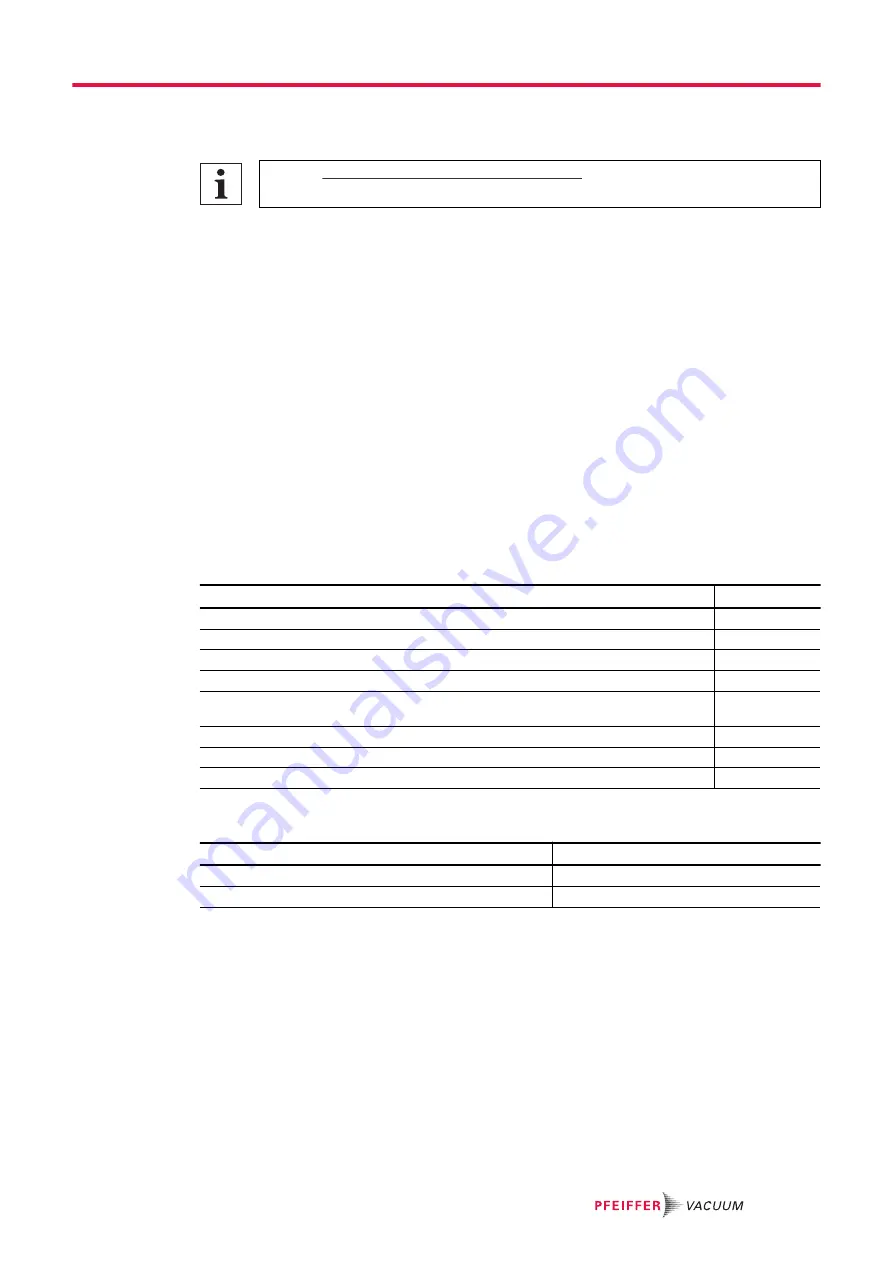
13 Accessories
range of accessories for rotary vane pumps
on our website.
13.1 Accessory information
OME 16 ATEX with operating fluid return line
The oil mist filter prevents the oil mist from escaping and channels separated operating fluid back into
the rotary vane pump.
Operation monitoring
The operation monitoring monitors the oil pressure and emits a signal in the event of a drop in pressure
or if the rotary vane pump shuts down.
Exhaust pressure monitoring
The pressure switch monitors the exhaust pressure of the rotary vane pump.
Operating fluid level monitoring
The level switch monitors the operating fluid fill level of the rotary vane pump.
Operating fluid temperature monitoring
The temperature sensor monitors the temperature of the operating fluid.
13.2 Ordering accessories
Accessories for Duo 11 ATEX
Order no.
OME 16 ATEX, Oil Mist Separator
PK Z40 200
Oil Return Unit ODK from OME 16 ATEX to Duo 11 ATEX
PK 006 081 -T
Operations Monitoring Unit 1, sensor for Oil level
PK 007 100 -T
Operations Monitoring Unit 2, Sensor for Oil Level and Oil Temperature
PK 007 101 -T
Operations Monitoring Unit 3, Sensor for Oil Level, Oil Temperature and Exhaust
Pressure
PK 007 102 -T
Operations Monitoring Unit 4, Sensor for Oil Pressure
PK 007 103 -T
PTC Resistor Tripping Device 220 – 240 V AC
P 4768 052 FQ
PTC Resistor Tripping Device 24 V AC/DC
P 4768 052 FE
Tbl. 12:
Ordering accessories
Consumables
Order no.
P3, mineral oil, 0.5 l
PK 001 136 -T
P3, mineral oil, 1 l
PK 001 106 -T
Tbl. 13:
Consumables
Accessories
53/58
Содержание DUO 11 ATEX
Страница 1: ...OPERATING INSTRUCTIONS EN Translation of the Original DUO 11 ATEX Rotary vane pump...
Страница 58: ...Notizen Notes...
Страница 59: ......
Страница 60: ...PD0079 E Date 2006 P N PD0079BEN...