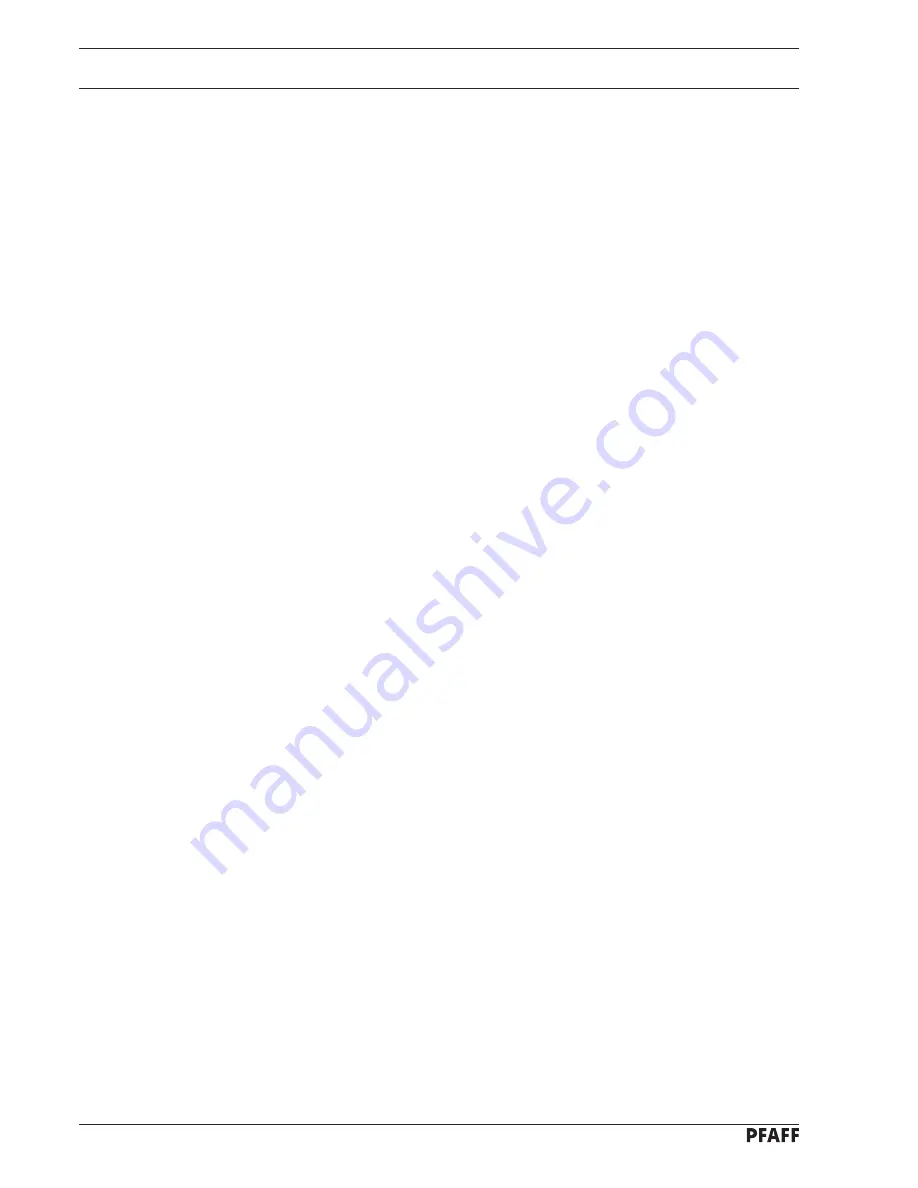
Safety
1
Safety
1
.01
General notes on safety
●
This machine must only be operated by adequately trained operators and only after
having completely read and understood the Instruction Manual!
●
All Notes on Safety and Instruction Manuals of the motor manufacturer are to be read
before operating the machine!
●
The Danger and Safety Instructions on the machine itself are to be followed!
●
The machine must be used only for the purpose for which it is intended and must not
be operated without its safety devices. Observe all relevant safety regulations!
●
When exchanging sewing tools (e.g. needle, presser foot, needle plate, feed dog and
bobbin), when threading, when the workplace is left unattended and during servicing,
the machine must be disconnected from the mains by switching off the on/off switch
or by removing the plug from the mains!
●
Daily servicing work must be carried out only by appropriately trained persons!
●
Repairs and special maintenance work must only be carried out by technicians or
persons with appropriate training!
●
For service or repair work on pneumatic systems the machine must be disconnected
from the compressed air supply. The only exceptions to this are adjustments and
function checks made by appropriately trained personnel!
●
Work on the electrical equipment must be carried out only by electricians or
appropriately trained personnel!
●
Work is not permitted on parts and equipment which are connected to the power
supply! Exceptions to this are contained in the regulations EN 50110!
●
Modifications and alterations to the machine must only be carried out under
observance of all the relevant safety regulations!
●
Only spare parts which have been approved by us are to be used for repairs! We
expressly point out that any replacement parts or accessories which are not supplied
by us have not been tested and approved by us. The installation and/or use of any such
products can lead to negative changes in the structural characteristics of the machine.
We shall not be liable for any damage which may be caused by non-original parts!
1 - 1
Содержание 900/51
Страница 1: ...900 51 900 57 Service Manual for the series 480 560 and 950 296 12 17607 Justieranleitung dtsch 06 95...
Страница 22: ......
Страница 23: ...Notes...