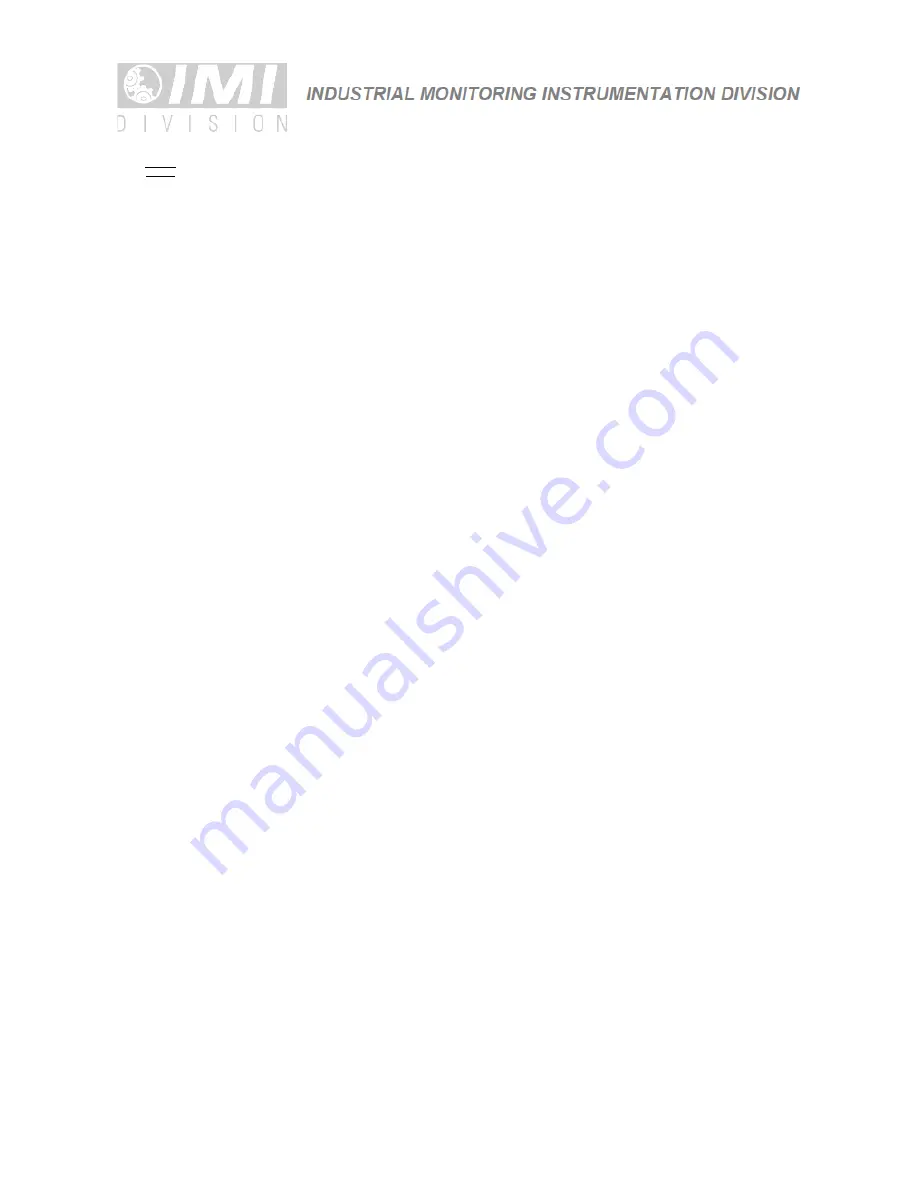
𝑓
max=
109
2𝜋𝐶𝑉
[𝐿𝑐−1]
(Equation 1)
Where, f
max
= maximum frequency (hertz)
C = cable capacitance (picofarads)
V = maximum peak output from sensor
(volts)
L
c
= constant current from signal
conditioner (mA)
10
9
= scaling factor to equate units
Note that in this equation, 1 mA is subtracted from the total
current supplied to sensor (L
c
). This is done to compensate
for powering the internal electronics. Also, note that these
are typical values only.
When driving long cables, Equation 1 shows that, as the
length of the cable, peak voltage output or maximum
frequency of interest increases, a greater constant current
will be required to drive the signal.
The nomograph on page 12 of this manual provides a
simple, graphical method for obtaining the expected
maximum frequency capability of an ICP® measurement
system. The maximum peak signal voltage amplitude, cable
capacitance and supplied constant current must be known
or presumed.
For example, when running at 100 ft (30.5 m) cable with a
capacitance of 30 pF/ft, the total capacitance is 3,000pF.
This value can be found along the diagonal cable
capacitance lines. Assuming the sensor operates at a
maximum output range of 5 volts and the constant current
available from the power supply is 2 mA, the ratio on the
vertical axis can be calculated to equal 5. The intersection of
the total cable capacitance and this ratio result in a
maximum frequency of approximately 10.2 kHz.
The nomograph does not indicate whether the frequency
amplitude response at a point is flat, rising or falling. For
precautionary reasons, it is good general practice to
increase the constant current (if possible) to the sensor
(within its maximum limit) so that the frequency
determined from the nomograph is approximately 1.5 to 2
times greater than the maximum frequency of interest.
Note:
Higher current levels will deplete battery-powered
signal conditioners at a faster rate. Also, any current not
used by the cable goes directly to power the internal
electronics and will create heat. This may cause the sensor to
exceed its maximum temperature specification. For this
reason, do not supply excessive current over short cable runs
or when testing at elevated temperatures.
5.1 CABLE CONNECTOR PROCEDURE
Care and attention to installation is essential, as the
reliability and accuracy of your system is no better than that
of the output cable.
STEP 1:
Ascertain that you have ordered the correct cable
type.
As with sensors, no cable can satisfy all applications. Special
low-noise cabling should be used with high impedance,
charge-output devices. ICP® sensors usually operate with
any ordinary tow-wire cable. Industrial applications often
require twisted/shielded cables to reduce the effects of EMI
and RFI. PTFE-jacketed cabling may be necessary to
withstand corrosive environments.
STEP 2:
Connect the cable to the accelerometer. A small
amount of thread-locking compound placed on the
connector prior to attachment helps secure the cable during
testing. In harsh environments, the connection can be
sealed with silicone rubber, O-rings, and flexible heat-shrink
tubing.
STEP 3:
Plug the connector of the cable into the mating
sensor connector. Then, holding the sensor stationary,
secure the connector in place by tightening down the
attached threaded cable sleeve.
STEP 4:
Route the cable to the signal conditioner, making
certain to stress-relieve the sensor/cable connection and
minimize motion by clamping the cable at regular intervals.
Common sense should be used to avoid physical damage
and minimize electrical noise. For instance, avoid routing
cables near high-voltage wires. Do not route cables along
floors or walkways where they be stepped on or become
contaminated. Shielded cables should have the shield
grounded at one end only, normally at the instrumentation
end.
STEP 5:
Finally, connect the remaining cable end to the
signal conditioner or readout device. To dissipate charge
that may have accumulated in the cable short the signal to
ground prior to attachment.
Содержание IMI SENSORS 622B01
Страница 17: ......