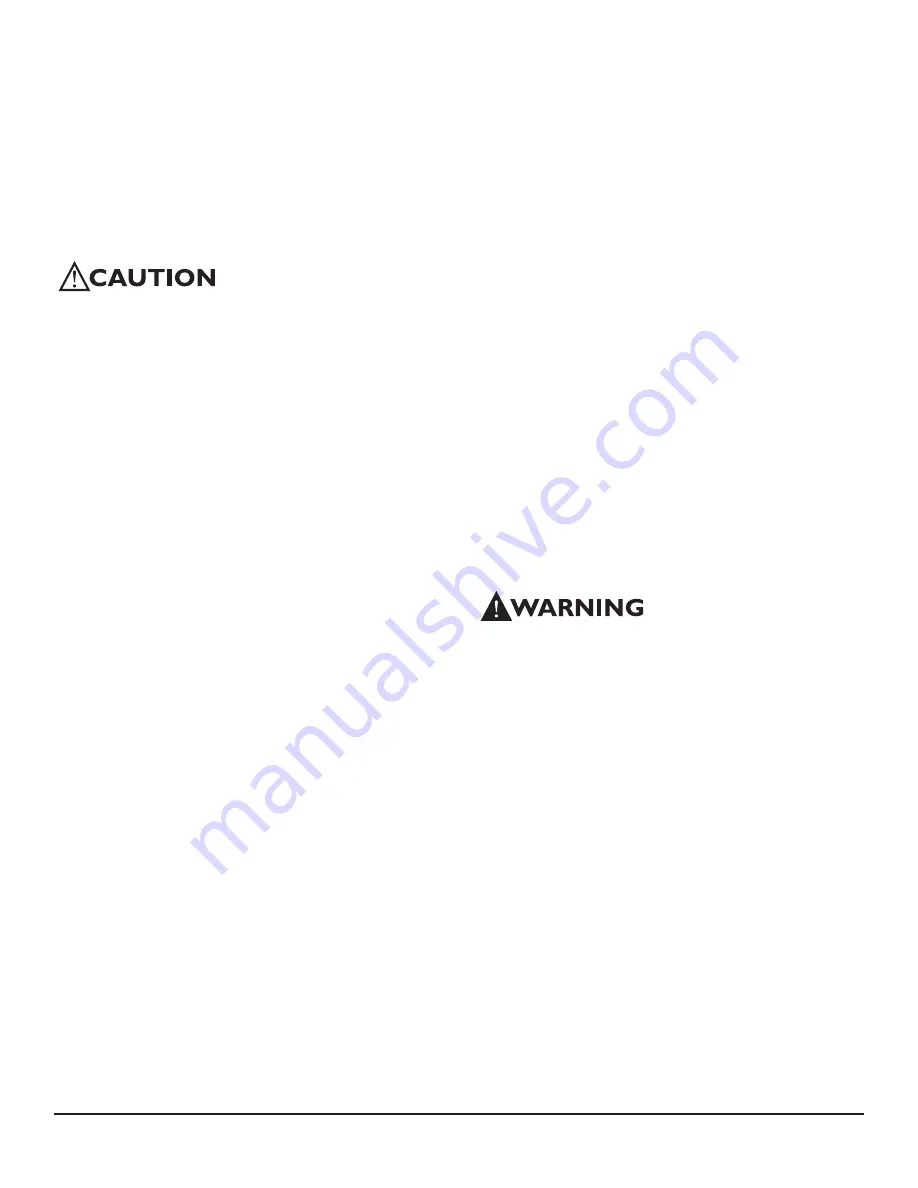
6
www.UsePhoenix.com • [email protected]
Toll-Free 1-800-533-7533
5. Rotate the blower outlet toward you as you remove it.
Use care to avoid hooking wiring, tubing or electrical
components.
6. Reassembling with the new blower in the above
procedure reversed.
4.6 Compressor/Capacitor Replacement
This compressor is equipped with a two terminal external
overload, run capacitor, but no start capacitor or relay (see
Fig. 3).
CAUTION-ELECTRICAL SHOCK HAZARD: Electrical power
must be present to perform some tests; these tests should
be performed by a qualified service person.
4.6A Checking Compressor Motor Circuits
Perform the following tests if the blower runs but the
compressor does not with the power switch ON.
1. Turn the power switch OFF and unplug the unit, remove
top panel and the cabinet front (6 screws).
2. Plug in the unit and turn the power switch ON. Use a
voltmeter to check for 110 to 120 volts between (a) the
relay terminal that the black wire from the compressor
connects to and (b) the capacitor terminal with the 2
white wires & blue wire connected. If voltage is present,
go to step 3. If no voltage, the low pressure control or
relay are open or there is a loose connection in the
compressor circuit. Test each component for continuity;
see the appropriate section if a defect is suspected.
3. Turn the power switch OFF and unplug the unit, then
disconnect the red and yellow wires from compressor
terminals R & S. Using an ohmmeter, check continuity
between the points listed below.
4. Compressor terminals C and S: No continuity indicates
an open start winding; the compressor must be replaced.
Normal start winding resistance 3 to 7 ohms.
5. Compressor terminals C and R: No continuity indicates
an open run winding; the compressor must be replaced.
Normal run winding resistance is .5 to 2 ohms.
6. Compressor terminal C and overload terminal 1: No
continuity indicates a defective overload lead.
7. Overload terminals 1 and 3: If there is no continuity, the
overload may be tripped; wait 10 minutes and try again.
If there is still no continuity, it is defective and must be
replaced.
8. Compressor terminal C and compressor case: Continuity
indicates a grounded motor; the compressor must be
replaced.
9. Disconnect the wires from the capacitor. Set the
ohmmeter to the Rx1 scale; the capacitor is shorted and
must be replaced if continuity exists across its terminals.
If there is no needle movement with the meter set on
the Rx100000 scale, the capacitor is open and must be
replaced.
10. Reconnect the wires to the compressor and capacitor;
plug in and turn on the unit. If the compressor fails to
start, replace the run capacitor.
11. If the unit still does not start, adding a hard-start kit will
provide greater starting torque. If this does not work, the
compressor has an internal mechanical defect and must
be replaced.
4.6B Replacing a Burned Out Compressor
The refrigerant and oil mixture in a compressor is chemically
very stable under normal operating conditions. However,
when an electrical short occurs in the compressor motor,
the resulting high temperature arc causes a portion of the
refrigerant oil mixture to break down into carbonaceous
sludge, a very corrosive acid, and water. These contaminants
must be carefully removed otherwise even small residues will
attack replacement compressor motors and cause failures.
The following procedure is effective only if the system is
monitored after replacing the compressor to insure that the
clean up was complete.
1. This procedure assumes that the previously listed
compressor motor circuit tests revealed a shorted or
open winding. If so, cautiously smell the refrigerant from
the compressor service port for the acid odor of a burn
out.
WARNING: The gas could be toxic and highly acidic. If no
acid odor is present, skip down to the section on changing
a non-burn out compressor.
2. Remove and properly dispose of the system charge. DO
NOT vent the refrigerant or allow it to contact your eyes
or skin.
3. Remove the burned out compressor. Use rubber gloves if
there is any possibility of coming in contact with the oil or
sludge.
4. To facilitate subsequent steps, determine the type of
burn out that occurred. If the discharge line shows no
evidence of sludge and the suction line is also clean
or perhaps has some light carbon deposits, the burn
out occurred while the compressor was not rotating.
Contaminants are therefore largely confined to the
compressor housing. A single installation of liquid
and suction line filter/driers will probably clean up the
system.
If sludge is evident in the discharge line, it will likely be
found in the suction line; this indicates the compressor
burned out while running. Sludge and acid have been
pumped throughout the system. Several changes of the
liquid and suction filter/driers will probably be necessary
to cleanse the system.