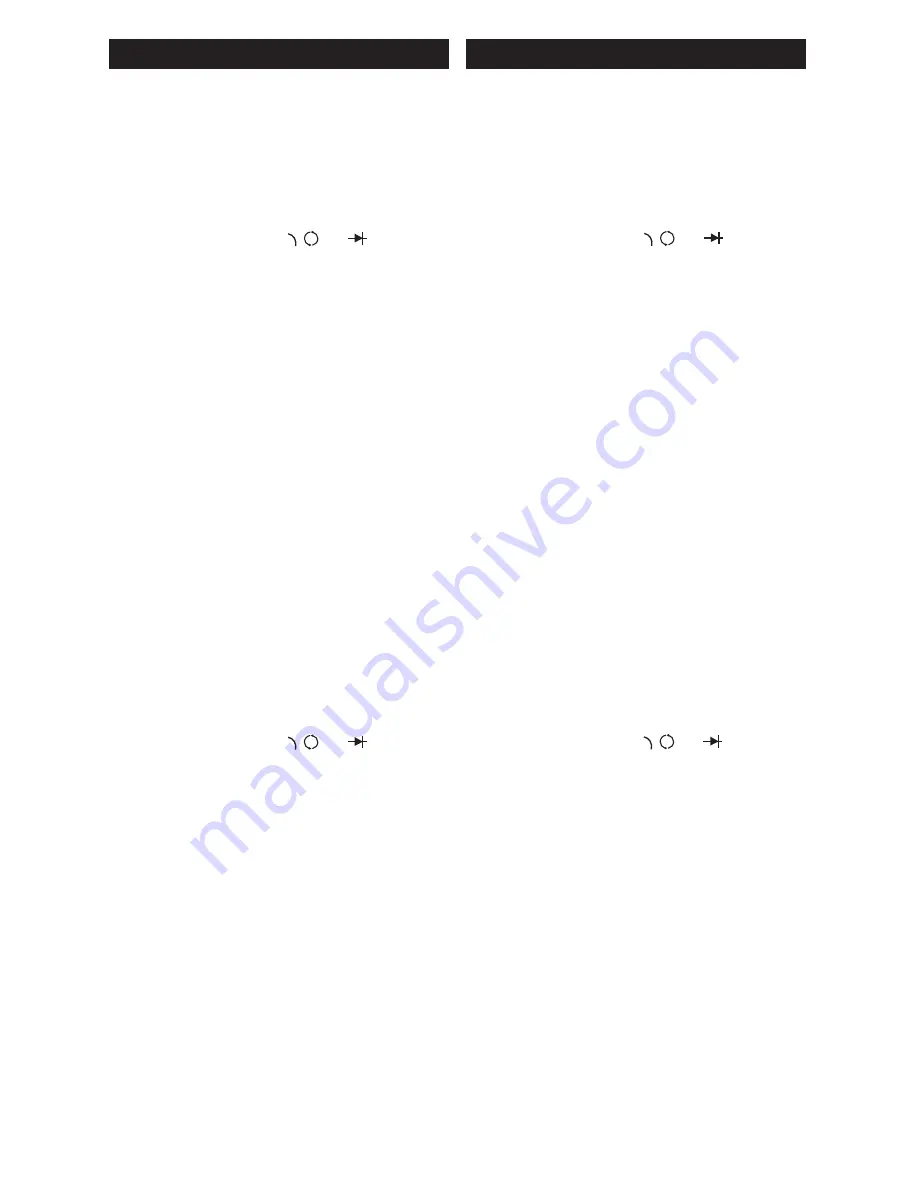
No Load Battery Test
Before testing the starting/charging system, first test
the battery to make sure it is fully charged.
1. Turn Ignition OFF.
2. Turn ON headlights for approx. 10 seconds to
dissipate surface charge.
3. Insert BLACK test lead into COM test lead jack.
4. Insert RED test lead into test lead jack.
5. Disconnect positive (+) red battery cable. Be sure
positive cable clamp is securely away from the battery.
6. Add the alligator clips and connect RED clip to
the positive (+) terminal of battery.
7. Connect BLACK clip to the negative (-) terminal
of battery.
8. Turn multimeter range selector to 20V DC range.
View voltage results on the display.
Voltage Displayed Percentage of Charge
12.75V or greater 100%
12.45V 75%
12.35V 50% Charge before any
further tests.
12.15V or less 25% Charge before any
further tests.
Cranking Battery Load Test
This test puts a load on the battery to determine if
there’s enough voltage delivered to the starter under
cranking conditions.
1. Disable ignition system so vehicle won’t start. Refer
to vehicle service manual for disabling procedure.
2. Insert BLACK test lead into COM test lead jack.
3. Insert RED test lead into test lead jack.
4. Add the alligator clips and connect RED clip to
positive (+) terminal/post of the battery.
5. Connect BLACK clip to negative (-) terminal/post
of the battery.
6. Turn meter range selector to 20V DC.
7. Crank engine for 15 seconds continuously while
observing display. An assistant may be needed so
you’re able to watch the display. Battery voltage should
be at least 9.6 volts at the end of the 15 second load
test with battery temperature at 70 degrees.
Battery Voltage Temperature
After load Test of Battery
9.6V
70 Deg. F and above
9.5V
60
Deg.
9.4V
50
Deg.
9.3V
40
Deg.
9.1V
30
Deg.
8.9V
20
Deg.
8.7V
10
Deg.
8.5V
0 Deg.
5
MECHANICAL TESTS
Engine RPM
When checking engine RPM the meter results must
be multiply by 10 to get the final figure. For
example, if your meter display reads 65 and is set
to 6 cylinder RPM, the actual engine RPM is 10
times 65 or 650 RPM.
1. Insert BLACK test lead into COM test lead jack.
2. Insert RED test lead into test lead jack.
3. Connect RED test lead to the TACH signal wire
from the DIS Ignition Module if the vehicle is equipped
with a Distributor less Ignition System. The TACH
signal wire going from the DIS module to the vehicle
engine computer. Refer to vehicle service manual for
the wiring diagram. Vehicles with distributors, connect
RED test lead to negative side of primary ignition coil.
4. Connect BLACK test lead to a good vehicle ground.
5. Turn the meters range selector to the correct
cylinder setting, 8CYL, 6CYL, or 4CYL.
Engine RPM is measurement while engine is running.
5. Take the display results and multiply by 10 to get
actual engine RPM.
Measuring Dwell
Dwell angle can be measured and set on breaker point
ignition systems. Dwell is the length of time, in
degrees, the breaker points remained closed. The
correct dwell angle is extremely important for proper
engine performance. Another application for dwell is in
testing the mixture control solenoid on GM feedback
carburetors. For dwell angle of your breaker point
ignition system connect as follows.
1. Insert BLACK test lead into COM test lead jack.
2. Insert RED test lead into test lead jack.
3. Connect RED test probe to the negative terminal
side of the primary ignition coil. Refer to your vehicles
service manual.
For measuring dwell angle on GM mixture control
solenoids the meter connections stay the same.
1. Connect RED probe lead to ground side or
computer driven side of solenoid. Refer to vehicle
service manual for solenoid location.
2. Connect BLACK test lead to a good vehicle ground.
3. Turn the meters range selector to DWELL and
the correct cylinder setting, 8CYL, 6CYL, or 4CYL.
View reading on display.
ƱⅤ
Ʌ
°
ƱⅤ
Ʌ
°
BATTERY/STARTING/CHARGING
ƱⅤ
Ʌ
°
ƱⅤ
Ʌ
°