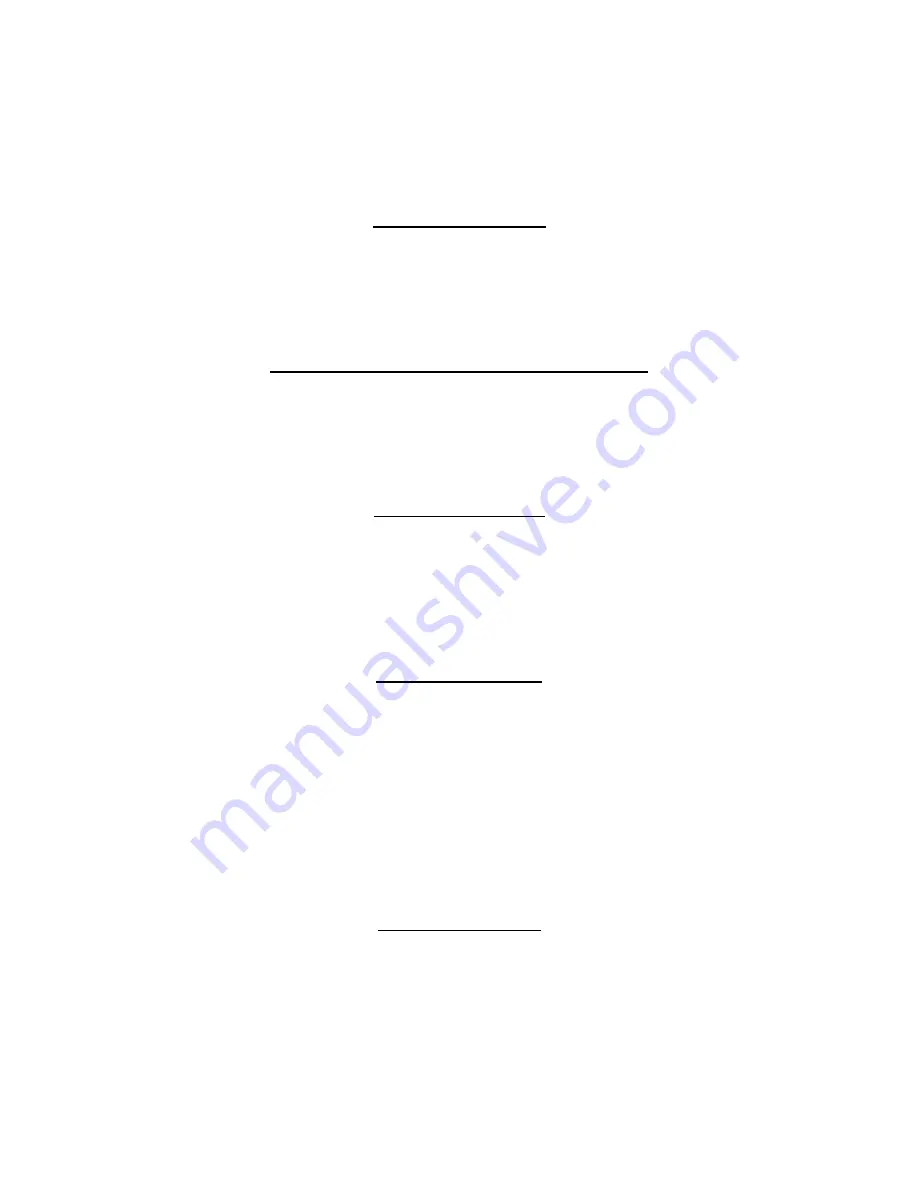
Penico Rotary Grinding Attachment
Page 2 of 4
MAGNETIC CHUCK
To operate the Magnetic Chuck insert the 6mm Allen Key into the Actuator and turn.
The magnet may be partially applied for thin work pieces.
Never leave the Allen Key in the magnet whilst the chuck rotates.
FIRST USE OF MACHINE AFTER DELIVERY
Check that the oil level is halfway up the sight glass. Connect the machine to the power
supply as described in the assembly instructions.
The magnetic chuck will require grinding true.
FLAT BASE MODEL
Contact the chuck face with a course dressed wheel and remove sufficient material to fully
clean up the face of the chuck. (Note: ensure the reversible chuck rotates contrary to the
grinding wheel). The use of coolant is recommended. Consult with your safety officer
concerning personal protection equipment.
SINE BASE MODEL
Remove the 8mm transit screw from the quadrant and replace it with the locking lever. The
'slip block' must be placed between the Sine Roller and the slip pad, ensure correct contact
is made.
Contact the chuck face with a course dressed wheel and remove sufficient material to fully
clean up the face of the chuck. (Note: ensure the reversible chuck rotates contrary to the
grinding wheel). The use of coolant is recommended. Consult with your safety officer
concerning personal protection equipment.
Refer to your inspection report for the sine centers for your model.
ANGLE GRINDING
The Sine Base Model can be set at any angle between 0-46°. A Sine Bar is fitted. It has
150mm centers. For quick angle setting a scale is engraved on the locking quadrant.
Please note that when grinding an angle the chuck will require rotating in the opposite
direction to flat grinding. When grinding on an angle it is also important that your grinding
wheel is on the center of your component. If the wheel is not on the centreline a true grind
cannot be achieved.