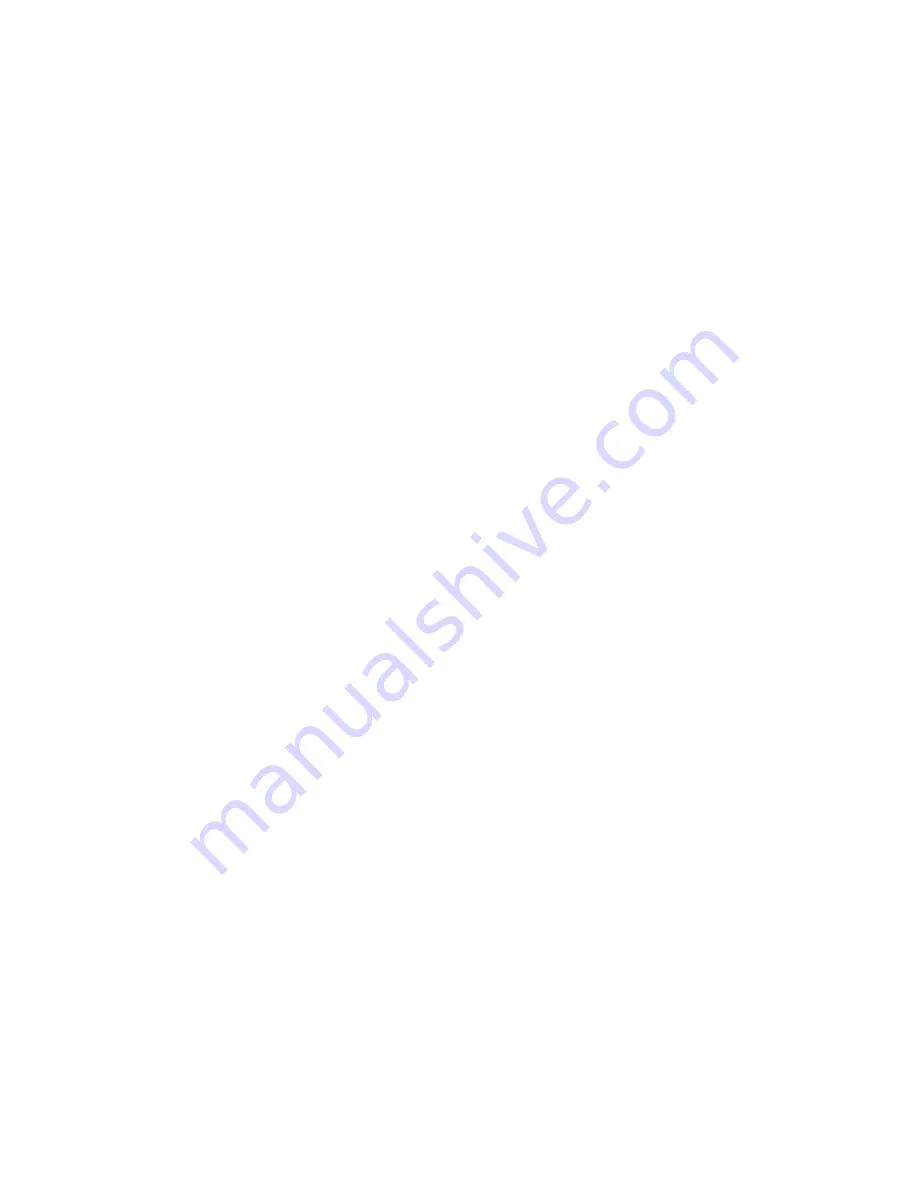
2
SECTION III
INSTALLATION
3-1
Location:
Several factors should be considered when selecting a location for the pumping unit (pump and drive). The unit
should be accessible for both inspection and maintenance. Headroom should be provided for the use of crane,
hoist or other necessary lifting devices. The pump should be located as close as possible to the liquid supply so
that the suction line is short and direct. Location should require a minimum of elbows and fittings in the
discharge line to minimize friction losses. The unit should be protected against flooding.
3-2
Mounting:
Pumps can be mounted on steel bases, raised concrete pads or floor as long as the mounting surface is level.
The mounting surface must be solid and rigid enough to support the pump unit without deflection or vibration. To
facilitate the leveling of the pump use a spirit level and short pieces of pipe in the threaded nozzles to determine
if the pump is level in all directions.
3-3
Alignment:
The pump unit has been manufactured to allow field alignment. The unit must be properly aligned at the time of
installation. Reliable trouble-free and efficient operation of a unit depends upon correct alignment.
Misalignment may be the cause of noisy pump operation, vibration, premature bearing failure, or excessive
coupling wear. Factors that may change the alignment of the pumping unit are settling of the foundation,
springing of the base plate, piping strains, a shift of the pump or drive on the foundation. When checking
coupling alignment, remember flexible couplings are not intended to be used as universal joints. The purpose of
a flexible coupling is to compensate for temperature changes and to permit end movement of the shafts without
interference with each other.
Two types of misalignment may exist: parallel misalignment and angular misalignment. Limits of misalignments
are stated in the coupling manufacturer's instructions, but should be kept to a minimum for maximum life of
equipment components.
To check coupling alignment, the following procedure should be followed:
1.
Set the coupling gap to the dimension shown on the coupling data sheet.
2.
Check for parallel misalignment by placing a straight edge across both coupling halves at four points
90
apart. Correct alignment occurs when the straight edge is level across the coupling halves at all
points.
3.
Check angular misalignment with a feeler gauge at four points 90
apart. Correct alignment occurs
when the same gauge just enters between the halves at all four points.
Angular and parallel misalignment are corrected by shifting the motor and adding or removing shims from under
the motor feet. After each change, it is necessary to recheck the alignment of the coupling halves. Adjustment
in one direction may disturb adjustment already made in another direction.
The importance of correct alignment cannot be overemphasized. Alignment should be checked and corrected
as required after:
1.
Mounting
2.
Piping is connected
3.
Pump or driver is moved for any reason.
Содержание HSC
Страница 15: ......
Страница 16: ...13 Notes ...