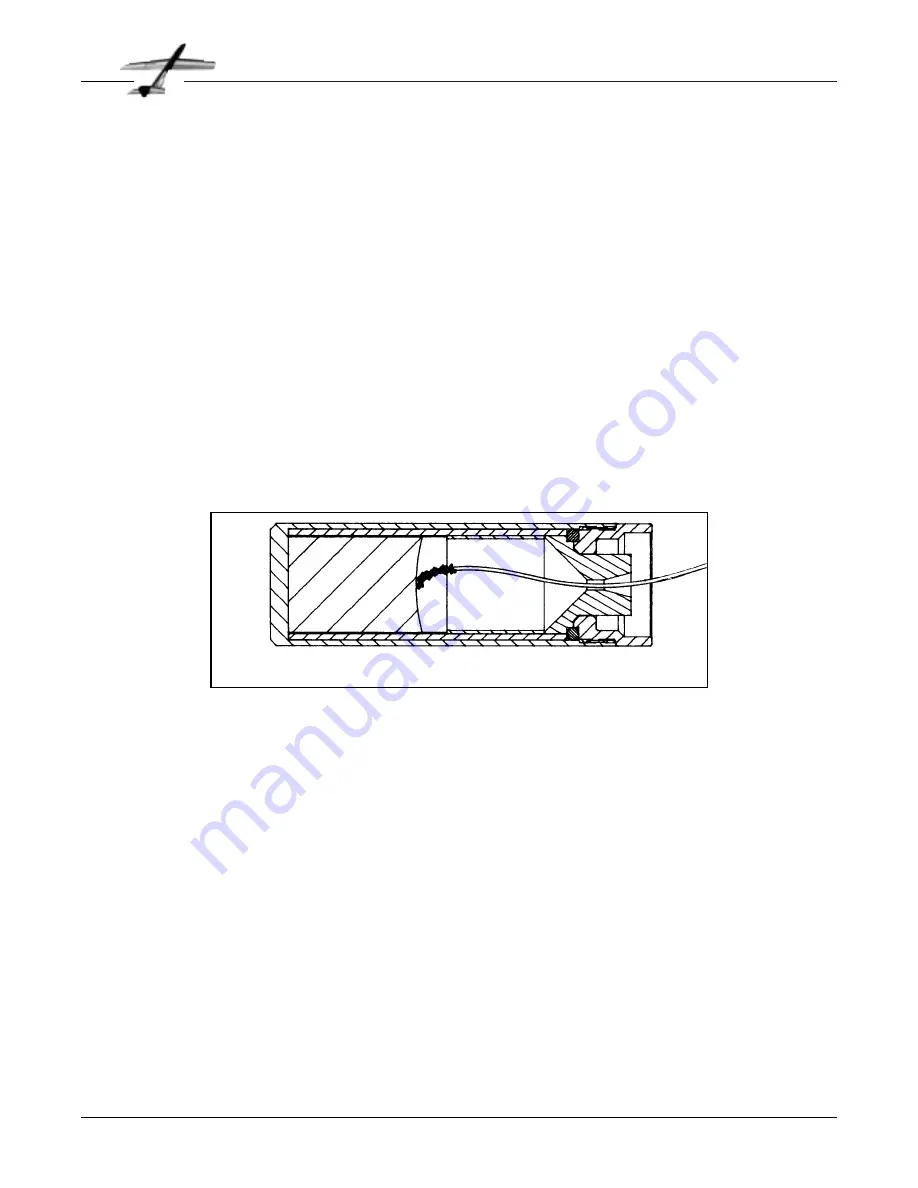
Phoenix
Page 38
Appendix B:About Rocket Motors
R
OCKET motors are a very different animal
than a typical gas or electric model air-
plane engine. Here is a bit of information on the
Phoenix motors, what they are and how they
work. You do not have to know any of this to
fly Phoenix, but we thought that some of you
would be interested.
First of all, while normal model airplane
engines are rated in terms of power, either
horsepower or watts, rocket motors are rated
in what is called “total impulse”. Total impulse
is measured in “pound-seconds”. A motor with
1 pound of thrust and a burn time of 1 second
has 1 pound-second of total impulse. A motor
with .1 pound of thrust and a 10 second burn
and a motor with a 4 pound thrust and a 1/4
second burn also have one pound second of
impulse. Most small rocket motors are actually
rated in the metric system. The metric equiva-
lent of the
pound-second
is the “New-
ton-second”.
There are 4.45
newtons in a
pound.
If we are flying
a spacecraft
somewhere
out in deep space, with no significant air or
gravity effects, then firing any of the three
motors will have the same effect. For example,
if our spacecraft weighs one pound, then firing
the motor will increase its speed by about 32
feet per second, about 22 miles an hour. Note
that it does not matter if we have a lot of thrust
for a short time or a low thrust for a long time.
If the total impulse is the same, it has the same
effect on speed of our spacecraft.
Things are different when we are launching
from the ground here on planet Earth where we
have both gravity and air drag to contend with.
If Phoenix weighs about 1.5 pounds, and we
use a motor with a thrust of less than 1.5
pounds, the model will never even leave the
launcher. On the other hand, if we use a really
high thrust motor, then we are likely to leave
the wings behind on the launch pad! What we
need to do is design an appropriate motor that
has enough thrust to fly the model, while still
keeping everything attached.
Fortunately, we have a bit more control of the
motor performance than just setting a thrust
level and a burn time. By specially shaping the
propellant, we can get a motor that has extra
thrust to help get the model moving and quick-
ly get it up to a speed where the controls are
effective. We then let the thrust decrease down
to a level where we can get a nice climb at a
reasonable speed.
T
HE performance of a motor is generally
shown in what is called a thrust-time curve,
which is just a plot of thrust versus time. If we
calculate the area under the curve, in units of
thrust and time, then we have the total
impulse. This is easy if the curve is a simple
rectangle, with constant thrust. If the thrust
varies, we
either work
harder to fig-
ure the area,
or program a
computer to
do it for us.
From the
curve, we can
also find some
other interest-
ing information, such as the peak thrust (so we
know how strong to make the wings!) and the
burn time.
Just like model airplane engines are grouped
into size categories by displacement, small
rocket motors are grouped by total impulse.
Each size category doubles the impulse of the
previous size. The Phoenix motors are
designed to fall into the “F” class (40 to 80 new-
ton seconds) and the “G” class (80 to 160 new-
ton-seconds). The letter designation is fol-
lowed by a number indicating the average
thrust in Newtons. Thus an F5 would have
about one pound of thrust (5 Newtons) on the
average, and would burn for 8 to 16 seconds.
An F80 would average about 16 pounds of
thrust and burn for one half to one second.
T
YPICAL small rocket motors used in model
rockets are designed to allow the model to
coast for a few seconds, and then deploy a
RMS-RC 32/60-100 Motor with F13-RC reload