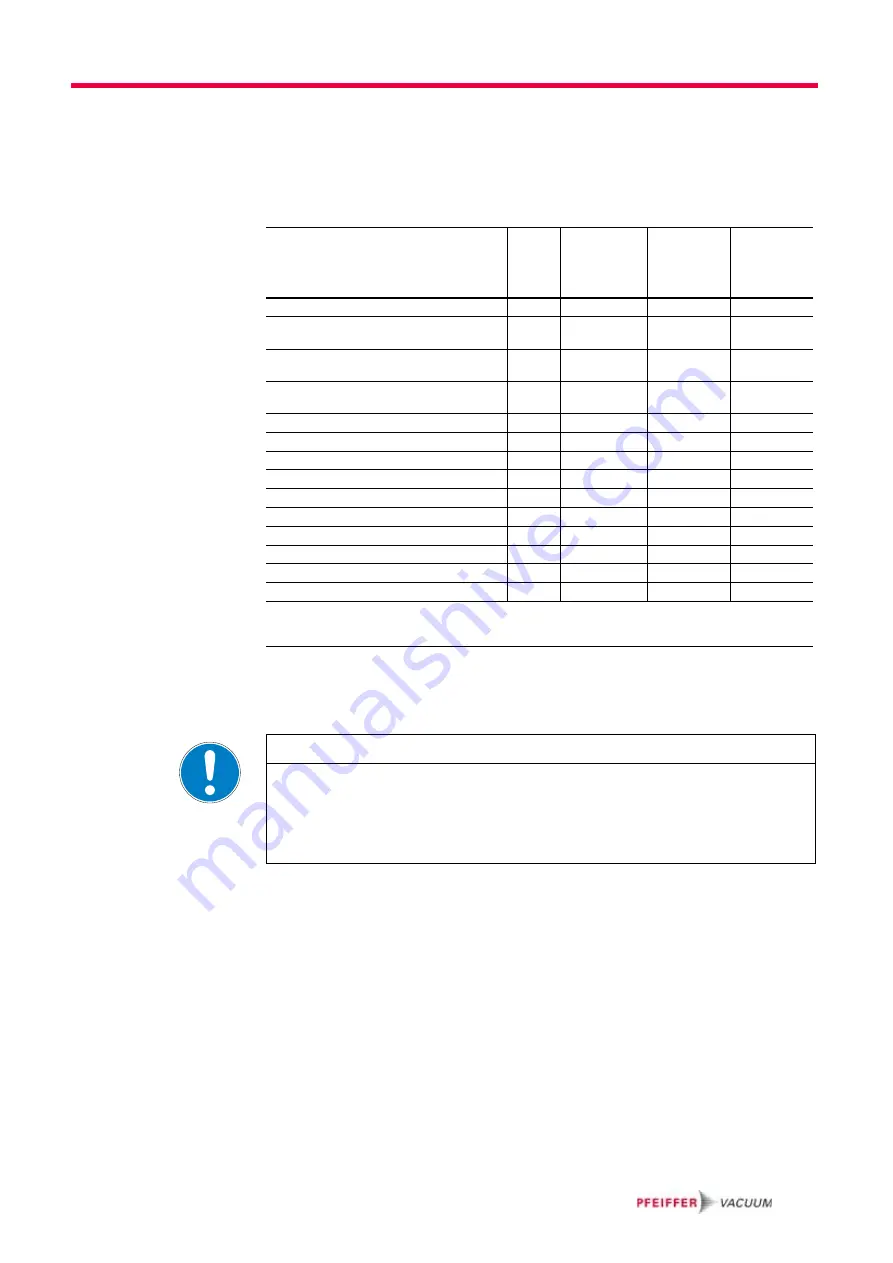
19
Maintenance
Checklist for inspection,
maintenance and over-
haul
Certain repair and overhaul work should only be performed by Pfeiffer Vacuum
Service (PV). Pfeiffer Vacuum will be released from all warranty and liability claims
if the required intervals for inspection, maintenance, or overhaul are exceeded or
inspection, maintenance, repair or overhaul procedures are not performed proper-
ly. This also applies if replacement parts other than Pfeiffer Vacuum OEM replace-
ment parts are used.
7.2
Changing the operating fluid
The changing interval for the operating fluid depends on the pump applications.
Î
Change the operating fluid at least once every year.
Î
The level of deterioration of operating fluid P3 can be read off the colour scale
in accordance with DIN 51578; request the supplementary sheet PK 0219 BN or
download it from the Internet.
Î
Fill the specimen in a test tube or some similar vessel and test by holding
against the light.
Î
Where discolouration is dark yellow to red brown (equivalent to 4 ... 5 on the sca-
le) change operating fluid.
Î
Switch off pump.
Î
Unscrew operating fluid drain screw 142 and drain operating fluid.
Activity
daily
as required;
at least
annually
as
required; at
least every
2 years
as
required; at
least every
4 years
Check operating fluid level
X
Visual inspection (leak-tightness/oil
leaks)
X
Check filter insert of external oil mist fil-
ter (if existent)
X
Change filter insert of external oil mist
filter (if existent)
X
Change operating fluid
X
Change oil filter (if existent)
X
Cleaning the pump and renew the seals
X
Clean gas ballast valve and silencer
X
Clean the motor fan cap
X
Replace radial shaft seal
X (PV)
Clean or change vacuum safety valve
X (PV)
Clean or change exhaust valves
X (PV)
Change vanes
X (PV)
Check or change coupling
X (PV)
Depending on the process, the required replacement intervals for lubricants and the intervals
for inspection, maintenance and overhaul may be shorter than the guide values specified in
the table.Consult with Pfeiffer Vacuum Service if necessary.
NOTE
Depending on the applications, Pfeiffer Vacuum recommends determining the
exact service life of the operating fluid during the first year of operation.
The replacement interval may vary from the guide value specified by Pfeiffer Vacuum
depending on the thermal and chemical loads, and the accumulation of suspended par-
ticles and condensation in the operating fluid.