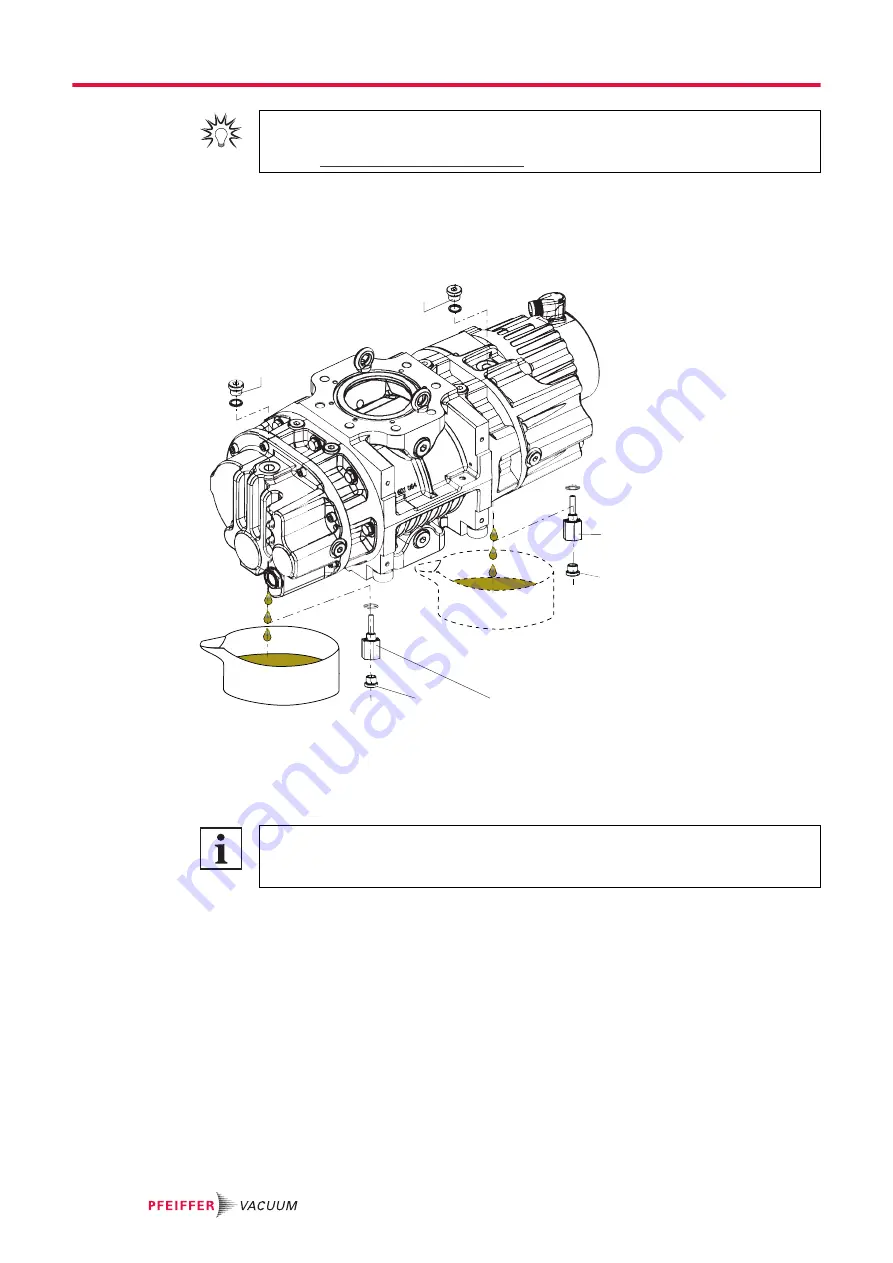
Safety data sheets
You can obtain the safety data sheets for lubricants from Pfeiffer Vacuum on request, or
from the
Pfeiffer Vacuum Download Center
.
9.4.1 Drain the lubricant
Required tools
● Allen key,
WAF 8
● Ring spanner,
SW 27
1
3
2
2
1
3
Fig. 18:
Drain the lubricant
1 Filler screws with seal
3
Fill level limiter
2 Drain screws with seal
Drain the lubricant
Unscrew the fill level limiter
To drain the lubricant, in addition to the drain screw, also unscrew the fill level limiter on the
pump bottom side.
1. Make sure that there is sufficient space underneath the pump to be able to place a collection re-
ceptacle for the lubricant.
2. Unscrew the filler screws.
3. Place the collection receptacle underneath.
4. Hold the fill level limiter with the ring spanner and unscrew the drain screw at the same time.
5. Unscrew the fill level limiter and allow the lubricant to drain.
9.4.2 Filling with lubricant
Required consumables
● Lubricant of the vacuum pump
Required tools
● Allen key,
WAF 8
● Ring spanner,
SW 27
Maintenance
48/68
Содержание HILOBE 1002
Страница 1: ...OPERATING INSTRUCTIONS EN Translation of the Original HILOBE 1002 1302 Roots pump ...
Страница 67: ...67 68 ...
Страница 68: ... PW0322 ed E Date 2102 P N PW0322BEN ...