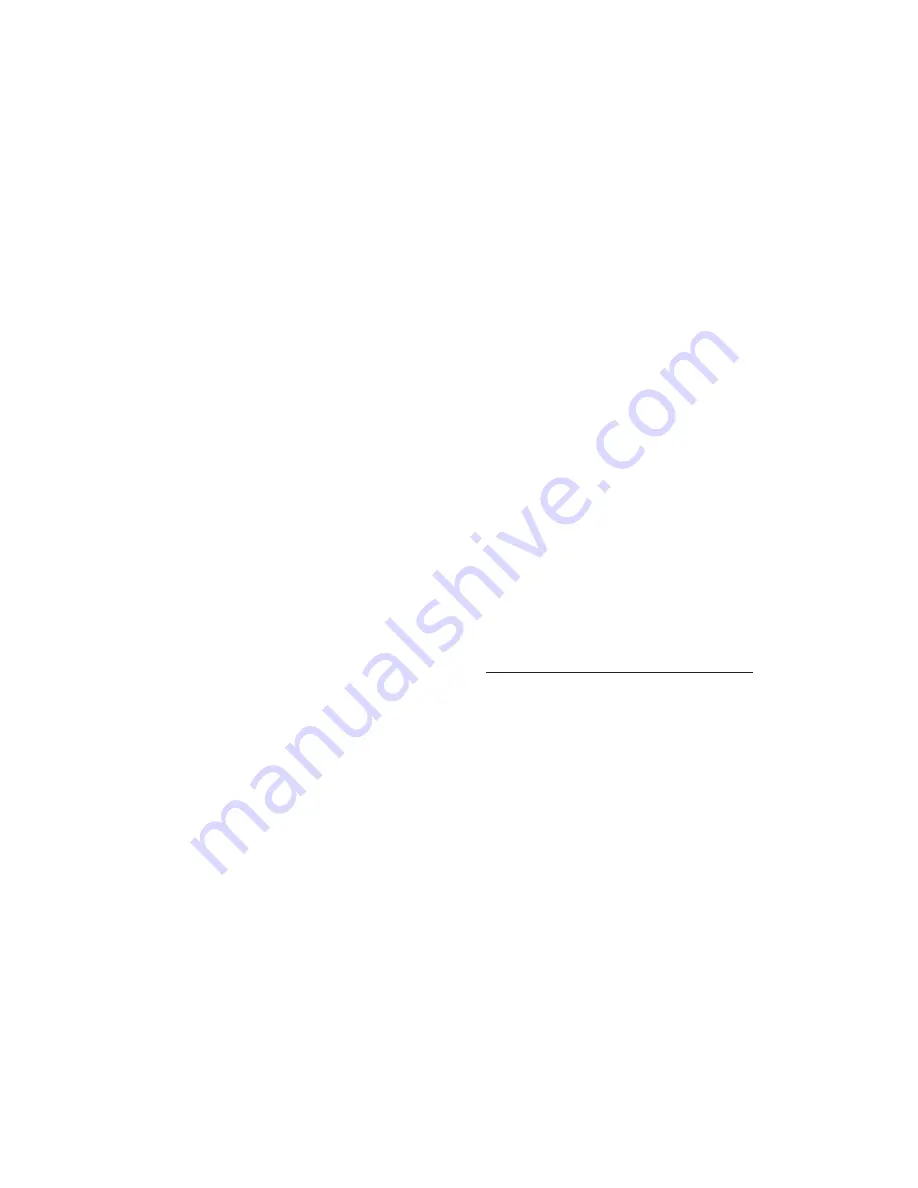
3
2
pump should be insulated from the piping with
rubber connections. Always keep pipe size as large
as possible and use a minimum of fittings to reduce
friction losses.
SUCTION PIPING
Suction pipe should be direct and as short as possible.
It should be at least one size larger than suction inlet
tapping and should have a minimum of elbows and
fittings. The piping should be laid out so that it slopes
upward to pump without dips or high points so that
air pockets are eliminated. The highest point in the
suction piping should be the pump inlet except where
liquid flows to the pump inlet under pressure. If a foot
valve must be used to keep pump primed, where liquid
flows to the pump, it may be desirable to use a check
valve in the suction line or discharge line to keep pump
primed.
To prevent air from being drawn into suction pipe
due to a suction whirlpool, the foot valve should be
submerged as least three feet below the low water
level. The suction pipe must be tight and free of air
leaks or pump will not operate properly.
DISCHARGE PIPING
Discharge piping should never be smaller than pump
tapping and should preferably be one size larger. A
gate valve should always be installed in discharge line
for throttling if capacity in not correct. To protect the
pump from water hammer and to prevent back flow, a
check valve should be installed in the discharge line
between the pump and gate valve.
ELECTRICAL CONNECTIONS
Be sure motor wiring is connected for voltage being
used. Unit should be connected to a dedicated circuit,
direct from main switch. A fused disconnect switch
or circuit breaker must be used in this circuit. Means
for disconnection of all poles must be incorporated in
the fixed wiring according with the wiring rules. Wire
of sufficient size should be used to keep voltage drop
to a maximum of 5%. All motors, unless provided with
built-in overload protection, must be protected with an
overload switch, either manual or magnetic. Single
phase 1/2 hp – 2-1/2 hp motors have built-in overload
protection.
Never install a pump without proper
overload protection. When motor is mounted on a
base plate or on slide rails for adjustment, flexible
metallic conduit should be used to protect the motor
leads. Three phase motors must have a protective
device installed in the fixed wiring.
Damaged supply cord replacement is intended to be
made by the manufacturer, its service agent or similar
qualified person to avoid hazard.
PRIMING
The pump must be primed before starting. The pump
casing and suction piping must be filled with water
before starting motor. Remove vent plug in top of
casing while pouring in priming water. A hand pump or
ejector can be used for priming when desired. When
water is poured into pump to prime, use care to remove
all air before starting motor.
STARTING
Close the discharge valve when starting the pump as
it puts less starting load on the motor. When the pump
is up to operating speed, open the discharge valve to
obtain desired capacity or pressure. Do not allow the
pump to run for long periods with the discharge valve
tightly closed. If the pump runs for an extended period
of time without liquid being discharged, the liquid in the
pump case can get extremely hot.
ROTATION
The pump must run in direction of the arrow on pump
case. All single phase motors are single rotation and
leave factory with proper rotation. Three phase motors
may run either direction. If rotation is wrong when
first starting motor, interchange any two leads to
change rotation.
STOPPING
Before stopping pump, close the discharge valve. This
will prevent water hammer and is especially important
on high head pumps.
FREEZING
Care should be taken to prevent the pump from
freezing during cold weather. It may be necessary,
when there is any possibility of this, to drain the pump
casing when not in operation. Drain by removing the
pipe plug in the bottom of the casing.
ROTARY SEAL
CT pumps are fitted only with a rotary seal. This
seal is recommended for water free from abrasives.
If liquid contains abrasives, the CT pump should not be
used.
DISASSEMBLY INSTRUCTIONS
All pumping parts can be removed from case without
disturbing the piping.
POWER SUPPLY
Open the power supply switch contacts and remove
fuses. Disconnect the electrical wiring from the motor.
VOLUTE CASE
Drain pump case by removing drain plug.
Remove the cap screws securing volute case to
pump bracket.
Pry volute case from seal plate.
IMPELLER
Remove motor end cover.
Loosen clamp holding start capacitor and swing
capacitor off to one side; do not disconnect wires.
Wrench flats are on the shaft just behind the centrifugal
switch that is screwed into the end of the shaft. Do not
remove this switch. A 7/16" open end wrench can then
be used to hold the shaft
from turning.
Grasp the impeller and turn counterclockwise
(as viewed from the pump end).