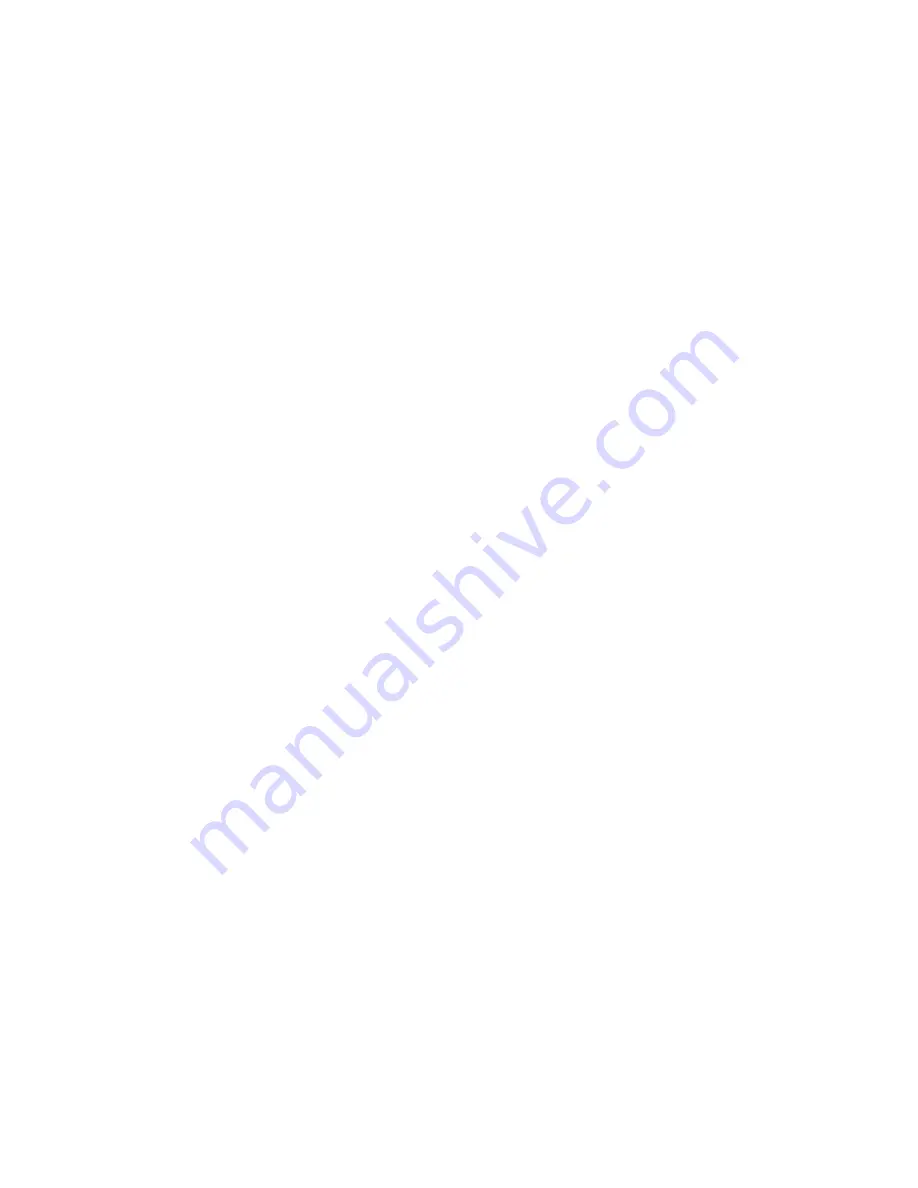
26850A005
5
5. If the pressure regulator internal bypass valve is worn, it
will allow too much of the pump capacity to be bypassed
and recirculated back to the tank. By examining the flow
from this valve with the discharge turned on, it can be
determined whether or not the valve is worn. If a heavy
flow continues when the discharge is turned on, it is
usually a good indication of a worn valve and should be
replaced.
6. Worn plunger cups, valves or valve seats will cause a
severe drop in pump capacity pressure. Worn
plunger cups are detected by water leakage past the
cups and should be replaced immediately. Water getting
into the pump crankcase will cause severe corrosion of
the bearings. Worn valves can only be detected by visual
examination of each valve assembly. Abrasive liquid will
cause wire cuts which begin as a very small groove, but
increase rapidly once the valve starts to leak through this
groove. If the valve plates are replaced as soon as they
start to show this cutting action, it will prevent the valve
seat from becoming cut in a similar manner.
7. Pump cylinder bodies withstand an extreme amount
of shock and pulsation while in operation, but if the
pump is allowed to freeze, by not being drained, the
freezing may crack the cylinder body walls in almost
any location. If the crack occurs on the suction valve or
cylinder portion of the body, it may allow a small amount
of air to enter on the suction stroke and cause noisy
operation or a decrease in pumping capacity. If the crack
develops in the walls between the cylinder cavities or
discharge valve cavity, it may allow the water to flow
from one cavity to the adjacent cavity and cause uneven
displacement.
8. The holes in the gun or nozzle discs are continually
subject to wear because of the high velocity of the liquid
through the holes. If the holes become worn, they may
allow a higher rate of discharge than the pump is able to
provide, then a drop in pressure will be noticed. This can
quickly be checked by reducing the number of nozzles
or guns while watching the amount of overflow from the
pressure regulator. If there is considerable overflow, it is
an indication that the regulator valve is worn rather than
the gun or nozzle disc.
9. Suction surge arresters should be installed on the
suction line of reciprocating pumps, 1-1/2" or 2" can
be used. A standing height of 12"-15" will be sufficient
with the top end closed by an ordinary pipe cap.
10. Water may accumulate in the pump crankcase from two
sources; leakage of the plunger cups or an accumulation
of condensation/moisture inside the crankcase due to
changes in weather or the repeated heating and cooling
of the pump. Pumps used consistently, running for a
considerable period of time to heat the oil and other
working parts, will not normally accumulate water by
condensation. Replace the plunger cups as soon as they
start to leak.
11. Worn connecting link bearings are caused by
unusual or adverse operating conditions and are
seriously affected by corrosion if water is present
in the crankcase. They will wear out from overheating
if adequate oil is not provided in the crankcase. It is
recommended to drain, clean and refill with new oil
prior to any storage period. Replace bearings as soon as
any damage is discovered to avoid possible damage to
crankshaft.
12. Low oil in the crankcase can quickly cause failure
of the pump's power end and result in extensive
repairs. Oil level should be checked periodically
during normal operation and during all maintenance
work.
13. A foaming mixture will sometimes have the same effect
as a small air leak in the suction line. This is because
various quantities of the foam are drawn through the
suction line into the pump disrupting the normal flow of
water.
14. Pressure regulators and unloading valves may become
sluggish in action due to the plunger sticking or fitting
too tightly in its cylinder. This may happen by an
accumulation of chemicals collecting in and around the
plunger or due to excessive corrosion of the plunger
parts. To check this condition, remove and clean the
plunger and cover the parts with a waterproof grease
before assembling.
15. The stuffing box nut on the unloading valve lifting post
should not be tightened to severely grip or bind the
packing on the post. Tighten this nut just enough to
prevent leakage and chatter. The pressure regulator and
unloading valves may chatter or vibrate excessively due
to an unstable operation from nozzling in the high or low
capacity range of the regulator or unloader. The range
should be at least 50% to 90% of pump capacity. With
unloader valves, nozzle capacity should be at least 20%
and not exceed 90% of pump capacity.
16. If foreign matter becomes lodged between the pump
valve and valve seat, a drastic drop in capacity and
considerable surge or pulsation will occur in the
discharge line. Examine each valve if this occurs.
17. When a pump is used for a long period of time, a
waterlogged discharge surge could cause pulsation at
the discharge. The suction should be opened into the
atmosphere to allow air to be drawn through the pump
to recharge the surge arrester. Do this with the pressure
release valve open so the pump operates at no pressure.
18. Noisy pump operation can be caused by a loose plunger
rod in the crosshead. This noise usually
has a regular cadence timed with each stroke of the
plunger. When this occurs, always replace both the rod
and the crosshead.
19. Increased preload to the crankshaft bearings will reduce
bearing life, require more power and generate more
heat, while insufficient preload may cause a knock,
timed with the crankshaft rotation. Check for loose bolts
on the crankshaft end caps or adjust shims to obtain
proper bearing preload.