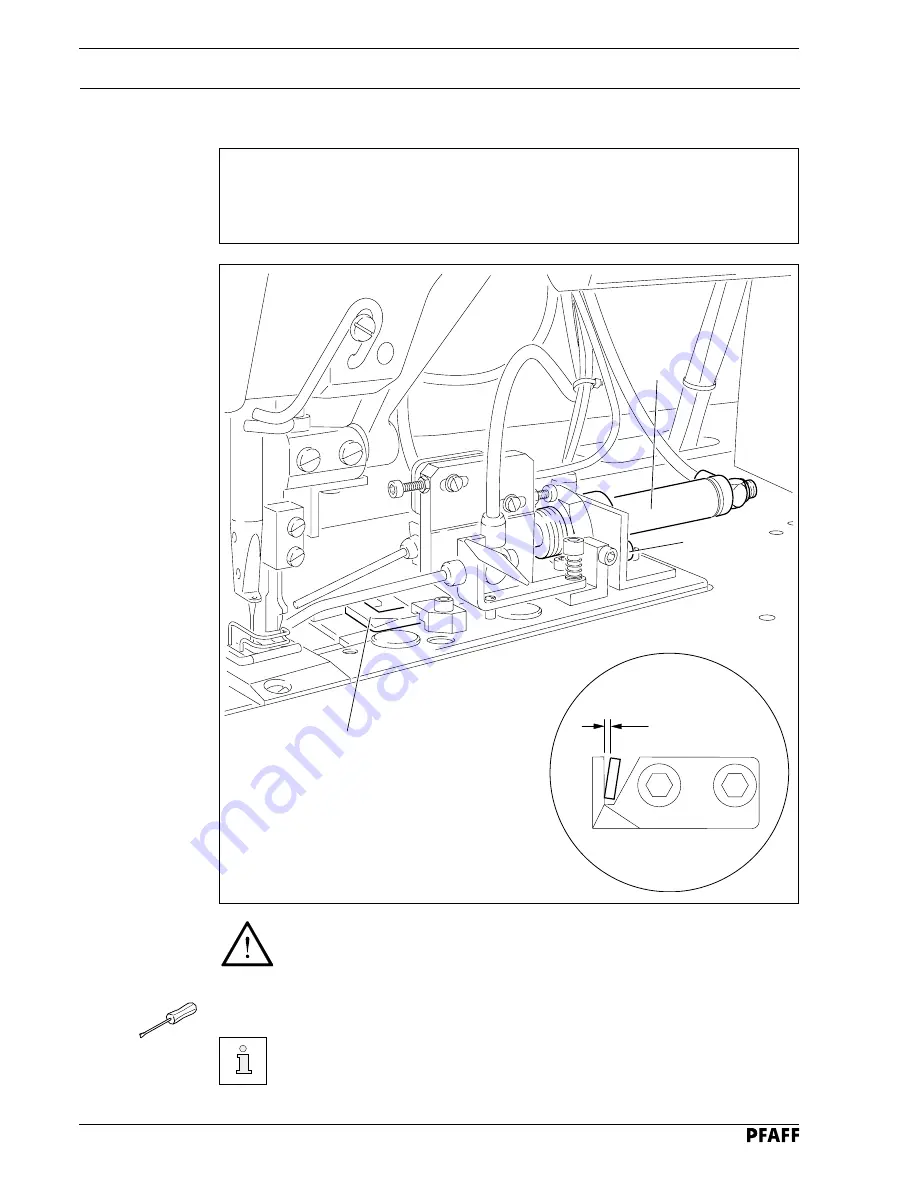
13 - 60
Adjustment
13
.08.08
Cutting pressure between the back knife and the hook knife
Requirement
1. Only as much cutting pressure as absolutely necessary should be applied.
2. After the cutting pressure has been set, the slant of the back knife must not be less
than
0.05 mm.
If the cutting pressure is too high, there is a risk of the hook knife breaking!
●
Adjust angle bracket
1
(screw
2
) according to the
requirements.
Make sure that cylinder
3
moves as far as it can go.
No material scraps should accumulate near angle bracket
1
.
Fig. 13 - 59
2
1
3
49-047
0.05 mm
Содержание 3822-1/32
Страница 129: ...Notes ...