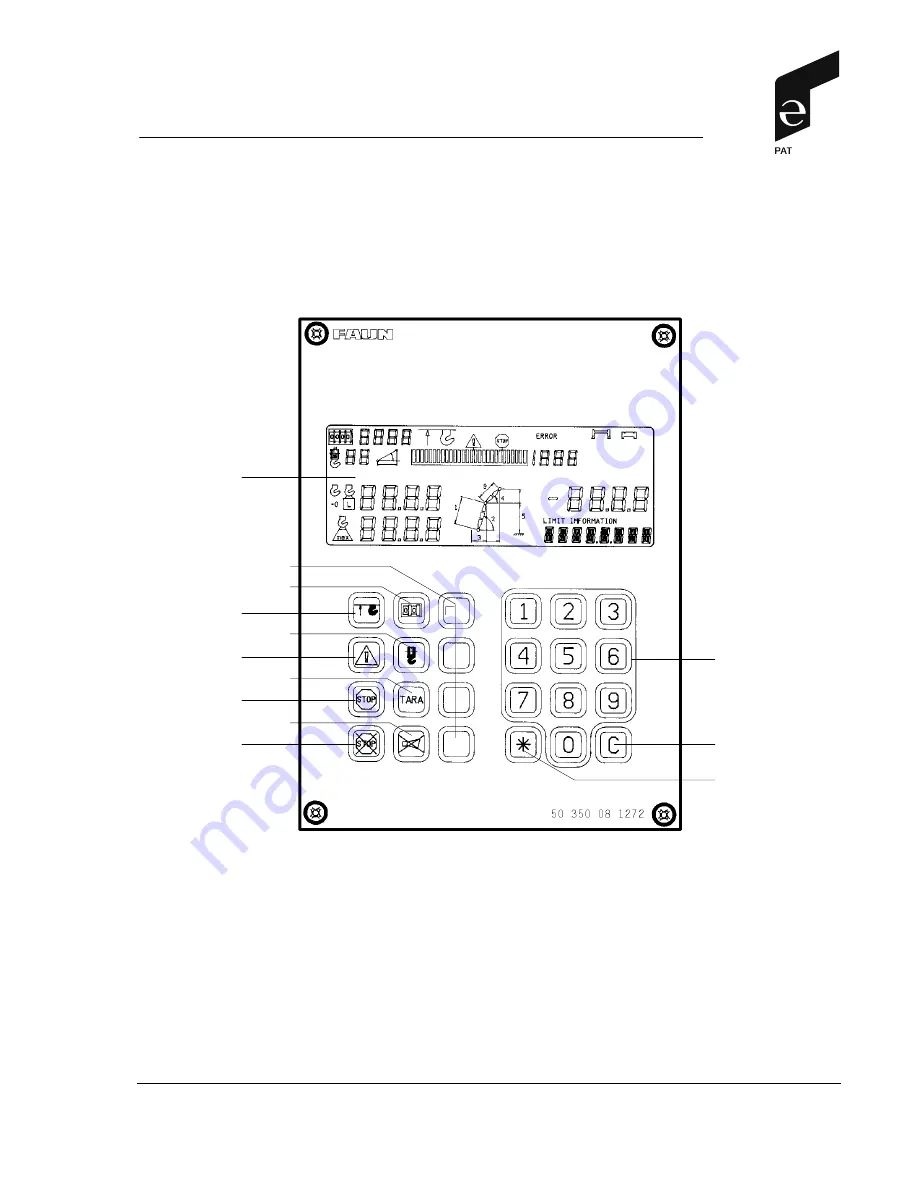
Control Identification
© 1996-2001 by PAT GmbH
∙
D-76275 Ettlingen
∙
Hertzstr. 32 - 34
∙
++49 (0) 7243 709-0
∙
FAX ++49 (0) 7243 709-141
7
19_1272E.DOC / 2001-04-02 / Rev. C / ko.
3.3
CONTROL IDENTIFICATION
Figure 1 illustrates the controls and displays of the DS 350 safe load indicator. The numbers of the
illustration correspond to the numbers in the following list which describes the function of each con-
trol:
1
data display, multi functional
2
A2B switch pilot lamp
3
Prewarning lamp (load moment)
4
Overload lamp (load moment)
5
Pilot lamp "Bridging LMI"
6
Button "operating mode"
7
Button "Reeving"
8
Button "Taring"
9
Button "Alarm off"
(10)
without function (evtl. symbol w/o signification)
(11)
without function
(12)
without function
(13)
without function
14
Numerical keys 0...9
15
Key "Acknowledgment"
16
Key "Asterix" (evtl. for comma inputs)
14
6
1
2
3
4
5
7
8
9
10...13
15
16
fig. 1
(standard)