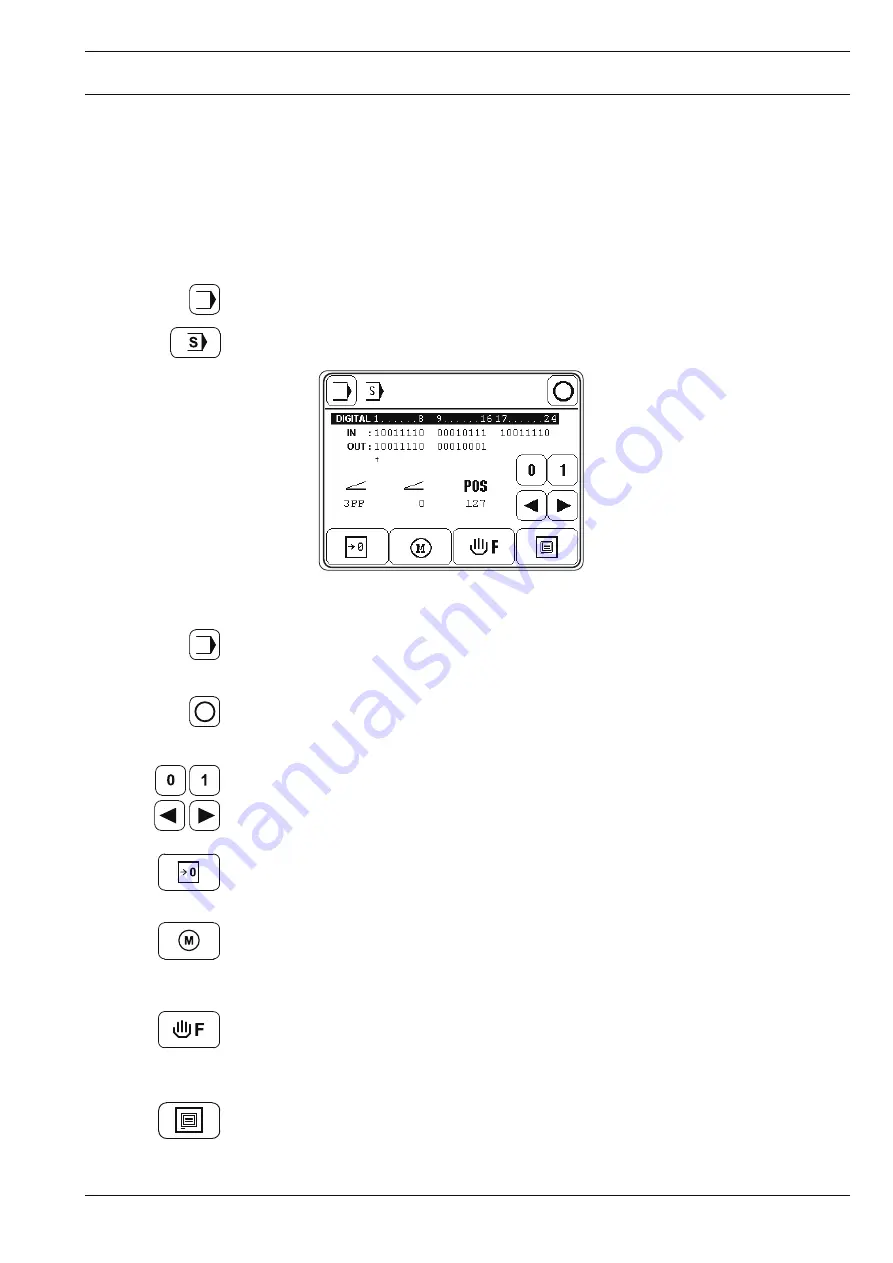
Adjustment
13 - 36
13
.11
Service menu
In the service menu information is displayed about the machine’s inputs and outputs, as well
as the values for both pedals and the balance wheel position.
In addition the following functions can also be carried out.
●
Switch on the machine.
●
Call up the input mode.
●
Call up the service menu.
Explanation of the functions
Input mode
Quit the service menu and call up the input mode.
Sewing mode
Quit the service menu and call up the sewing mode.
Set/reset outputs
Use the arrow functions to select the desired output and set "function 1" or reset "function
2".
Cold start
See
Chapter 13.09 Carry out a cold start.
Motors
After this function has been called up, the stepping motors for roller presser and feed wheel
and for the sewing motor can be moved.
Balance wheel sequence
After selecting this function the stitch formation can be checked. The movement of the
stepping motors for the stitch length depends on the position of the balance wheel.
Control panel
See
Chapter 9.13 Adjusting the control panel.
Содержание 3834-14/11
Страница 107: ...15 2 91 191 467 95 Page 1 Version 25 08 05 Circuit diagrams...
Страница 108: ...15 3 Circuit diagrams Version 25 08 05 91 191 467 95 Page 2...
Страница 109: ...15 4 91 191 467 95 Page 3 Version 25 08 05 Circuit diagrams...
Страница 110: ...15 5 Circuit diagrams Version 25 08 05 91 191 467 95 Page 4...
Страница 111: ...15 6 91 191 467 95 Page 5 Version 25 08 05 Circuit diagrams...