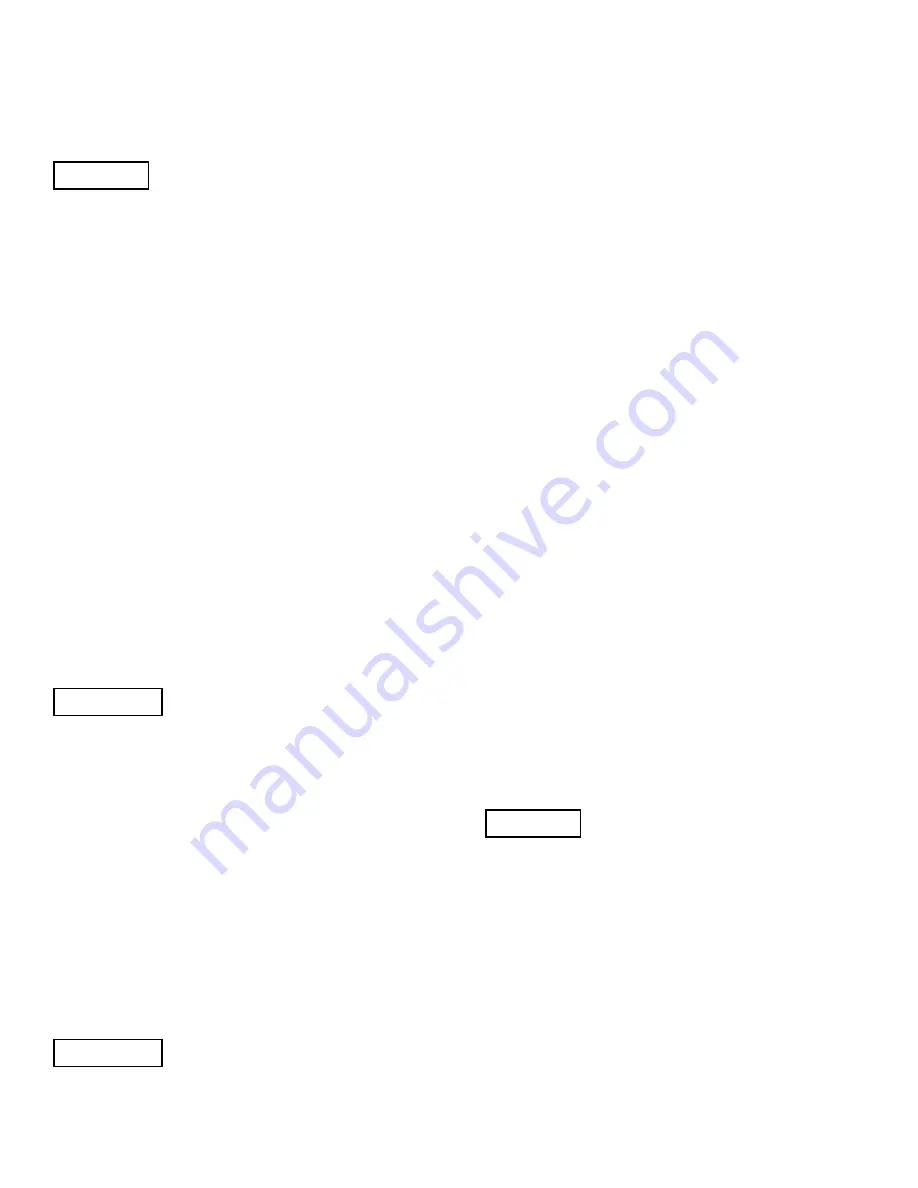
4. Using an Allen wrench, loosen the pump coupling
(23) set screw (38) and remove the coupling, thrust
collars and bail bearings (14).
5. Remove pump strainer (15) and suction plate (7).
Use care when withdrawing shaft to
prevent bending or damage. Use
proper support and two men for removal of long,
heavy shaft.
6. Pull out impeller and shaft assembly (1 and 2)
from impeller end of pump.
7. Unscrew impeller nut (40) and remove washer (39).
8. Remove the discharge pipe set screw (36), and
pull the discharge pipe (12) up out of the pump
discharge casing (6). The bottom end of the
discharge pipe is not fastened in any way; it has a
flexible connection sealed by a rubber packing ring
(13).
9. If pump has intermediate bearings (3) which need
replacing, separate the hanger pipes (10).
CLEANING:
Pump parts may be cleaned with petroleum base
solvent if desired. Metal parts (except motor) may be
soaked in solvent if necessary. Use a bristle brush
(not metal or wire) to remove tightly adhering
deposits. Wipe the exterior of motor housing with a
solvent-dampened cloth. Blow parts dry with clean,
dry, compressed air. Clean ball bearings in the
following manner:
Petroleum base cleaning sol-
vents are flammable. Open flame
or smoking by personnel in the vicinity of these
solvents is extremely hazardous and must not be
permitted. Disregard of this Warning can result in
serious bodily harm and could be fatal.
1. Place bearings in wire basket – so there is space
for cleaner to reach all parts.
2. Immerse in Stoddard solvent. Agitate basket until
old grease is thoroughly loosened and can be flushed
out.
3. Place bearing on a screened surface.
4. Using a spray gun with air filter and clean
Stoddard solvent, flush each bearing until all grease
and sludge is removed.
Never spin ball bearings. Spin-
ning
a
dry
ball
bearing
can
cause damage. Spinning any ball bearing by an air
blast can cause bearing to fly apart resulting in
possible fatal injury.
5. Blow solvent out of bearing with dry, filtered air.
6. Lubricate bearings immediately after cleansing
with light spindle oil and place them in a covered
container.
INSPECTION:
Inspect pump parts for cracks, dents,
nicks, scratches or other damage affecting service-
ability or sealing.
CAUTION
Test cleaned and oiled bearings by rotating slowly
with the hands. If worn, rough, noisy, loose or
flatted, replace with new. Do not unwrap new
bearings until ready to be installed.
REPAIR:
Remove burrs, nicks or scratches from
non-critical surfaces with a fine stone or crocus
cloth.
Replace all parts that show wear.
When ordering replacement parts always furnish data
stamped on nameplate attached to the pump. Give
the figure number, index number and part name as
shown on figure 2.
TO REPLACE GUIDE BEARINGS [3, 4, and 5]:
All
guide bearing are originally pressed in at the
factory, being held in place by the tight fit. To
remove the worn bearings they may either be sawed
in half with a steel hack saw blade and collapsed, or
threaded with a 3/4 inch tap and removed with a 3/4
inch bolt shouldered over a pipe sleeve.
New guide bearings should be pressed or lightly
tapped in place using a block of wood as a buffer.
When installing the bottom bearing (5) in pump
discharge casing, be sure that the end of bearing
nearer the impeller is approximately 1/8 inch within
the housing so that the snap ring (42) on the shaft
will not come in contact with the bearing.
WARNING
Refer motor to a repair shop author-
Ized by the motor manufacturer for
repairs. It is not recommended tat user attempt to
make repairs on this type motor under any
circumstances. Attempt to repair motor by unauth-
orized personnel voids manufacturer’s warranty.
CAUTION
ASSEMBLY:
To assemble the pump, reverse the
disassembly procedure but observe the following
precautions:
1. Be sure not metal filings or cuttings are left in the
hanger pipe. Flush out well with solvent before
inserting shaft.
WARNING
2. Before reinstalling, clean the radial thrust bearing
collars thoroughly in solvent. Be sure the collars are
placed above and below the ball bearing.
10
2899982