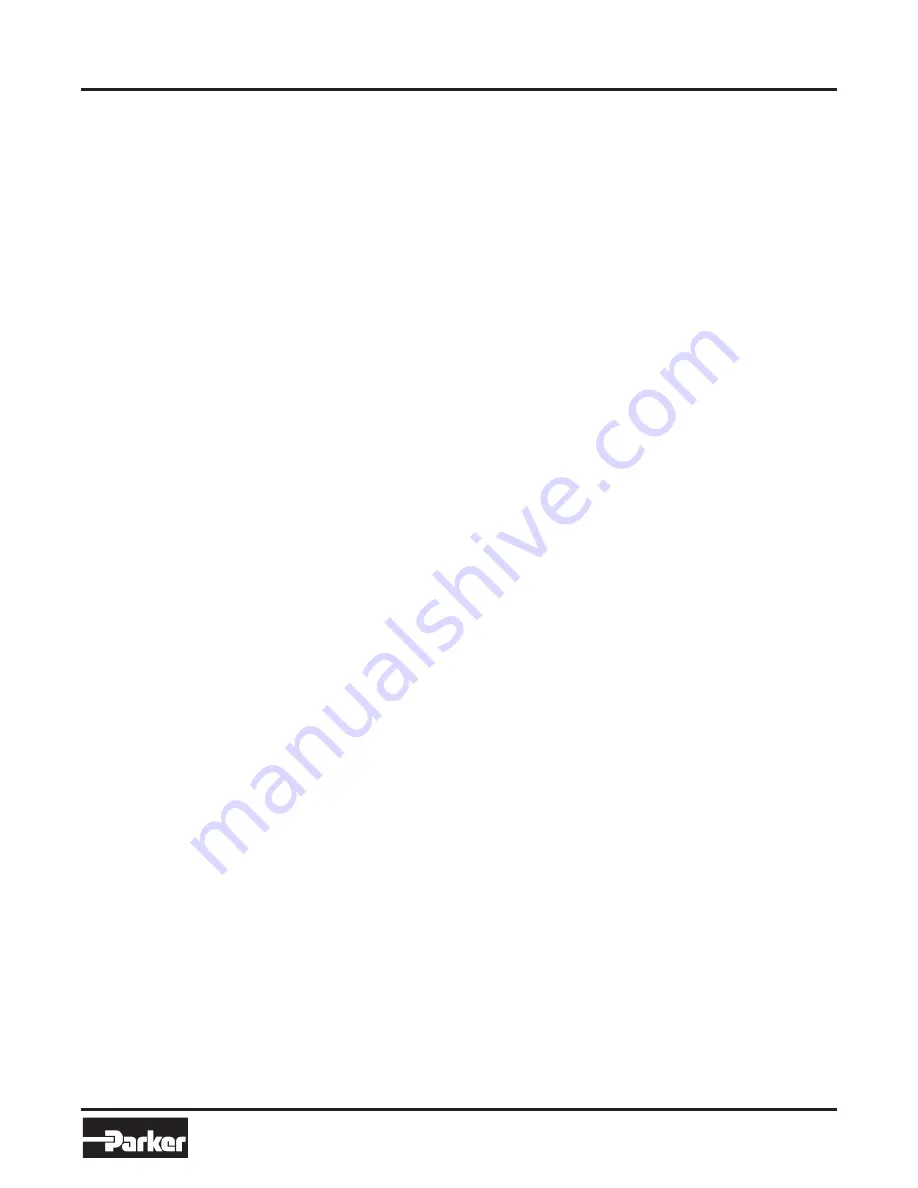
Bulletin HY13-1650-M1/USA
Piston Pump Service Procedure
P2 / P3 Series
Parker Hannifin Corporation
Hydraulic Pump/Motor Division
Greeneville, Tennessee US
7
NOTE: Before troubleshooting any system problem, check service literature published by the equipment and/or
component manufacturers. Follow their instructions, if given, for checking any component other than the Pump unit.
Preparation
Make your troubleshooting easier by preparing as
follows:
• work in a clean, well-lighted place;
• have proper tools and materials nearby;
• have an adequate supply of clean petroleum-based
solvent.
WARNING: SINCE SOLVENTS ARE FLAMMABLE, BE
EXTREMELY CAREFUL WHEN USING ANY SOL-
VENT, EVEN A SMALL EXPLOSION OR FIRE COULD
CAUSE INJURY OR DEATH.
WARNING: WEAR EYE PROTECTION AND BE SURE
TO COMPLY WITH OSHA AND OTHER MAXIMUM AIR
PRESSURE REQUIREMENTS.
Preliminary Checks
Hydraulic systems are often trouble-free. Hence, the
problem an operator complains of could be cause by
something other than the hydraulic components.
Thus, once you have determined that a problem exists,
start with the easy-to-check items, such as:
• parts damaged from impact that were not properly
repaired, or that should have been replaced; and
• improper replacement parts used in previous
servicing
• mechanical linkage problems such as binding,
broken, or loose parts or slipping belts
Hydraulic Components
If you think the problem is caused by a hydraulic
component, start by checking the easy-to-reach items.
Check all hoses and lines for cracks, hardening, or
other signs of wear. Reroute any usable hoses that are
kinked, severely bent, or that rest against hot engine
parts. Look for leaks, especially at couplings and
fittings. Replace any hoses or lines that don’t meet
system flow and pressure ratings.
Next, go to the reservoir and filter or filters. Check fluid
level and look for air bubbles. Check the filter(s).
20/18/14 filtration is recommended per ISO 4406.
Visually check other components to see if they are
loosely mounted, show signs of leaks, or other damage
or wear.
Excessive heat in a hydraulic system can create
problems that can easily be overlooked. Every system
has its limitation for the maximum amount of tempera-
ture. After the temperature is attained and passed, the
following can occur:
• oil seal leaks
• loss of efficiency
• pump loss of efficiency
• pump failure
• hoses become hard and brittle
• hose failure
A normal temperature range means an efficient hydrau-
lic system. Consult the manuals published by equip-
ment and/or component manufacturers for maximum
allowable temperature and hydraulic tests that may be
necessary to run on the performance of the hydraulic
components. The pump is not recommended for hydrau-
lic systems with maximum temperatures above 70°C
(158°F).
Normal working temperatures are 0° - 70°C (-32° -
158°F).
Maximum case drain temperature is 90°C (194°F).
Troubleshooting Guide