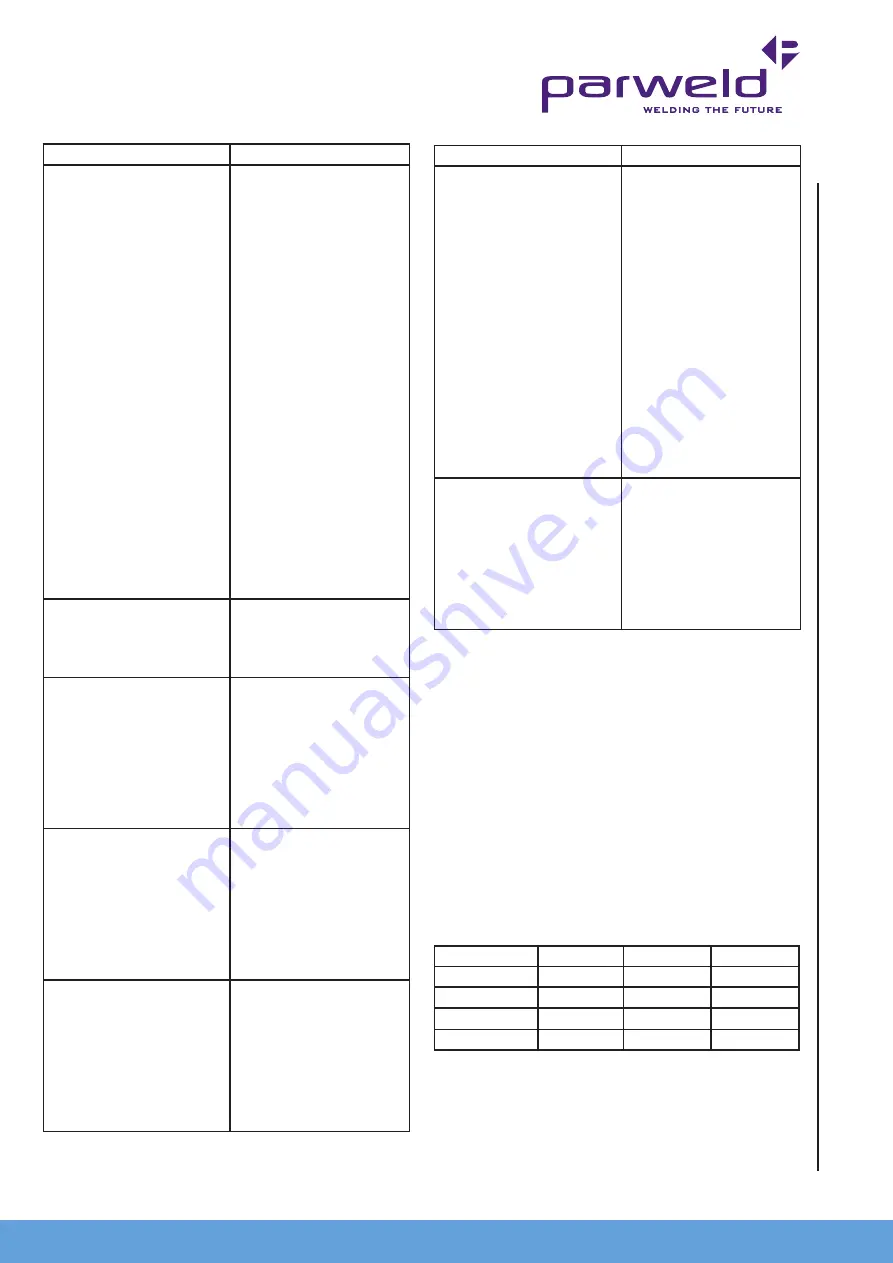
www.parweld.co.uk
11
8.0 Accessories
8.1 Drive rolls
Wire
0.8/1.0
1.0/1.2
1.2/1.6
Mild steel
DR4V0810
DR4V1012
DR4V1216
Stainless Steel
DR4V0810
DR4V1012
DR4V1216
Aluminium
DR4U0810A
DR4U1012A
DR4U1216A
Flux Cored
DR4K0810
DR4K1012
DR4K1216
Problem
Cause/Corrective Action
Excessive Spatter - scattering of
Molten metal particles that cool
to solid form near weld bead.
Wire feed speed too high.
Select lower wire feed speed.
Voltage too high. Select lower
voltage range.
Electrode extension (stick out)
too long. Use shorter electrode
extension (sick out).
Work piece dirty. Remove all
grease, oil, moisture, rust,
paint, undercoating, and dirt
from work surface before
welding.
Insufficient shielding gas at
welding arc. Increase flow of
shielding gas at regulator/flow
meter and/or prevent drafts
near welding arc.
Dirty welding wire. Use clean,
dry welding wire. Eliminate
pickup of oil or lubricant on
welding wire from feeder or
liner.
Wire feed unit operates but no
gas flow .
Gas cylinder empty
Gas regulator closed
Faulty solenoid
Restriction in torch cables
Wire feed unit operates, but
does not feed
Insufficient drive roll pressure
Incorrect drive rolls
Excessive wire spool brake
tension
Incorrect liner
Blocked liner
Bird nesting
Burn back
Bird nesting
Excessive feed roll pressure
Incorrect or blocked liner
Incorrect contact tip size
Contact tip overheating
Restriction in torch cable
Misaligned drive rolls or wire
guides
Excessive cable kinkage
Burn back
Improper voltage setting
Improper stick out
Erratic wire feed
Incorrect or blocked liner
Contact tip overheating
Excessive cable kinking
Adjust the burn back control
correctly
Problem
Cause/Corrective Action
Erratic Wire Feeding or Arc
Improper drive roll tension
Improper drive roll size
Worn drive rolls
Incorrect or blocked liner
Incorrect wire guide size
Misaligned drive rolls or wire
guide
Gaps at liner or wire guide
junctions
Incorrect contact tip size
Contact Tip overheating
Spatter adhesion on exit
geometry of tip bore
Excessive cable kinkage
Poor earth or cable
connections
Weld joint area dirty
Yellow temperature light
illuminates
Power source has over heated
leave the machine running
to allow it to cool down.
Ensure entry and exit vents
on machine are clear and
machine has a good supply of
cooling air.
Reduce operating duty cycle
and or amperage.
Содержание XTM 304C
Страница 1: ...OPERATOR MANUAL ISSUE 1 XTM 304C...