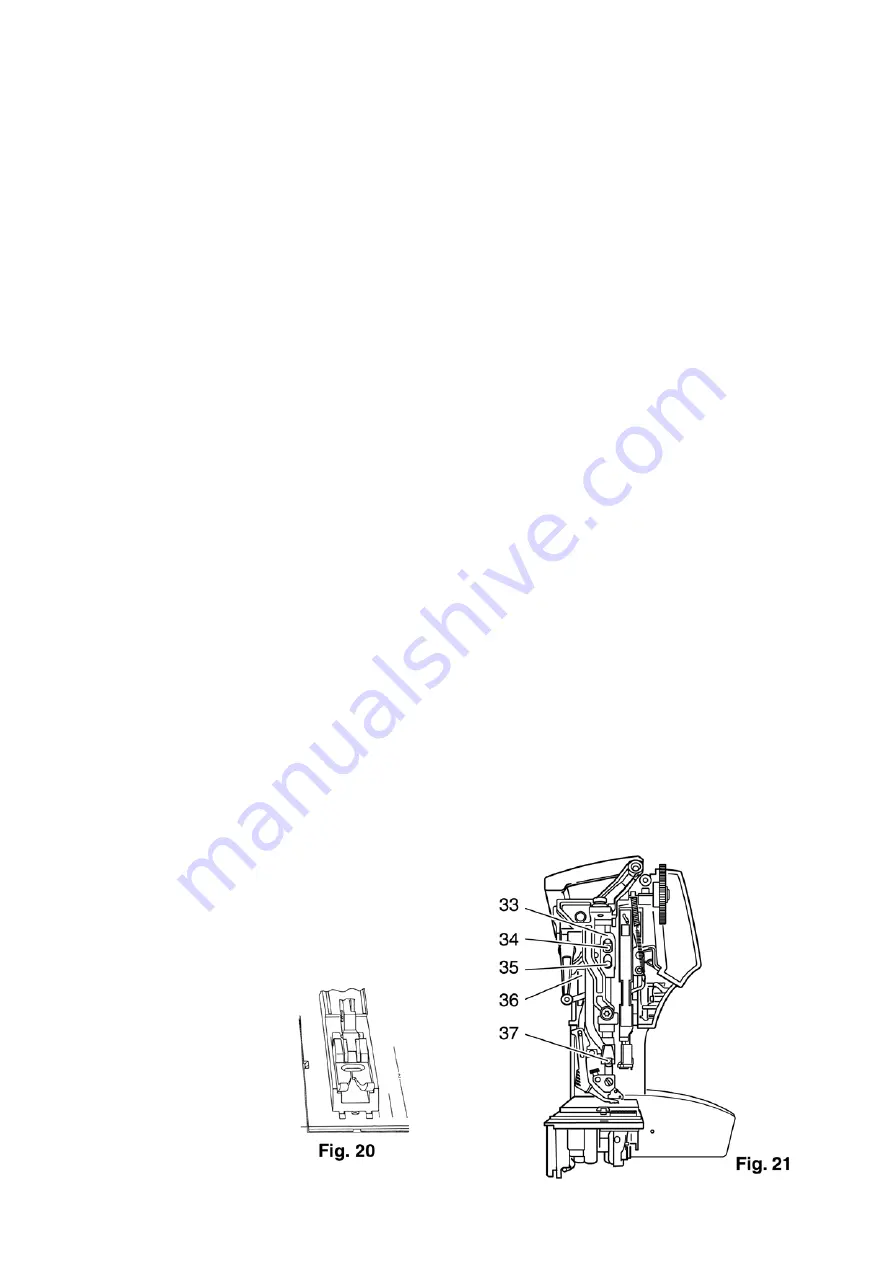
28
6. Adjustment of presser foot height
Requirement:
With the presser bar lifter raised there must be a clearance of 8 mm between the needle plate and the
sole of the zigzag foot.
Check:
●
Raise the presser bar lifter.
●
Fit the zigzag foot.
●
Lower the feed dog.
●
Fully raise the presser bar lifter and hold it in this position.
●
Insert the presser foot gauge (63-114 690-39) from behind under the zigzag foot and into the cutout of
the needle plate (fig. 20).
●
Lower the presser bar lifter to its normal position again.
The zigzag foot must rest parallel and without play on the presser foot gauge.
However the presser foot gauge must not lift the zigzag foot.
the needle thread tension must be without play (fig. 21).
Adjustment:
●
Loosen the three screws 34, 35 and 37 (fig. 21).
●
Turn the zigzag foot with the presser bar lifter raised until it is parallel with the sides of the presser foot
gauge.
●
Use a screwdriver to press presser bar guide 36 firmly down.
●
At the same time firmly tighten screw 35.
Cross-check:
●
Press the presser bar lifter further upward and release it again.
The zigzag foot must rest parallel and without play on the presser foot gauge.
Needle thread tension release lever 33 must be without play. The presser bar lifter must be in its raised
position.
Note:
The two screws 34 and 37 are not tightened until later
when the top feed height is set.
Содержание EXPRESSION 2014
Страница 1: ...Service Manual 1st edition November 2002 expression 2014 2024 2034 2044 german engineering...
Страница 2: ...Leerseite...
Страница 17: ...15 Remove buttonhole sensor s cable guide 20 fig 15 Remove the complete buttonhole sensor with the spring...
Страница 18: ...16 Notes...
Страница 27: ...25...
Страница 33: ...31 Cross check Turn the handwheel and check for clearance of 0 2 mm...
Страница 35: ...33...
Страница 39: ...37...
Страница 43: ...41...
Страница 51: ...49 Notes...
Страница 59: ...57...
Страница 61: ...59...
Страница 63: ...61...
Страница 65: ...63...
Страница 69: ...67...
Страница 73: ...71...
Страница 81: ...79...
Страница 83: ...81...
Страница 85: ...83...
Страница 87: ...85...
Страница 89: ...87...
Страница 93: ...91...
Страница 109: ...107...
Страница 111: ...109 Notes...