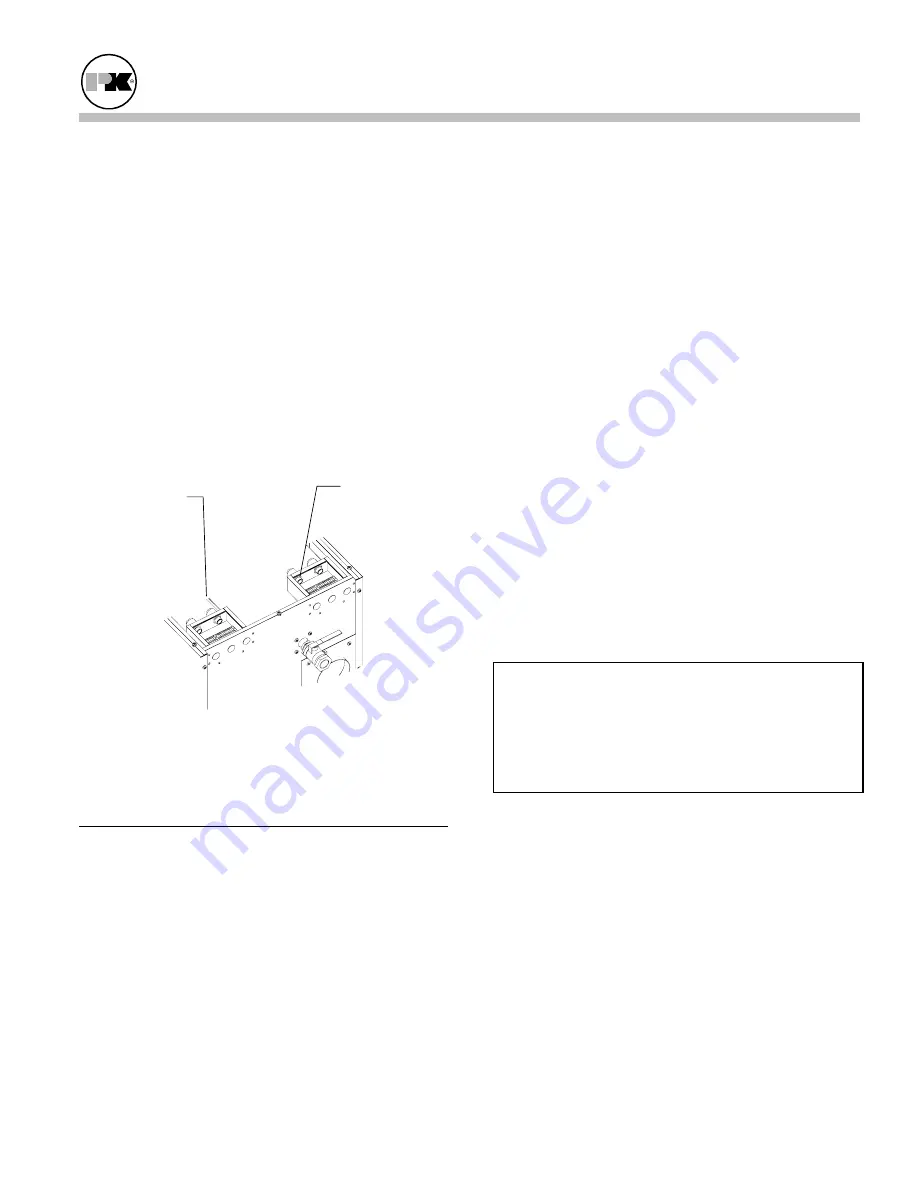
MACH® Series
Gas-Fired Boiler
Installation
Page 7
An external electrical disconnect (not supplied with
the boiler) with adequate overload protection is
required. The boiler must be grounded in accordance
with local codes or in the absence of such
requirements, in the U.S. with National Electrical
Codes, ANSI/NFPA No. 70 latest edition and in
Canada to the current Canadian Electrical Code, Part I,
CSA C22.1.
Note:
A dedicated earth ground (green wire) is
required to avoid nuisance shutdowns. Do not ground
through the conduit. It is also important that proper
polarity be maintained.
Note:
Refer to Terminal Block Assignments (Section
6.1.1).
Electrical Connections at Rear of Boiler
3.5
C
OMBUSTION
A
IR
Combustion air must be free from dust, lint, etc. The
presence of such materials in the air supplied to the
burner could cause nuisance "Low Air" shutdowns or
premature burner failure. The boiler should not be
operated during construction while the possibility of
drywall dust, demolition dust, etc. exists.
The combustion air supply must be completely free of
chemical fumes which may be corrosive when burned
in the boiler. Common chemicals which must be
avoided are fluorocarbons and other halogenated
compounds, most commonly present as refrigerants or
solvents, such as freon, trichlorethylene,
perchlorethylene, chlorine, etc. These chemicals,
when burned, form acids which quickly attack the
boiler and the boiler stack. The result is improper
combustion and premature boiler failure.
Provisions for combustion and ventilation air must be
in accordance with Section 5.3, Air for Combustion
and Ventilation, of the National Fuel Gas Code,
ANSI Z223.1, latest edition, or applicable provisions
of the local building codes. In Canada, combustion
air openings shall comply with CSA B.149
Installation Code. The formula is 1 sq. in. per 1,000
Btu/hr of gas input not less than 100 sq. in. The
location shall be neither more than 18", nor less than
6" above the floor level.
The boiler room shall be provided with two openings
to ensure adequate combustion air and proper
ventilation. One opening should be 6 to 12 inches
above the floor and the other 6 to 12 inches below the
ceiling, preferably on opposite walls. The size of
each opening is determined by whether air is taken
from inside or outside the building. In Canada,
ventilation air openings shall be at least 10% of the
cross sectional area required for combustion air, but
not less than 10 square inches. It is to be located at
the highest practical point communicating with
outdoors.
WARNING!
Under no circumstances shall the boiler room
ever be under a negative pressure. Particular
care should be taken when exhaust fans,
compressors, air-handling units or other
equipment may rob air from the boiler.
3.5.1 Air Inlet Requirements
If air is taken directly from outside the building, each
opening (minimum of two) should have a net free
area of 1 square inch for each 4,000 Btu per hour of
total boiler input. For instance, 112.5 square inches
are required for 450,000 Btu per hour input.
When air is taken from the outdoors through a
vertical duct, 1 square inch per 4,000 Btu per hour is
required. If a horizontal duct is used, 1 square inch
per 2,000 Btu per hour is required, i.e., 225 square
inches for 450,000 Btu per hour input.
Low Voltage
Control Junction
Box
120 Volt
Electrical Control
Junction Box
Содержание MACH-05
Страница 2: ...MACH Series Gas Fired Boiler...
Страница 43: ...MACH Series Gas Fired Boiler Parts and Technical Support Page 39 6 1 2 Wiring Series C 300...
Страница 44: ...MACH Series Gas Fired Boiler Parts and Technical Support Page 40 6 1 3 Wiring Series C 450...
Страница 45: ...MACH Series Gas Fired Boiler Parts and Technical Support Page 41 6 1 4 Wiring Series C 750 900 1050...
Страница 56: ...MACH Series Gas Fired Boiler Appendix Page 52 8 0 APPENDIX Date Hi Low Fire O2 CO CO2 Stack Temp Action By...