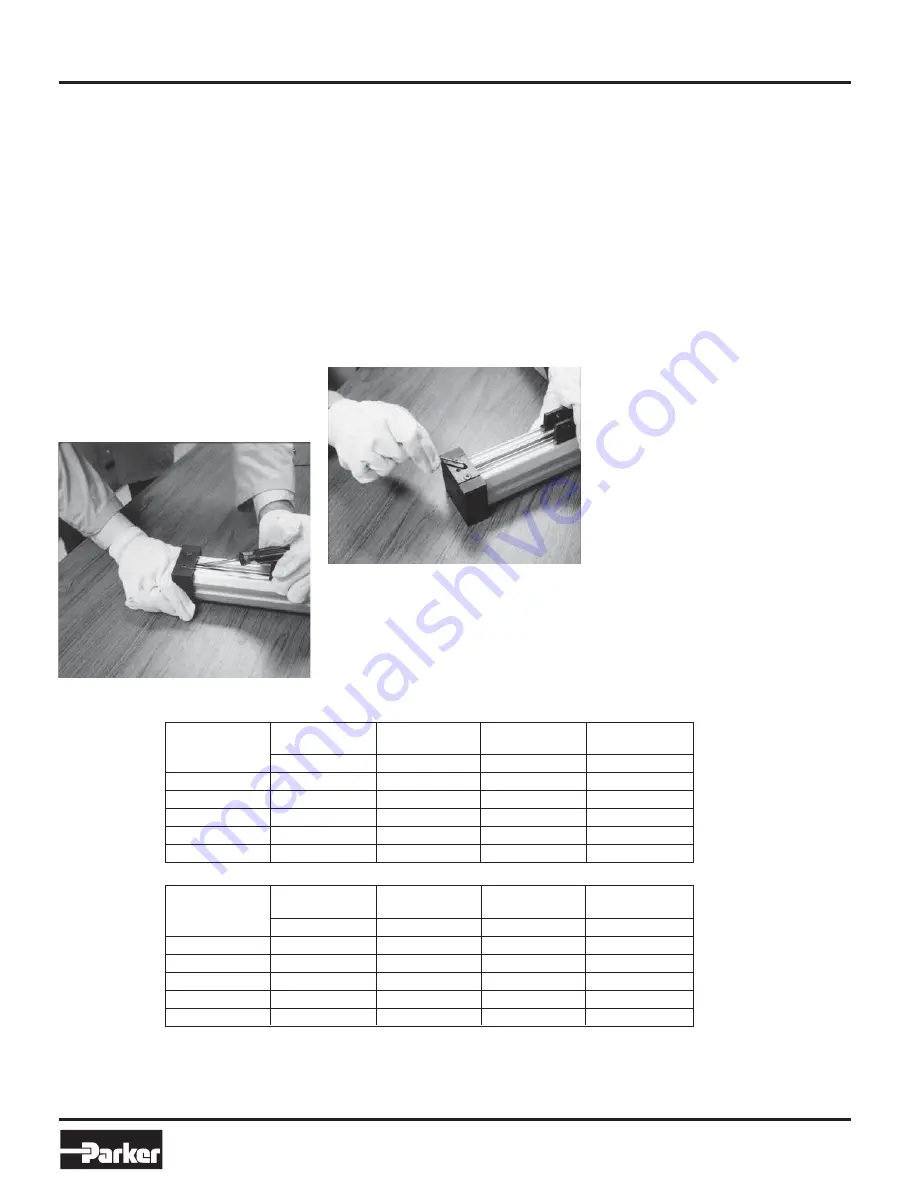
Parker Hannifin Corporation
Actuator Division
Wadsworth, Ohio USA
62
Catalog AU03-0900P-2/NA
Maintenance Instructions
Maintenance Instructions and Service
RC Series
7)
Test cylinder for audible leakage.
8)
Install outer band through the piston
carriage and into each end cap above the
band spacer. Position the band so no band
material protrudes from the face of either
end cap.
9)
Place carriage on piston.
10) Install carriage bolts and tighten on
each end of carriage.
11) Install carriage support rods (sym.
#13 if applicable) or carriage spacer #13A
(25mm bore).
12) Install band wipers with button head
screws. (On 25mm and 32mm bores with
double carriage mounting, install thinner 2
band wipers on inner ends of carriages.)
13) Install outer band set screws into band
clamp at each end and tighten to the rec-
ommended torque value
(Table C).
2)
Install the band clamp (sym. #22) on
each end cap with the flat head fasteners
(sym. #15). Tighten fasteners to the recom-
mended torque value
(see table C).
3)
If the outer band set screws (sym. #6)
have not already been removed, remove
them now.
4)
Insert the band clamp spacers (sym.
#16) into each end cap with the set screws
(sym. #8) pre-installed and with the hex
side of the set screws facing up.
5)
Insert a hex wrench through the outer
band set screw holes
(Photo #11) to
access the set screws in the band spacer.
6)
Tighten the inner band set screws at
each end to the recommended torque
value
(Table C).
Photo #11
3)
Repeat the preceding two steps to
install the opposite end cap.
4)
Place the cylinder assembly on a flat
surface so the end caps are aligned.
5)
Insert the end cap mounting screws
(sym. #9) at both ends and tighten to the
recommended torque value
(see Table C).
C) Final Assembly
1)
Using a thin flat blade screwdriver,
remove the slack of the inner band by
pushing the slot at each end
(Photo #10).
NOTE: The goal is not to tension the band,
merely to eliminate any slack. Use of
excessive force may cause the band to
move out of position and/or band
damage.
Photo #10
End Cap
Band Clamp
Inner Band
Outer Band
Bore
Screws
Screws
Screws
Screws
Size
Sym. #9
Sym. #15
Sym. #8
Sym. #6
25mm
35 + 5
10 + 2
10 + 5
10 + 5
32mm
35 + 5
10 + 5
10 + 5
10 + 5
40mm
60 + 10
15 + 5
10 + 5
10 + 5
50mm
40 + 10
15 + 5
10 + 5
10 + 5
63mm
70 + 10
15 + 5
10 + 5
10 + 5
RC Series Rodless Cylinder Torque Values (Kg cm)
End Cap
Band Clamp
Inner Band
Outer Band
Bore
Screws
Screws
Screws
Screws
Size
Sym. #9
Sym. #15
Sym. #8
Sym. #6
25mm
40 + 6
12 + 2
12 + 6
12 + 6
32mm
40 + 6
12 + 6
12 + 6
12 + 6
40mm
69 + 12
17 + 6
12 + 6
12 + 6
50mm
46 + 12
17 + 6
12 + 6
12 + 6
63mm
81 + 12
17 + 6
12 + 6
12 + 6
Table C
RC Series Rodless Cylinder Torque Values (inch - pounds)
Note: Rodless cylinder
fasteners should be
properly torqued using a
calibrated torque
wrench. Torquing of the
end cap fasteners
should be performed
first using the opposite
corner sequencing
technique to approxi-
mately 75% of the final
torque value shown in
the table to the left.
Then, continuing the
opposite corner
technique, torque to
the final value.