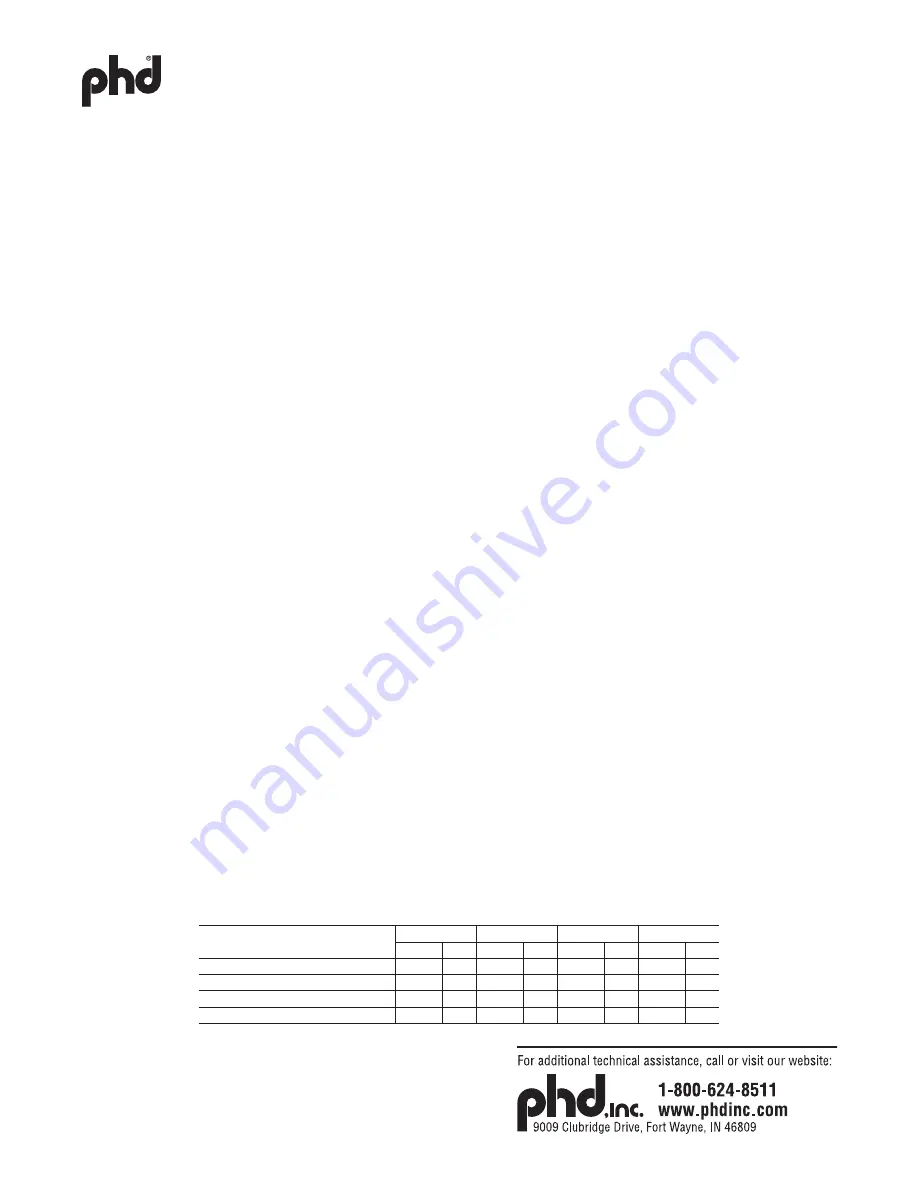
PART NO.: 6441-727A
2
REPAIR PROCEDURES: SERIES GRF DESIGN 2 [6] GRIPPERS
PHD, Inc. makes no warranty as to the fitness of its products or as to the length of service life after being repaired or parts replaced by anyone other than authorized
employees of PHD, Inc. In no event shall PHD, Inc. be liable for loss of profits, indirect, consequential, or incidental damages arising out of the use of PHD Products.
DISASSEMBLY PROCEDURE
1) WARNING: All air pressure in the unit must be relieved prior to disassembly of gripper.
2) During disassembly, be careful to avoid scratching bearing or sealing areas. Refer to Figure 1 unless otherwise noted.
3) -CP units: Remove proximity target (if attached) and prox target pin from jaw (CP proximity sensor ready option only).
4)
Standard units (see Figure 5): Remove sensor cover (cannot be reused). Pulling straight out from gripper to prevent bending or breaking magnet target
pin, use pliers to remove magnet target assembly (cannot be reused). Remove magnet target pin using 0.0605 in [1.5 mm] hex wrench.
5) Remove bore plug retainer, bore plug, and plug seal. Remove piston assembly fastener (size 25, 28, and 32). See Figure 2. Unscrew one-piece piston and
rod on size 19. See Figure 3.
6) Remove jaw cover assembly fasteners retaining jaw cover.
7) Move jaws to closed position and lift jaws and jaw driver from body of gripper.
8) Push rod through body to press out piston and piston seal. Remove piston seal, taking care to avoid scratching sealing surface of seal groove in piston.
9) Remove rod seal, note orientation of seal.
10) Clean and inspect all components. WARNING: Worn or damaged components should be replaced.
REASSEMBLY PROCEDURE
1) Be careful to avoid damaging seals during reassembly.
2) Lubrication guidelines (only use lubricants which are compatible with pneumatic devices)
• Standard Units: all components use petroleum-based high-pressure grease, oil wicks: petroleum-based heavy weight oil with Teflon
• -Y4 and -V6 Units: all components use Cleanroom designated grease, oil wicks: Cleanroom designated heavy weight oil
• -V1 Units: all components use PTFE based lubricant, oil wicks: PTFE-based heavy weight oil
3) Use removable threadlocker on all threaded fasteners.
4) Lubricate bore and grooves in body. Lubricate and install rod seal, see Figure 2 for orientation.
5) Lubricate jaw slot, jaws, cam driver and jaw cover where jaws slide along cover.
6)
Size 19 piston and piston rod: Replace and lubricate piston seal on one-piece piston and rod. Install piston and rod into bore, the thread at end of rod
should be visible in jaw slot. See Figure 3. Apply small amount of liquid threadlocker to thread at end of piston and rod.
7) Size 25, 28, and 32 piston rod: Lubricate rod, install in body with narrowed section visible in jaw slot. See Figures 1 and 2.
8)
Size 19 jaws: Install cam driver into one jaw. Place jaw and cam driver into a slot in jaw cover. Install remaining jaw into other slot in cover.
NOTE: jaws may need to be angled when inserting in cover slot. Verify that counterbore in cam driver (see Figure 2) is oriented to accept rod when assembled.
9)
Size 25, 28, and 32 jaws: Assemble both jaws to cam driver and move jaws to closed position. Verify that counterbore in cam driver (see Figure 2) is
oriented to accept rod when assembled. Note jaw orientation per Figure 1.
10) Align jaw and driver assembly with jaw slot. Slide assembly down into jaw slot. Size 25, 28, and 32: place lubricated jaw cover over onto body.
11) Apply removable threadlocker sparingly to jaw cover assembly fasteners and install in body. Torque jaw cover assembly fasteners per Table 1.
12) Size 25, 28, and 32 piston: Replace and lubricate piston seal. Insert piston with seal into body of gripper, see Figure 2 for orientation.
13)
Size 25, 28, and 32 piston: Apply removable threadlocker to piston assembly fastener and assemble through piston and rod into cam driver,
torque per Table 1.
14) Lubricate and install bore plug seal, see Figure 2 for location on sizes 28 and 32. Sizes 19 and 25 lubricate and install seal into groove in bore plug.
NOTE: Bore plug seal on sizes 28 and 32 may require stretching prior to installation to allow proper installation of bore plug.
15) Lubricate and install bore plug, see Figure 2 for orientation. Verify proper seating of bore plug.
16) Install bore plug retainer into body (sharp edges of retaining ring outward from body). Verify proper seating of retaining ring.
17)
Standard unit without -CP option: Apply removable threadlocker sparingly to thread on magnet target pin and install through target slot in body into jaw,
see Figure 5. Torque the magnet target pin in jaw per Table 1.
18) Press magnet target assembly onto magnet target pin as shown in Figure 5 until target is approximately 0.040 in [1 mm] below sensor slot surface.
19) Clean sensor slot surface (see Figure 5) to remove any grease or dirt. Carefully remove backing from aluminum sensor cover.
(WARNING: if cover becomes bent it will not adhere or seal properly.) Install sensor cover onto sensor slot surface with cover aligned with edge as
shown in Figure 1. Press firmly along length of cover to remove air.
20)
CP option: Apply removable threadlocker sparingly to prox target pin and install through body into jaw. Torque prox target pin in jaw per Table 1.
21)
GRF34-x-25 x 6.5 only: Apply removable threadlocker to bearing plugs on size 25. Install bearing plugs in body. See Figure 4 for orientation. Apply air
to unit and cycle at 30 psi [2.1 bar] while tightening bearing plugs. Tighten plugs until unit stops cycling, back-off screw until unit cycles freely. Allow
threadlocker to cure before use of unit.
TABLE 1 - GRIPPER ASSEMBLY TORQUES
PART DESCRIPTION
SIZE 19
SIZE 25
SIZE 28
SIZE 32
in-lb
Nm
in-lb
Nm
in-lb
Nm
in-lb
Nm
JAW COVER ASSEMBLY FASTENER
7
0.8
9
1.0
17
1.9
17
1.9
PISTON ASSEMBLY FASTENER
15
1.7
17
1.9
17
1.9
25
2.8
MAGNET TARGET PIN (STD UNIT)
20 in-oz 0.14 20 in-oz 0.14 20 in-oz 0.14 20 in-oz 0.14
PROX TARGET PIN (CP OPTION ONLY) 40 in-oz 0.28 40 in-oz 0.28 40 in-oz 0.28 40 in-oz 0.28