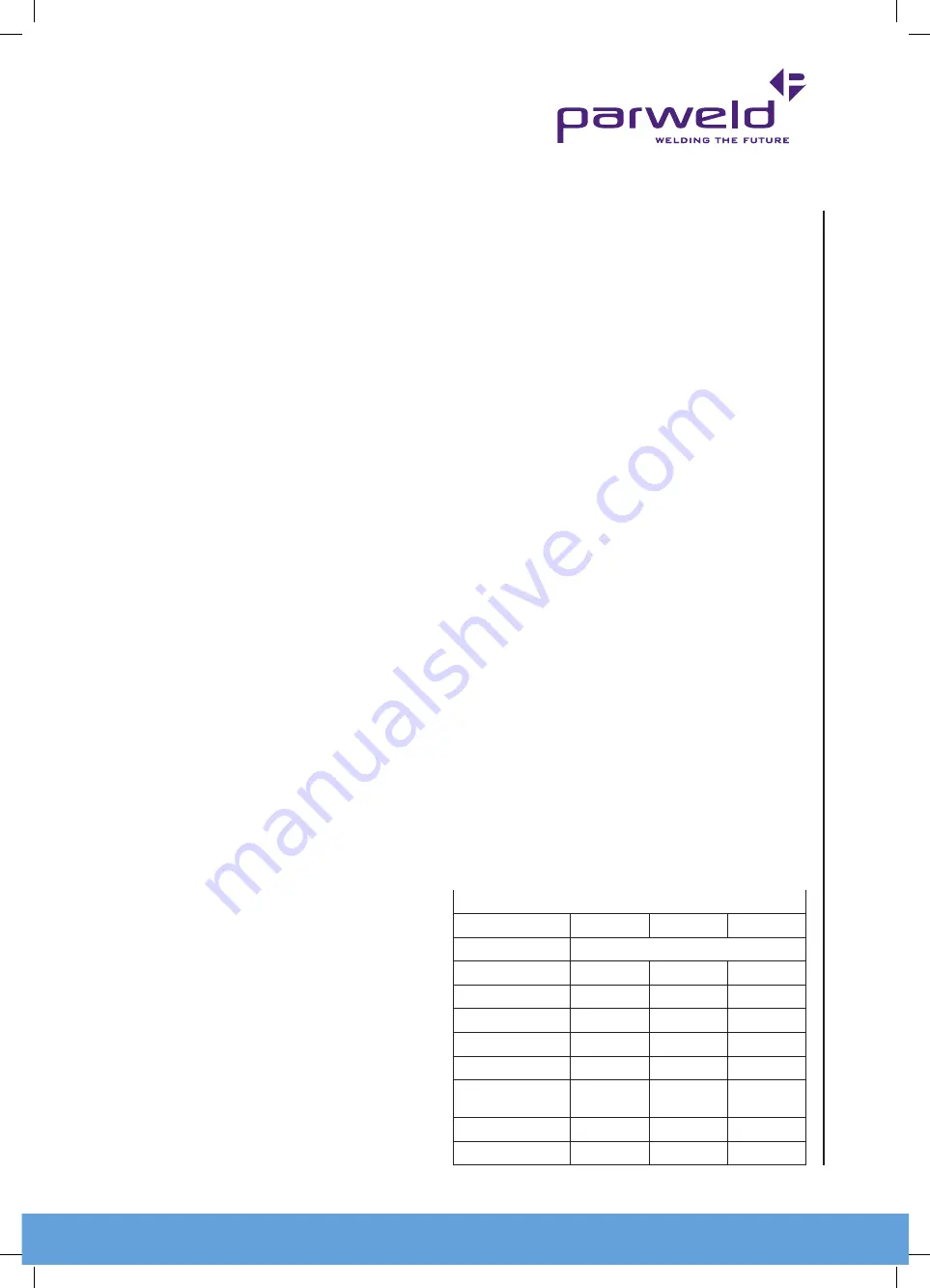
www.parweld.com
www.parweld.com
5
WELDING can cause fire or explosion.
Remove all flammables within 10m of the welding arc. If this is not
possible, tightly cover them with approved covers.
Do not weld where flying sparks can strike flammable material.
Protect yourself and others from flying sparks and hot metal.
Be alert that welding sparks and hot materials from welding can
easily go through small cracks and openings to adjacent areas.
Watch for fire, and keep a fire extinguisher nearby. Be aware that
welding on a ceiling, floor, bulkhead, or partition can cause fire on
the hidden side.
Do not weld on closed containers such as tanks, drums, or pipes,
unless they are properly prepared according to local regulations
Connect work cable to the work as close to the welding area as
practical to prevent welding current from travelling along, possibly
unknown paths and causing electric shock, sparks, and fire hazards.
Cut off welding wire at contact tip when not in use.
Wear oil-free protective garments such as leather gloves, heavy
shirt, cuffless trousers, high shoes, and a cap. Remove any
combustibles, such as a butane lighter or matches, from your person
before doing any welding.
FLYING METAL can injure eyes.
Welding, chipping, wire brushing, and grinding cause sparks and
flying metal. As welds cool they can throw off slag. Wear approved
safety glasses with side shields even under your welding helmet.
BUILDUP OF GAS can injure or kill.
Shut off shielding gas supply when not in use. Always ventilate
confined spaces or use approved air-supplied respirator.
HOT PARTS can cause severe burns.
Do not touch hot parts with bare handed.
Allow cooling period before working on gun or torch.
To handle hot parts, use proper tools and/or wear heavy, insulated
welding gloves and clothing to prevent burns.
MAGNETIC FIELDS can affect pacemakers.
Pacemaker wearers keep away.
Wearers should consult their doctor before going near arc welding,
gouging, or spot welding operations.
NOISE can damage hearing.
Noise from some processes or equipment can damage hearing.
Wear approved ear protection if noise level is high.
Shielding gas cylinders contain gas under high pressure.
CYLINDERS can explode if damaged.
Protect compressed gas cylinders from excessive heat, mechanical
shocks, physical damage, slag, open flames, sparks, and arcs.
Install cylinders in an upright position by securing to a stationary
support or cylinder rack to prevent falling or tipping. Keep cylinders
away from any welding or other electrical circuits. Never drape a
welding torch over a gas cylinder. Never allow a welding electrode to
touch any cylinder. Never weld on a pressurized cylinder - explosion
will result. Use only correct shielding gas cylinders, regulators,
hoses, and fittings designed for the specific application; maintain
them and associated parts in good condition.
Turn face away from valve outlet when opening cylinder valve.
Use the right equipment, correct procedures, and sufficient number
of persons to lift and move cylinders.
Read and follow instructions on compressed gas cylinders,
associated equipment, and Compressed Gas Association (CGA)
2.0 Product Description
The XTE 171C, 181C and 201C is a complete semiautomatic
constant voltage DC arc welding machine built to meet CE
specifications. It combines a constant voltage power source and
a constant speed wire feeder to form a reliable high-performance
welding system. A simple control scheme, consisting of voltage and
wire feed speed controls, provides versatility with ease of use and
accuracy. Other features include wire reel spindle with adjustable
brake for 15kg wire spools (300mm), integrated gas cylinder
mounting undercarriage, an adjustable
3.0 Technical
Specifications
The XTE 171C, 181C and 201C are compact type machines with
integrated wire feed units for use with single phase 230V supply.
Technical Information
Model
XTE 171C
XTE 181C
XTE 201C
Input Power/Frequency
Single phase 230V 50Hz
Rated Input Capacity
6.45KVA
7.35KVA
8.75KVA
Max Current Draw
28A
32A
38A
Minimium Fuse Rating
16A
16A
32A
Output Current Step
8
8
8
Output Current Range
30A~165A
35A~185A
40A~205A
Duty Cycle
15%@165A
30%@115A
60%@80A
15%@185A
30%@130A
60%@90A
15%@205A
30%@145A
60%@100A
Protection Class
IP21S
IP21S
IP21S
Cooling Method
Fan Cooling
Fan Cooling
Fan Cooling