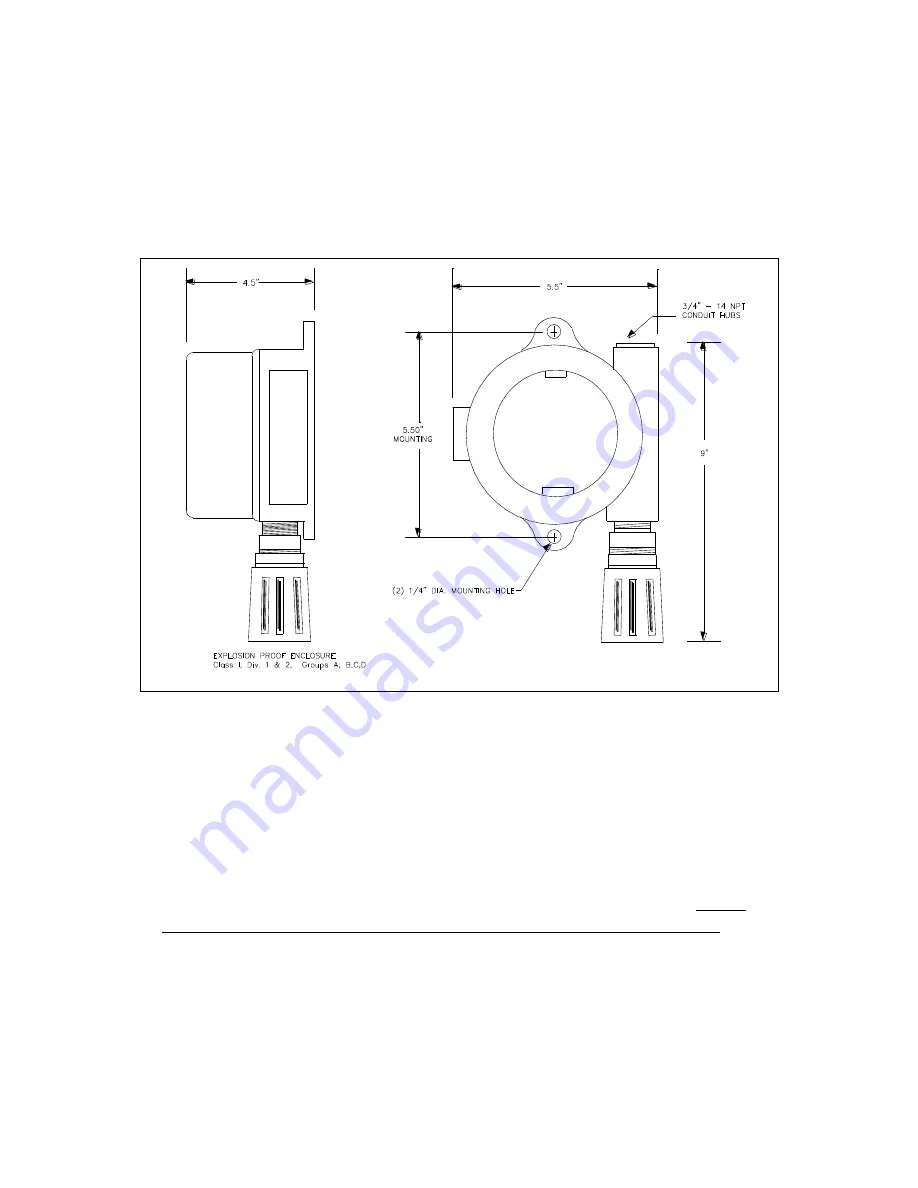
PT395 Series LEL Sensor Rev 6
12
Installation
Refer to figure 5 for model PT395 explosion proof enclosure for mounting and
conduit connection.
Figure 5. Explosion proof sensor enclosure.
Follow steps below for installation.
1.
Remove the enclosure cover and un-plug the transmitter board by simply
moving the thumb screws in counter-clockwise direction until they have loosen
up. Slowly pull the transmitter board and detach the ribbon cable.
Do not
completely un-screw or remove the thumb screws from the transmitter board.
2.
Mount the enclosure. Refer to the figure above for mounting hole dimensions.
Avoid mounting the sensor to fixtures with heavy vibrations.
3.
Using a 3 conductor cable connect the termination board with the monitor or
controller as shown in figure 3. For the cable size a reference table is provided
below.