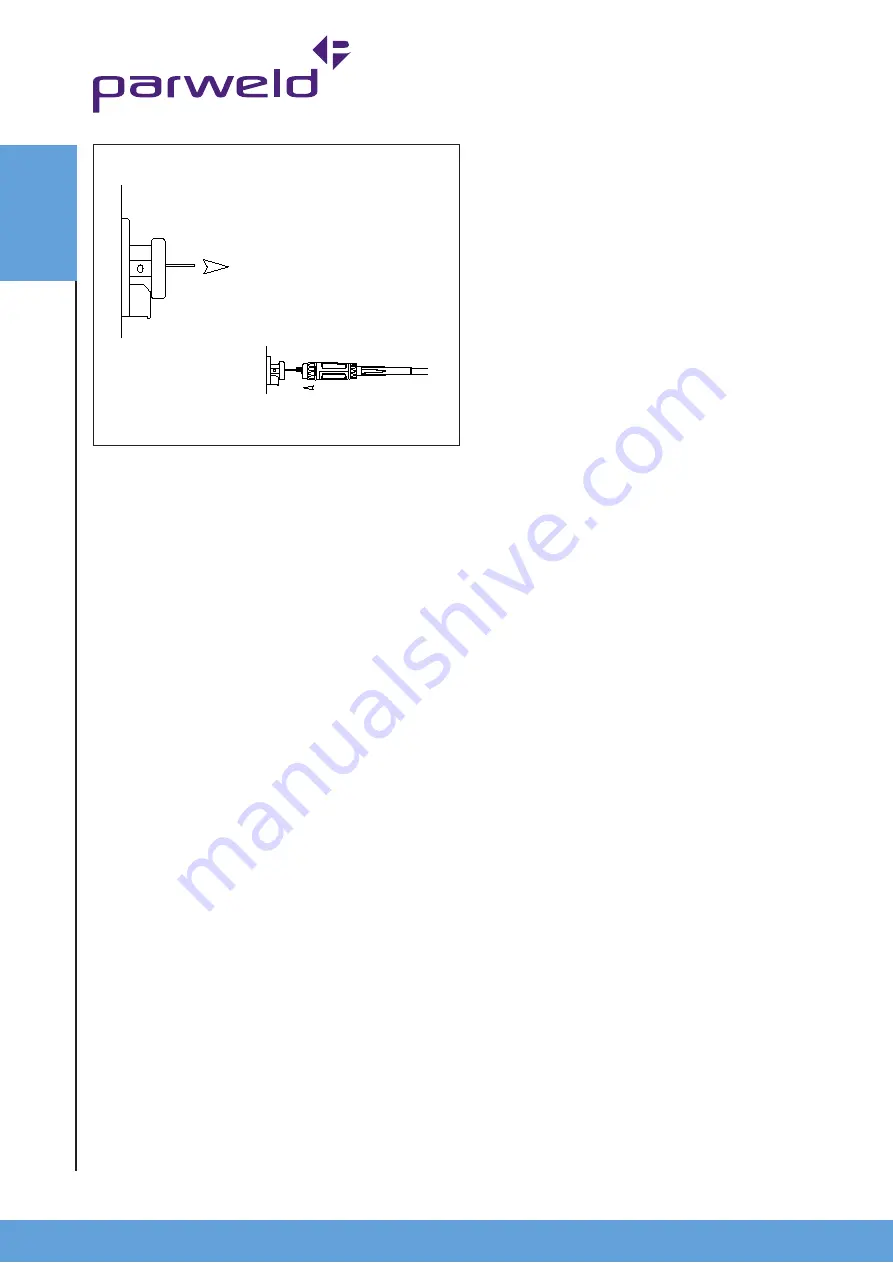
www.parweld.co.uk
8
Note; To aid the initial location of a new torch and to prevent
damage to the gas nipple O-ring a very light application of
grease to the O Ring is beneficial.
4. Keeping the torch as straight as possible, use the torch trigger
to feed the electrode wire 50mm from the end of the liner
conduit.
5. Once the electrode wire has stopped, refit the tip adaptor,
diffuser, contact tip and gas nozzle.
6. Trim the electrode wire to within 5mm of the face of the nozzle,
this will facilitate jolt free arc initiation.
7. Press the gas purge button and check the gas flow is adequate
for your application.
8. An inexpensive flow meter is available from Parweld reference
806001.
5.4.4 Work return lead connection
Insert the work return lead connector into the Negative Twist lock
receptacle on the front panel of the machine and twist it clockwise
until tightly secured.
Connect the earth clamp to the work piece as close as possible to
the point to be welded and ensure that a good electrical connection
is created to bare metal.
5.4.5 Shielding gas connection
1. Using the gas hose supplied connect the hose to the gas inlet
connection on the rear of the machine and tighten it with a
spanner.
2. Connect the opposite end of the gas hose to the output
connection of a gas regulator capable of supplying the correct
gas flow for the welding operation.
Note The gas cylinder should be secured to ensure it cannot
fall.
6.0 Operation
WARNING
When using an open arc process, it is necessary to use correct
eye, head, and body protection.
6.1 MIG Welding
Synergic MIG Welding
Controls used
(7) 2T/4T sets the trigger to momentary or latching for longer welding
runs.
(5) Wire size selector toggle through the different wire sizes to match
the wire size installed in the machine
(6) Material type select the material type that matches your material.
(3) Current control. Adjust the current to the desired level this will
automatically adjust the welding voltage for you. If the power level is
to low then increase the current, if the power level is too high then
decrease the current.
If you wish to trim the voltage control to fine tune the parameters
you can increase or decrease the voltage independently using (4)
the voltage adjustment. You may also wish to adjust the inductance
which will alter the arc from soft to hard. (12)
Manual Welding
(5) Wire size selector toggle through the different wire sizes to the
SPL setting
(4) Voltage adjustment knob, allows the adjustment of welding
voltage
(3) Current adjustment knob controls the wire feed speed
(12) Inductance adjustment knob controls the smoothness of the arc
Using primarily the Voltage and the Current (wire speed) knobs,
adjust until you reach a stable arc condition.
Note: Check that drive rolls, and torch parts are correct for the
wire size and type being used.
1.
The optimum idle roll pressure varies with type of wire, wire
diameter, surface conditions, lubrication, and hardness. As a
general rule, hard wires may require greater pressure, and soft,
or aluminium wires, may require less pressure than the factory
setting. The optimum idle roll setting can be determined as
follows:
2. Press end of torch against a solid object that is electrically
isolated from the welder output and press the torch trigger for
several seconds.
3. If the wire “bird nests”, jams or breaks at the drive roll, the idle
roll pressure is too great. Back the adjustment knob out 1/2
turn, run new wire. If the only result was drive roll slippage,
loosen the Hand nut on the central connector and pull the torch
forward about 6” (15cm) away from the power source. There
should be a slight waviness in the exposed wire. If there is no
waviness, the pressure is too low. Tighten the adjustment knob
1/4 turn, reinstall the torch cable and repeat the above steps.
6.1.1 Feeding wire electrode
1. When triggering, the electrode and drive mechanism are
electrically “LIVE” relative to work and ground and remain
“LIVE” several seconds after the torch trigger is released.
WARNING
When using an open arc process, it is necessary to use correct
eye, head, and body protection.
OPERA
TION
Fig 1
Fig 2
Содержание XTM 161i
Страница 1: ...OPERATOR MANUAL XTM 161i XTM 201i ISSUE 2...