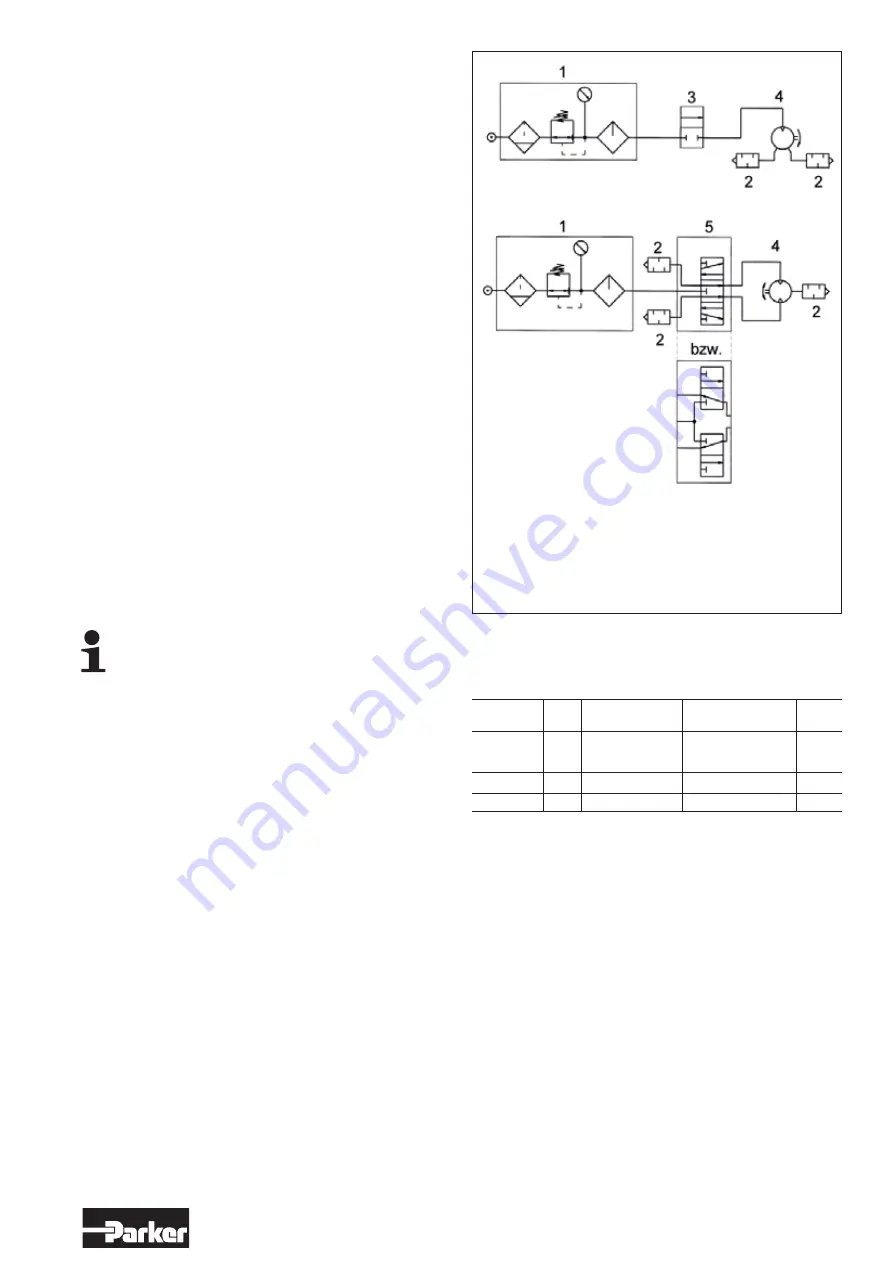
5
www.parker.com/euro_pneumatic
5.6 Dimensions
5.7 Installation
Prior to Connection of Motor
Before connecting the air supply line to the motor, clean
the air pipe and the air hose by slightly blowing air into
the pipe/hose. This will remove any dirt particles that are
present in the pipe/hose.
Always wear safety goggles, tightly hold the pipe/
hose and do not move into the air stream.
Remove the covers from the connections.
Turn the air-supply to “OFF”.
Air Supply Line
Make sure, that all air lines have a sufficient cross-section
(see chapter Technical Data) and that there are no throttle
areas, bends or kinks. If the air supply line is longer than
2 meters, the next larger hose I.D. should be installed in
order to avoid a loss of power.
Connection of Motor
For operation in only one turn-direction:
See Diagram, figure a)
Install silencers (optional equipment) into the unused ports.
For reversible operation
(clockwise and anticlockwise direction):
See Diagram, figure b)
Connect 2 supply lines to the motor. For position and size
of the air inlet ports, see Dimensional Drawing
(chapter 5.6).
Do not close unused ports with a plug or the like. This may
lead to a loss of the motor’s power or motor standstill. The
exhaust air may be piped away using either an exhaust line
or a silencer as well.
Do not use any Teflon tape on the threads of the pipe.
Operating Pressure
Check and make sure that the flow-pressure at the motor
connection side is 6 bar (85 PSI). A higher air pressure
leads to increased wear and tear (install a pressure
regulator). An air pressure below 6 bar reduces the power
output of the motor.
Lubrication
All motors may be operated either with or without
lubricated air. The best performance is achieved by adding
1 – 2 drops of oil per 1 m³ of air consumption. When
operating with oil-free air, a performance reduction of up
to 20 % occurs.
The air supply to the motor has to be filtered
(see chapter 5.8).
The maintenance unit, the valves and the silencers have
to be selected according to the air consumption of the
motor, not in accordance to the connection threads. Install
components, which have a measurement that will limit the
pressure drop – when measured from the maintenance
unit to the motor – to less than 0.5 bar (7.25 PSI).
Install a maintenance unit, fill it with oil and adjust oiler as
needed. Fill the oil container of the oiler to the indicated oil
level.
Lubricants
Use only lubricants approved by the manufacturer.
Please refer to the technical catalog PDE2539TC
1. Maintenance unit (filter with water separator, pressure regulator
and oiler)
2. Silencer
3. 2/2-way-valve
4. Motor
5. 5/3-way-valve or alternatively 2 x 3/2-way-valve
Illustration 2 - Diagram
5.8 Air Quality
With regard to air quality according to ISO 8573-1 we recommend:
Class
Residual Dust
Residual Water
Residual
Oil
particle max.
max. pressure content
size um concentrati concentrati dew-point mg/m
3
on mg/m
3
on mg/m
3
°C
Lubricator air
-/4/4
25
10
5
+3
5
Oil-free air
6/3/3
5
5
1
-20
1
* Filter grade 8 µm is sufficient for units machines that are operated in
dry run.
a)
b)