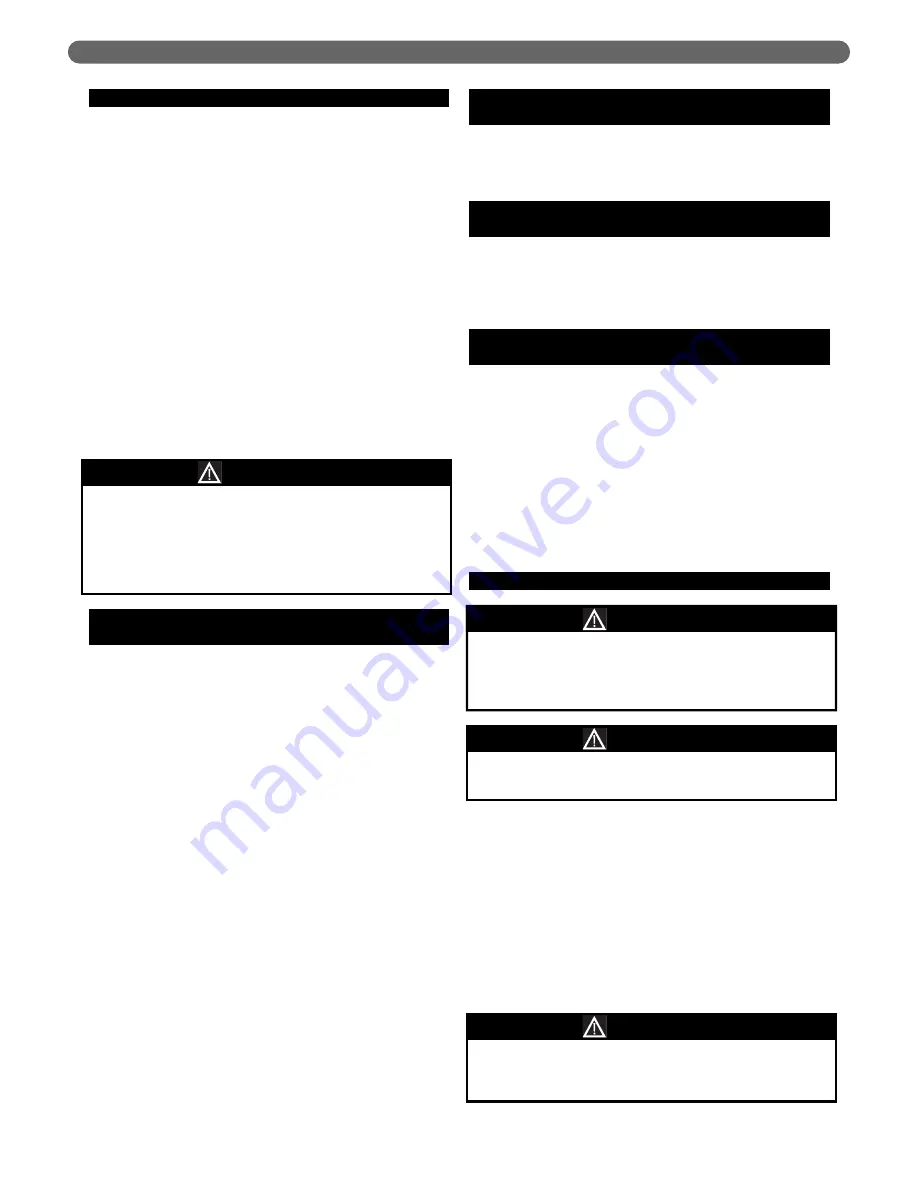
18
MAINTENANCE
A. GENERAL
1. Check pipes adjacent to cold walls or in unheated
spaces. Insulate and tape them if necessary to be
sure they can't freeze up. Keeping the water moving
at all times will reduce the likelihood of freezing.
2. If there is considerable foreign matter in the boiler
water, the boiler should be shut down and allowed to
cool, then drained and thoroughly flushed out. Drain
the boiler at the drain cock. Pipe the drain cock to a
suitable drain or containment device (if antifreeze is
used). Flush the system to remove remaining matter.
If there is evidence that hard scale has formed on the
internal surfaces, the boiler should be cleaned by
chemical means as prescribed by a qualified water
treatment specialist.
3. There must be no signs of continuous wetness at the
chimney. If signs of continuous wetness are
observed, a qualified service agency must be
consulted to modify the vent configuration to prevent
the formation of condensate, which may damage the
vent pipe.
B. DAILY MAINTENANCE (WITH BOILER
OPERATING)
Daily boiler observation can be performed by the owner.
If any potential problems are found, a qualified installer
or service technician/agency must be notified.
1. Remove any combustible materials, gasoline and
other flammable liquids and substances that generate
flammable vapors from the area where the boiler is
contained. Make certain that the boiler area has
ample air for combustion and ventilation and that
there are no obstructions to the free flow of air to
and from the boiler.
2. Observe general boiler conditions (unusual noises,
vibrations, etc.)
3. Observe operating temperature and/or pressure
gauge on the boiler. Boiler pressure should never be
higher than 5 psi below the rating shown on the
safety relief valve. The valve rating can be found on
the top of the safety relief valve. Boiler temperature
should never be higher than 250°F.
4. Check for water leaks in boiler and system piping.
C. WEEKLY MAINTENANCE (WITH BOILER
OPERATING)
1. Flush float-type low-water cut-off (if used) to remove
sediment from the float bowl as stated in the
manufacturer's instructions.
D. MAINTENANCE OF SAFETY RELIEF
VALVE
1. Check function and maintain safety relief valve as
specified by manufacturer, typically every other
month or every month, per the instructions on the
tag on the safety relief valve.
E. MONTHLY MAINTENANCE (WITH BOILER
OPERATING)
1. Check boiler room floor drains for proper
functioning.
2. Test probe type low-water cut-off (if used) by using
the Push-to-Test Button.
3. Test limit by lowering the limit set point until the
burner shuts down. When proper operation is
confirmed, return the set point to original setting.
4. Follow additional instructions in the Burner Manual
for proving the burner component operation.
F.
MAINTENANCE – ANNUAL
TO CLEAN:
1. Remove top jacket panel and flue collector cover
plate, Item 11 (Figure 2.1).
2. To thoroughly clean the boiler it must be brushed
down from the top. The target wall is made of a soft
ceramic fiber. Care must be taken not to damage this
material during cleaning.
3. Remove any scale or soot from the combustion
chamber area by vacuum cleaning or any other
available means.
Do not use this appliance if any part has been under
water. Improper or dangerous operation may result.
Immediately call a qualified service technician to
inspect the boiler and to replace any part of the
control system and any control which has been
under water.
WARNING
Entire heating system, including boiler, burner and
venting system, must be inspected at least once a
year by a qualified heating professional. Boiler is to
be cleaned at least once a year.
NOTICE
Burner mounting plate must be opened gain access
to combustion chamber for the removal of dirt and
debris.
NOTICE
Disconnect all power to the burner before accessing
combustion chamber.
WARNING