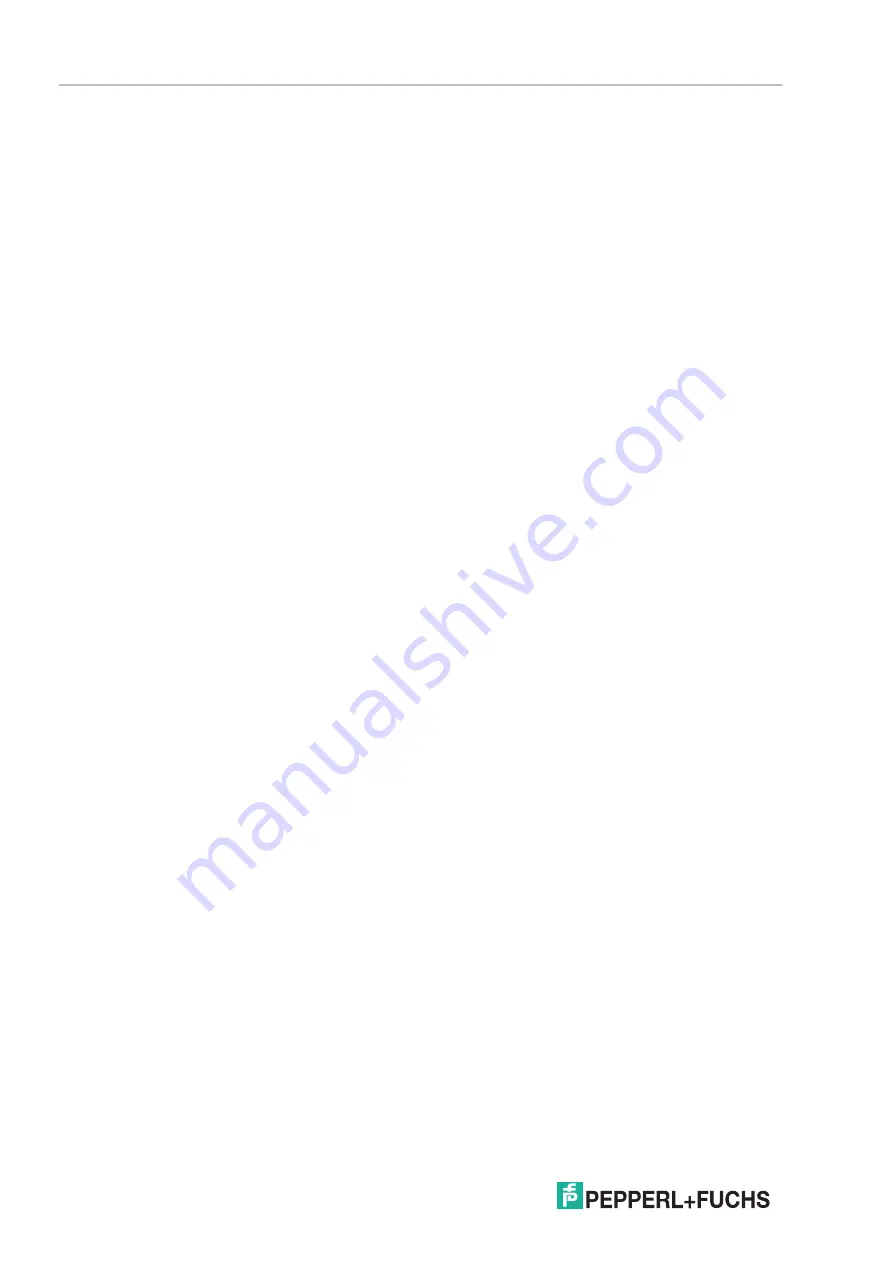
2
02
1-
04
12
Functional Safety HiD2022*, KFD2-STC5-(Ex)*, KFD2-STV5-(Ex)*
Planning
3
Planning
3.1
Assumptions
The following assumptions have been made during the FMEDA:
•
Failure rate based on the Siemens standard SN 29500.
•
Failure rates are constant, wear is not considered.
•
External power supply failure rates are not included.
•
The safety-related device is considered to be of type
A
device with a hardware
fault tolerance of
0
.
•
The device will be used under average industrial ambient conditions comparable
to the classification "stationary mounted" according to MIL-HDBK-217F.
Alternatively, operating stress conditions typical of an industrial field environment similar
to IEC/EN 60654-1 Class C with an average temperature over a long period of time
of 40
º
C may be assumed. For a higher average temperature of 60
º
C, the failure rates
must be multiplied by a factor of 2.5 based on experience. A similar factor must be used
if frequent temperature fluctuations are expected.
•
If you are using the HART function, observe that the HART signal superimposes
an analog signal on the signal line. This is negligible for slow acquisition system
(typically < 25 acquisition/s). If in doubt, use HART filters at the analog input
of the receiving device.
•
The application program in the programmable logic controller (PLC) is configured
to detect underrange and overrange failures.
•
Both channels of the 2-channel device can be used in the same safety function.
Observe that both devices use common components and that a simultaneous failure
is possible with a common cause factor of 15 %.
SIL 2 Application
•
To build a SIL safety loop for the defined SIL, it is assumed as an example that this device
uses 10 % of the available budget for PFD
avg
/PFH.
•
Since the safety loop has a hardware fault tolerance of
0
and it is a type
A
device,
the SFF must be > 60 % according to table 2 of IEC/EN 61508-2 for a SIL 2 (sub) system.
SIL 3 Application
SIL 3 can be reached if the two outputs of the device are connected to the same control
interface and evaluated if the deviation remains below 2 %.
•
To build a SIL safety loop for the defined SIL, it is assumed as an example that this device
uses 10 % of the available budget for PFD
avg
/PFH.
•
Since the safety loop has a hardware fault tolerance of
0
and it is a type
A
device,
the SFF must be > 90 % according to table 2 of IEC/EN 61508-2 for a SIL 3 (sub) system.