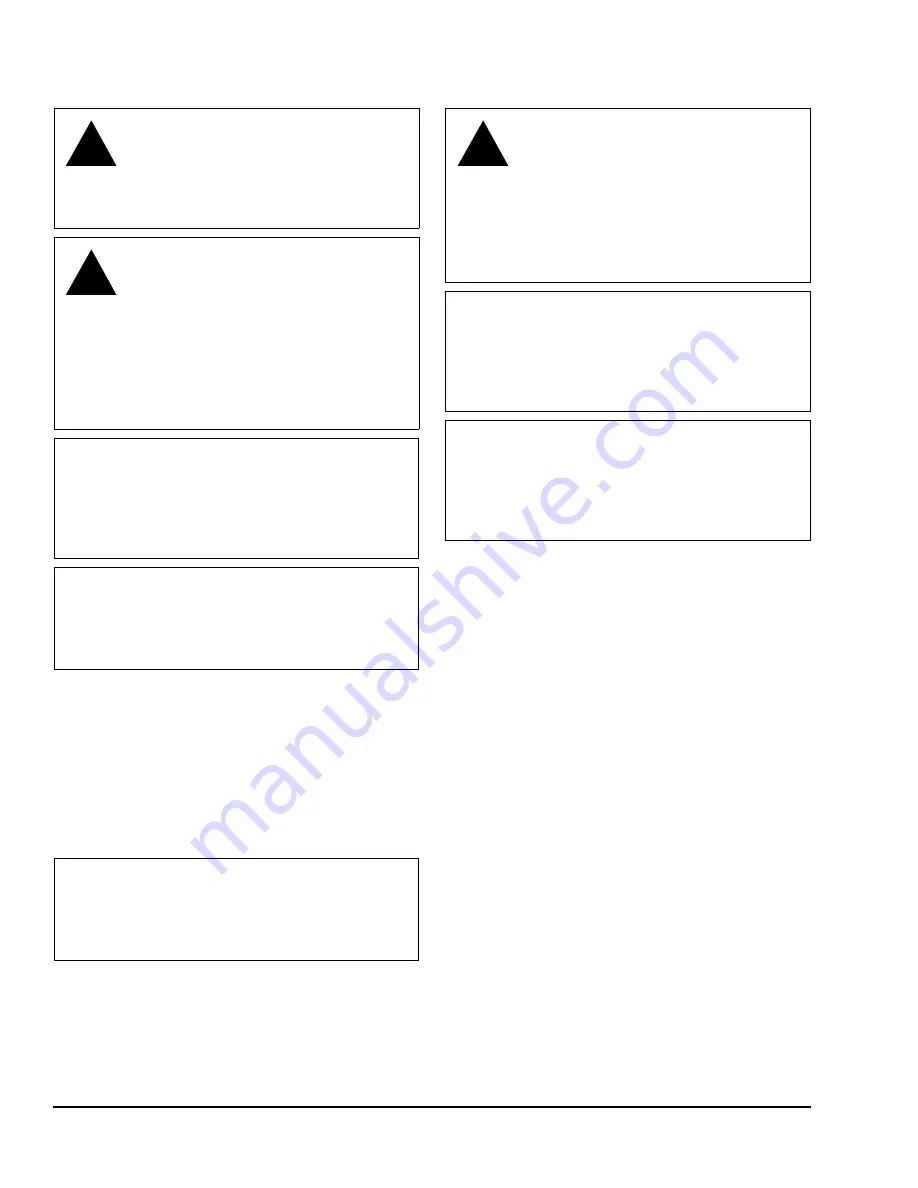
P70, P72, and P170 Series Controls for Low Pressure Applications Installation Instructions
6
Piping
P70, P72, and P170 low pressure controls are
connected to the controlled equipment by a capillary or
flexible hose (except ammonia models). Controls are
available with a variety of pressure-connection styles.
Avoid severe pressure pulsation at high side pressure
connections. Install pressure connection to pressure-
tap points away from the compressor, to minimize the
effects of pressure pulsation from reciprocating
compressors.
Setup and Adjustments
Adjustment of the P70, P72, and P170 low pressure
controls varies, depending on the model. The following
guidelines and diagrams illustrate the procedures for
adjusting these controls. Refer to the product label
inside the control cover for model number and switch
action, and check the front of the control cover to
determine if the control is an All-Range or
MICRO-SET® model. See Table 5 for switch action,
low event, and high event of the various control
models. See Figure 8 for an illustration and instructions
on control adjustments.
All-Range Controls
All-Range pressure controls have scaleplates that
display the Cut In and Cutout setpoints. (See the visible
scale on the control.) Turn the range screw to adjust
the Cut In and Cutout setpoints up or down
simultaneously while maintaining a constant pressure
differential. Turn the differential screw to adjust (only)
the low event on the left side of the scale (which
changes the differential pressure value).
MICRO-SET® Controls
MICRO-SET® low-side pressure controls have
scaleplates that display the Cut In setpoint and
Differential setting. (See visible scale on control.) Turn
the range screw to adjust the Cut In setpoint on the
right side of the scale. Turn the differential screw to
adjust the differential setting on the left side (which
changes the Cutout
pressure value).
!
CAUTION: Risk of Environmental and
Property Damage.
Avoid sharp bends in the capillary tubes.
Sharp bends can weaken or kink capillary
tubes, which may result in refrigerant
leaks or restrictions of flow.
!
CAUTION: Risk of Environmental and
Property Damage.
Coil and secure excess capillary tubing
away from contact with sharp or abrasive
objects or surfaces. Vibration or sharp or
abrasive objects in contact with capillary
tubes can cause damage that may result
in refrigerant leaks [or loss of element
charge], which may result in damage to
the environment or property.
IMPORTANT:
If the control is installed on
equipment that contains hazardous or regulated
materials such as certain refrigerants or lubricants,
you must comply with all standards and regulations
governing the containment and handling of those
materials.
IMPORTANT:
Do not apply more than 9 ft·lb
(12 N·m) of torque to the flare nuts on pressure
connection line fittings. Overtightening or applying
more than 9 ft·lb (12 N·m) of torque may cause seal
failure and will void the warranty.
IMPORTANT:
After installing the control, evacuate
pneumatic and pressure connection lines to remove
air, moisture, and other contaminants in a manner
consistent with applicable environmental regulations
and standards.
!
CAUTION: Risk of Property Damage.
Obtain and use the compressor
manufacturer’s net oil bearing pressure
specifications. If necessary, reset the
cut-out pressure difference to the
manufacturer’s specifications. Using
improper pressure settings may damage
the control, compressor, or other
controlled equipment.
IMPORTANT:
Use the pressure control settings
recommended by the manufacturer of the controlled
equipment. Do not exceed the pressure ratings of
the controlled equipment or any of its components
when checking pressure control operation or
operating the controlled equipment.
IMPORTANT:
After mounting, wiring, and
evacuating the control, attach a reliable set of
gauges to the controlled equipment, and operate the
equipment (at least) three cycles at the pressures
necessary to verify control setpoints and proper
equipment operation.