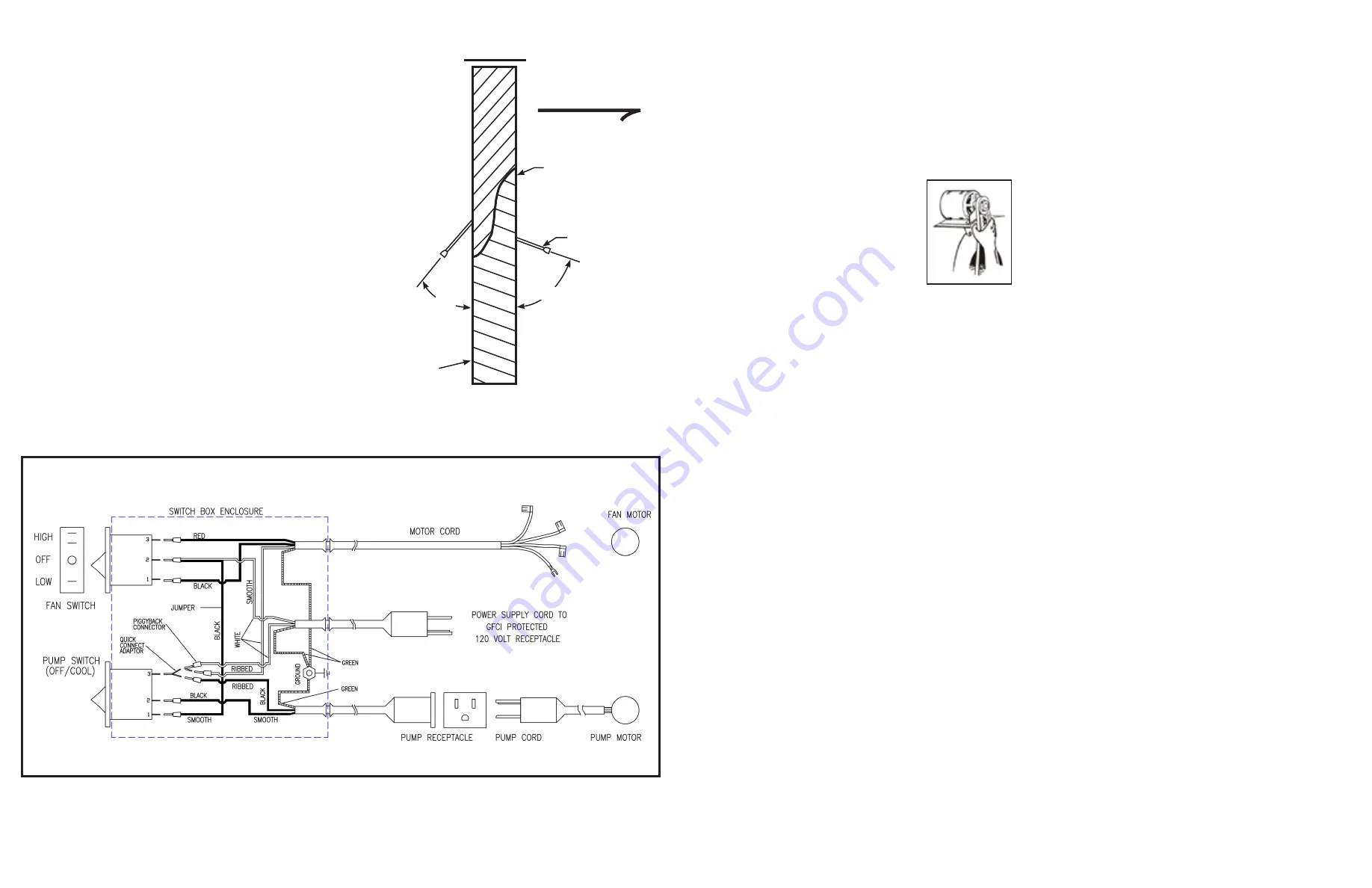
a. Remove inlet (back) grille from cabinet.
b. Remove top pan from cabinet.
c. Remove water distributor cover and tube assembly.
d. Remove pads by tilting slightly forward and carefully
lifting up and out. If passages are clogged or pad is dirty,
hose off inlet face of pad. Light, gentle brushing of the
inlet edges of the pad with a stiff bristle brush (do not use
a wire brush) will not harm the pad and will remove more
stubborn scaling.
e. If necessary, replace with new rigid media pads, available
only from your rigid media dealer. Aspen, expanded paper
or other types of evaporative cooling pads will not work
and will void your warranty.
3. Using a mild detergent, wash dirt and scale from the
inside of the wet section cabinet. Wire brushing is not
recommended. If finish is damaged or rusting is noted,
repair as noted in the “Touch-Up” section. Rinse with
fresh water.
• Reinstall pads, making sure they are positioned correctly
(painted stripe on pad placed to the bottom, facing
outside).
• Reinstall water distributor cover and tube assembly.
• Reinstall top pan to wet section cabinet.
• Reinstall inlet louver panels.
PAGE 6
WIRING DIAGRAM
END VIEW
AIR FLOW
THIS SURFACE TO
INSIDE OF UNIT
(TOWARD BLOWER)
PENCIL
SEE SIDE OF PAD
FOR DIRECTION
AL
AIR FLOW
45°
75°
PAGE 3
Motor and fan check
Using ¼ nut driver remove front grille screw as shown in fig-
ure 1. Remove the grille by slightly lifting it from the bottom,
pull outwards until clear of cabinet bottom pan, then down-
wards until frame clears cabinet top. Check motor mounting
to be sure all screws
Belt Adjustment
Correct belt tension and alignment is
important as it cuts power consumption
and prolongs life of belt and motor. When
installing or adjusting belt, loosen the
motor adjustment bolts and adjust for
proper tension. Align belt vertically by
centering motor pulley in-line with
blower pulley. Dot not adjust motor
sheave turns. Adjusting sheave turns
will void warranty.
Electric Power
CAUTION:
• This cooler is designed for connection to 120 volt AC, 60
Hz (cycle) power only. NOTE: Improper voltage will void the
pump and/or motor warranties and may cause serious per-
sonal injury or property damage.
• This cooler must be plugged into a GFCI protected re
-
ceptacle, which has been properly installed in accordance
with all local and national codes. If you are not sure that the
receptacle is GFCI protected, consult with a qualified electri
-
cian.
• This cooler is equipped with a power cord having an
equipment grounding conductor and grounding plug.
DO
NOT
attempt to defeat this safety device by removing the
grounding pin.
Cooler checkout and first time start-up
Congratulations your cooler is complete and ready for use.
Please proceed to Pre-startup inspection checklist on
page 3 before starting unit for the first time.
• Fan, shaft, pulley and motor sheave set bolts/screws are
snug.
• Motor sheave alignment okay; belt tension okay (see page
3 for instructions).
Start-up Checklist
CAUTION: Never operate unit with inlet/outlet grille
removed. This will result in an overloaded condition and
may damage the fan motor. The motor and pump have
an internal automatic thermal overload switch that will
shut the motor and/or the pump off if it overheats! The
motor and/or pump can restart automatically when they
cool down.
To verify and check out the cooler installation on initial start-
up, the following procedure should be followed.
• Push “COOL” switch to ON position (pump on).
• Verify that pump starts and pads are evenly wet.
• Open windows, doors or vents in building.
• Push “FAN” switch to LOW position (low speed on).
• Observe that motor starts and runs. Check high-speed
function by turning “FAN” switch to HIGH (high speed on).
In case of trouble in any of these stages, refer to the
Troubleshooting chart on page 7.
Cabinet Inspection Checklist
After initial start-up and during periodic inspections,
check for and/or observe the following: Refer to the
Troubleshooting Chart on if necessary.
• Leaks from cabinet
• Observe cooler media for uneven wetting
• Confirm water level setting is correct.
• Verify full, even flow in water distribution system.
• Fan / motor rotates freely, no unusual noises.
• Belt condition / tension / alignment.
• Check motor mounting and cabinet hardware.
Extended Shut-down (winterizing)
checklist
Any time the unit will not be used for an extended period:
• Move cooler to the area appropriate to dump water.
Remove brass drain cap as shown in fig 2. Drain all of the
water out of the cooler when not used for prolonged
periods, particularly at the end of the season (winter).
• Unplug the cooler power supply cord and secure it out of
the way on the side of the unit to avoid damage.
GENERAL INSPECTION
Pre-Start-up Inspection Checklist
• Cooler is on a level surface, casters locked to prevent
unnecessary movement (prevent spillage).
• Power supply cord is plugged into a GFCI protected
receptacle; cord is secure from accidental damage.
• Float valve installed.
• Water hose connected securely without leaks. Water
faucet or supply is turned on.
• Float adjusted for proper water level.
• Inlet and outlet grilles correctly installed.
• Pump impeller turns freely. Remove impeller cover
(see page 5 “Cleaning Pump”) and check rotation.
and nuts are tightened down properly.
hand to see that it moves freely withou
Rotate the fan by
ut rubbing against
hand to see that it moves freely without
housing. Reinstall the front grille and sec
rubbing against
cure with the scre
housing. Reinstall the front grille and secure
with the screw.