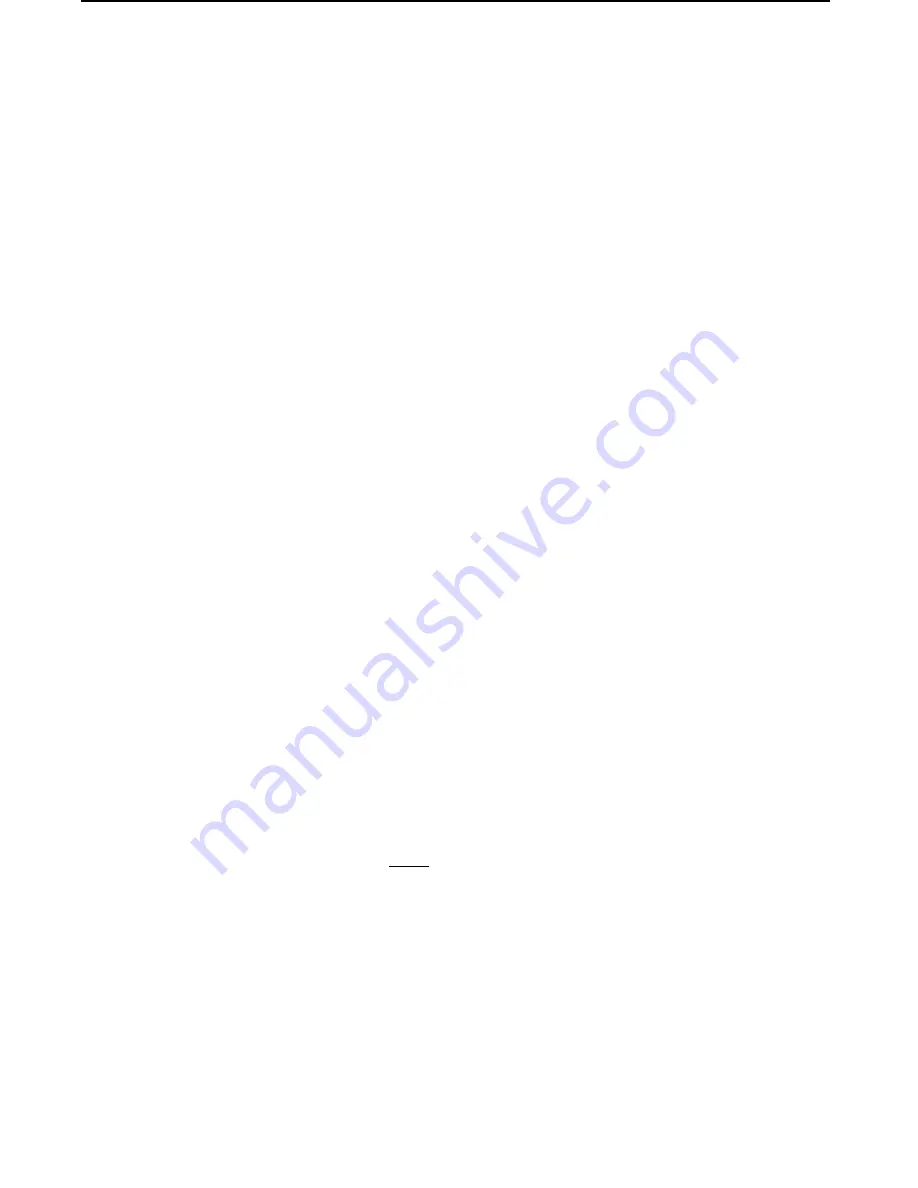
The user may define a move profile using the MC command to establish the continuous
mode. Velocity can be programmed on the fly by the V command.
The positioner also has a mode MQ, which is like the preset move mode in that the move
distance is pre-defined, but it is possible to change speed in the middle of the move as
required based on a distance, input or time delay trigger.
Encoder Following
The commands SIM and CCS may be used to allow the motor of one axis to follow the
encoder of another axis or an externally-generated step and direction signal. When the
control module is to be used in following mode, the input from the encoder to be followed
should be connected to the External Encoder connector pins 1 - 9 (as shown in Figure 2-2).
These inputs can be configured using the CCS command as an encoder input (x1, x2 or x4).
The SIM command may be used to select:
a) Normal indexer operation (SIM0), used for reverting to normal operation by overiding
previous SIM commands
b) Encoder following with indexer motion commands inoperative (SIM1).
c) Encoder following with indexer commands operative (SIM 2), allowing the superimposing
of indexer moves.
d) Software scaled encoder following (SIM3).
e) Software scaled encoder following with direction reversal (SIM4).
f) Preset following index mode (SIM 5).
For SIM1 and SIM2 operation the motor output rate follows the encoder input, using
hardware scaling, at a ratio of 1 or less.
Software Scaling
This is the scaling of the encoder input when using the SIM3 or SIM4 commands to achieve
following at a ratio greater or less than 1. Unlike hardware scaling, exact following ratios can
be achieved by controlling both the numerator and denominator parts of the fraction used to
set the scaling ratio, thus ratios such as 3:1 can be obtained.
The scaling ratio is set using the CMR command value divided by the CUR command value
to give :
Motor Output Rate = input rate x
CMR
CUR
Both CMR values and CUR values are individually limited to a range of 1 to 32,767, and
when combined as a fraction are further limited, by software scaling to having both numerator
and denominator in the range 1 to 255. This results in a maximum division ratio of 1/255, or
at the other extreme a maximum multiplication ratio of 255.
Software scaling does not allow the superimposing of indexer moves.
Artisan Technology Group - Quality Instrumentation ... Guaranteed | (888) 88-SOURCE | www.artisantg.com
Содержание PDHX-E Series
Страница 3: ...Artisan Technology Group Quality Instrumentation Guaranteed 888 88 SOURCE www artisantg com...
Страница 15: ...Artisan Technology Group Quality Instrumentation Guaranteed 888 88 SOURCE www artisantg com...
Страница 68: ...Artisan Technology Group Quality Instrumentation Guaranteed 888 88 SOURCE www artisantg com...
Страница 92: ...Artisan Technology Group Quality Instrumentation Guaranteed 888 88 SOURCE www artisantg com...
Страница 98: ...Artisan Technology Group Quality Instrumentation Guaranteed 888 88 SOURCE www artisantg com...
Страница 101: ...Artisan Technology Group Quality Instrumentation Guaranteed 888 88 SOURCE www artisantg com...