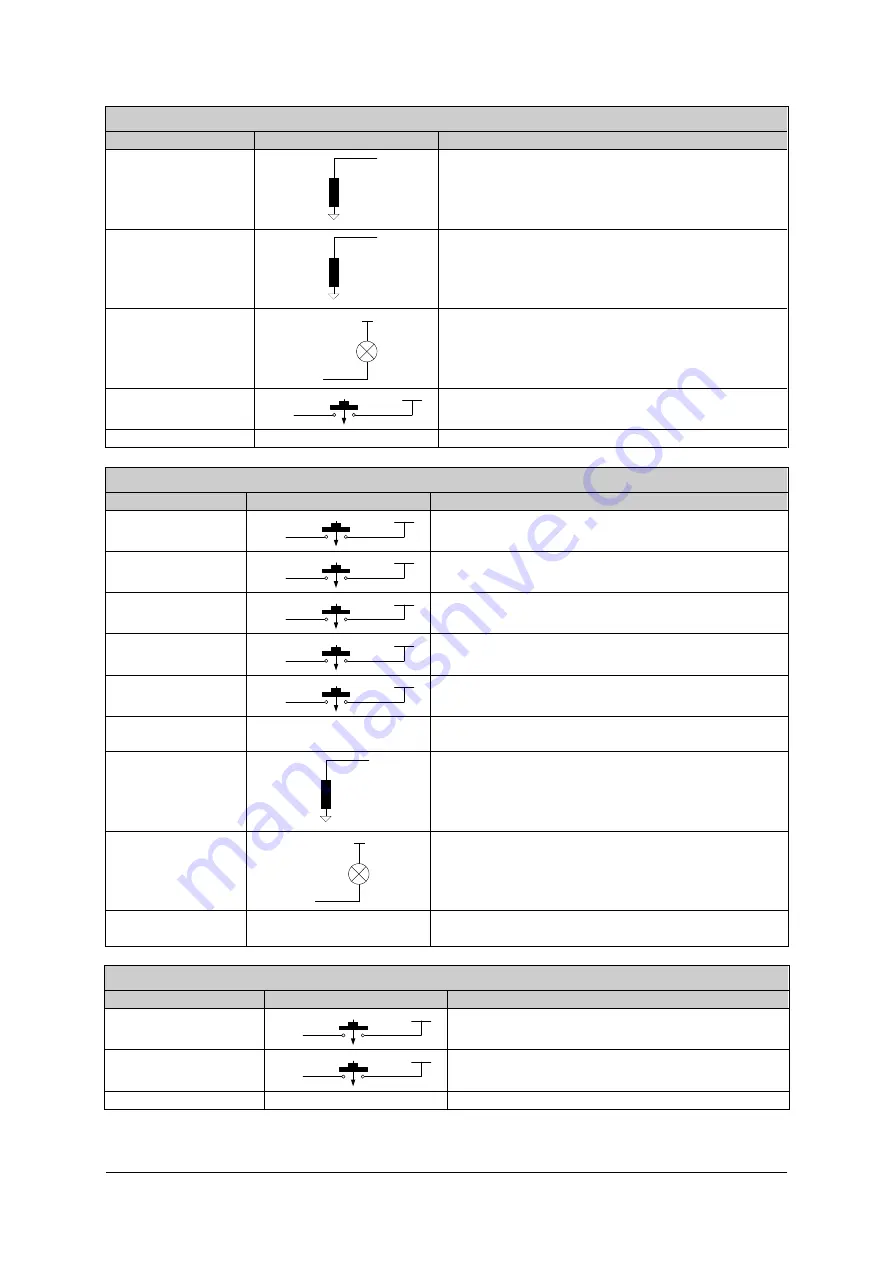
OPERATING MANUAL
PSEN op4F/H-A series
PSENopt Advanced RX Muting
CONNECTION
LINE
BEHAVIOUR
OSSD1 / OSSD 2
0V
OSSDs
Protected field clear
No voltage = Protected field not clear
OVERRIDE
STATUS
0V
OSSDs
High level = Override function active
Low level = Override function inactive
NOTE: This line signals the state of the override
signal inputs
MUTING LAMP
24Vdc
LAMP
The open collector connection is activated when
muting is activated.
MUTING1/MUTING2
24Vdc
IN line
N.O.
Is connected – when muting is active during
operation
FUNCTION EARTH
Connect to earth
PSENopt Advanced RX Blanking
CONNECTION
LINE
BEHAVIOUR
RESET
24Vdc
IN line
N.O.
Is connected – when in disabled state the
RESET/RESTART/ALIGN button is operated
RESTART
24Vdc
IN line
N.O.
Is connected – when during operation the
RESET/RESTART/ALIGN button is operated
ALIGNMENT
24Vdc
IN line
N.O.
Has to be set to 24 V DC at startup
TEACH-IN
24Vdc
IN line
N.O.
Is connected – when TEACH-IN button is operated
during operation
TOLERANCE
24Vdc
IN line
N.O.
Has to be set to 24 V DC at startup
EDM
See Chapter 7.4 for
connections
Must be non-equivalent to OSSD during operation
with EDM enabled
OSSD1 / OSSD 2
0V
OSSDs
Protected field clear
No voltage = Protected field not clear
BLANKING LAMP
24Vdc
LAMP
The open collector connection is switched when
blanking is activated.
FUNCTION
EARTH
Connect to earth
PSENopt Advanced TX
CONNECTION
LINE
BEHAVIOUR
TEST
24Vdc
IN line
N.O.
is connected, when the RESET button is
operated during operation
REDUCED RANGE
24Vdc
IN line
N.O.
Has to be set to 24 V DC at startup
FUNCTION EARTH
Connect to earth
1003067-EN-0
4
27