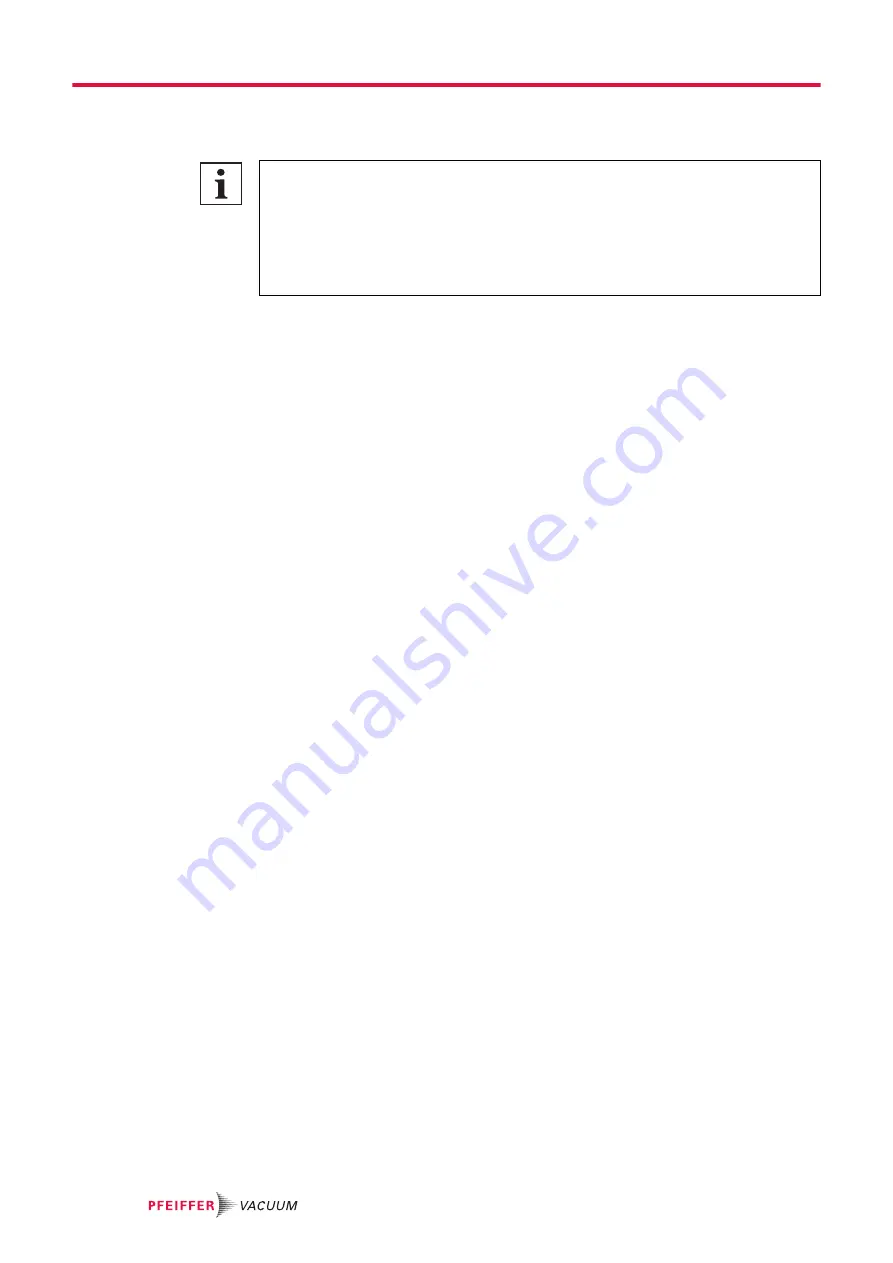
12 Spare parts
Ordering and using spare parts
Spare parts for service work are grouped into packs. These vary according to pump ver-
sion.
● You can ask Pfeiffer Vacuum Service for spare parts pack order numbers.
● Have the full vacuum pump article number (with index where applicable) to hand. You
can find it on the rating plate.
● Replace all parts contained in the pack.
12.1 Set of seals for version with RSSR
The set of seals contains:
● all sealing parts such as O-rings, radial shaft seal rings and supporting rings
● flat seals, square washers and annular profile seals
The protective sleeve and centering rings for connecting the roots pump to the suction and pressure
sides are not included.
12.2 Set of seals for version with magnetic coupling
The set of seals contains:
● all sealing parts such as O-rings
● flat seals, square washers and annular profile seals
Centering rings for connecting the suction and pressure sides are not included.
12.3 Maintenance kit for version with RSSR
The maintenance kit contains:
● all sealing parts in the area of the radial shaft seal ring including the protective sleeve
● all sealing rings of the filling and drain screws and both O-rings for the device cover and cap
● the coupling buffer (toothed ring)
12.4 Maintenance kit for version with magnetic coupling
The maintenance kit contains:
● all sealing rings of the filling and drain screws and both O-rings for the device cover and cap
● the O-ring for the isolation shroud
Spare parts
46/54
Содержание OKTA 1000 M
Страница 1: ...OPERATING INSTRUCTIONS EN Translation of the Original OKTA 250 250 M 500 500 M Roots pump ...
Страница 54: ...Notizen Notes ...
Страница 55: ......
Страница 56: ... PP0071 ed W Date 2108 P N PP0071BEN ...