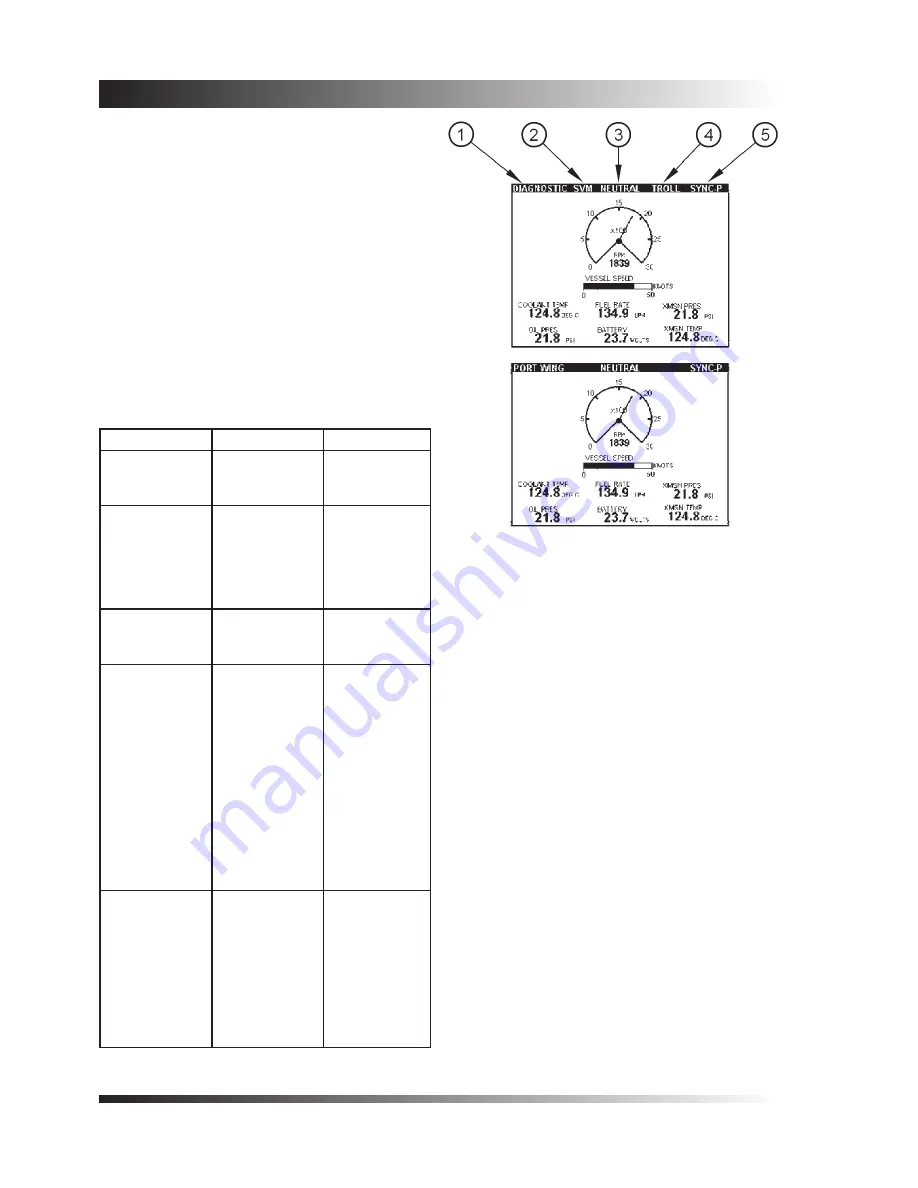
Chapter 8
N40475
Page 34
Figure 13
Vessel status bar
The status indicators are shown across the top of
the screen in reverse video and are only available on
parameter screens, except for the diagnostic icon,
which is shown on all screens.
Status items (figure 13)
Active diagnostic status of active station location.
Slow Vessel Mode (SVM) status.
Gear position
Troll mode status.
Engine synchronization status.
The Diagnostic icon overrides the Active Station
Location when there is an active diagnostic
condition.
Parameter
Status
Display Text
Slow Vessel
Mode (SVM)
SVM active
SVM inactive
SVM
No text
displayed
Gear position
Forward
AHEAD
Neutral
NEUTRAL
Reverse
ASTERN
Gear Lockout
Active
Gear L/O
Troll Mode
Troll active
Troll inactive
TROLL
No text
displayed
Engine sync
mode
Synchronized
PORT
SYNC-P
Synchronized
STBD
SYNC-S
PORT Master
Sync cruise
active
CRUISE-P
STBD Master
Sync cruise
active
CRUISE-S
Sync not active
No text
displayed
Active station*
bridge
PORT Wing
STBD Wing
Tower
Engine room
Aft station
Fly bridge
Bow station
BRIDGE
PORT WING
STBD WING
TOWER
ENG ROOM
AFT STATION
FLY BRIDGE
BOW
STATION
* If there is an active diagnostic, the word DIAGNOSTIC will be
displayed in place of the active station location.
1.
2.
3.
4.
5.
Содержание M190C
Страница 1: ...Installation Manual Part No N40475 GB Marine Power M300C M250C M216C M190C ...
Страница 2: ......
Страница 6: ......
Страница 10: ...Contents N40475 ...
Страница 18: ...Chapter 3 N40475 Page 8 ...
Страница 24: ...Chapter 4 N40475 Page 14 ...
Страница 26: ...Chapter 5 N40475 Page 16 ...
Страница 55: ...N40475 Chapter 8 Page 45 Engine wiring harness overview ...
Страница 56: ...Chapter 8 N40475 Page 46 Panel harness overview ...
Страница 57: ...N40475 Chapter 8 Page 47 Wiring diagrams Engine wiring harness 1 ...
Страница 58: ...Chapter 8 N40475 Page 48 Engine wiring harness 2 ...
Страница 59: ...N40475 Chapter 8 Page 49 Engine panels 1 ...
Страница 60: ...Chapter 8 N40475 Page 50 Interconnecting leads 1 ...
Страница 61: ...N40475 Chapter 8 Page 51 Master slave option port ...
Страница 62: ...Chapter 8 N40475 Page 52 Marine junction box ...
Страница 63: ...N40475 Chapter 8 Page 53 Master slave option starboard ...
Страница 64: ...Chapter 8 N40475 Page 54 Interconnecting leads 2 ...
Страница 65: ...N40475 Chapter 8 Page 55 Engine panels 2 ...
Страница 66: ...Chapter 8 N40475 Page 56 ...
Страница 68: ...Chapter 9 N40475 Page 58 ...
Страница 72: ...Chapter 11 N40475 Page 62 ...
Страница 76: ...Chapter 12 N40475 Page 66 ...
Страница 80: ...Chapter 12 N40475 Page 70 ...