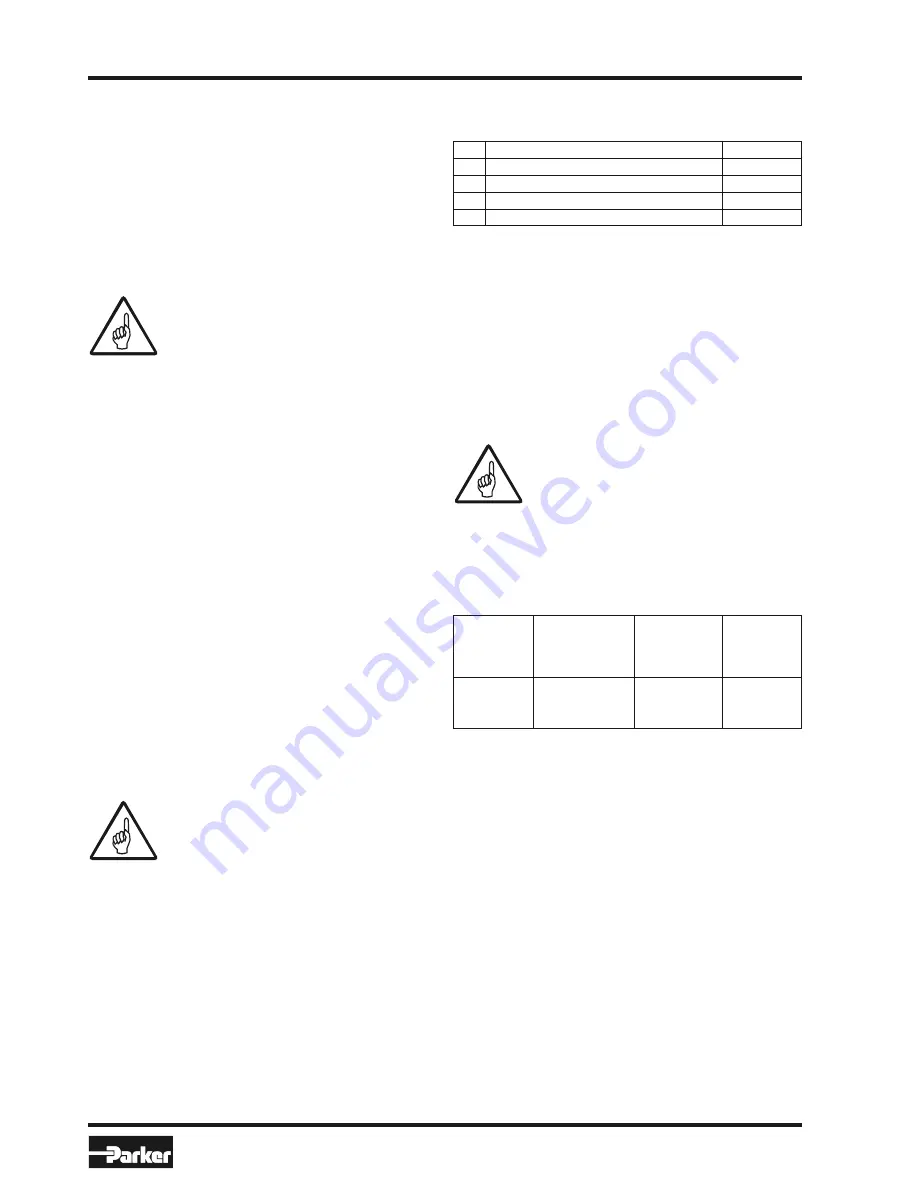
30
IA VRD UK.INDD RH 02.06
Digital Power Amplifier
Series VRD350 and VRD355
Installation Manual
Parker Hannifin GmbH & Co. KG
Hydraulic Controls Division
The controller structure is shown in the figure on
page 17. Pressure control loops and their dynamics
are essentially determined by the system capaci-
ties. A presetting in the works is impossible. The
parameters should be determined individually for
each application. Controller parameters can be
calculated from the loop amplifications using the
equations on page 22. Should these calculations
prove impossible, the parameter values have to be
determined in tests.
Proportional pressure valves can oscillate on ac-
count of the system. This behaviour may be signifi-
cant in the control loop, particularly through system
feedbacks. In certain circumstances, this may be
counteracted by adjusting the dither parameter (P5,
P6). Variations to the dither frequency are generally
the most effective.
Remote Loop Control
Initially, the amplifier is in open loop operating
mode. The solenoid current is in direct proportion
to the command signal, resulting e.g. in a certain
pressure using pressure control valves. By chang-
ing the “reset ramp” input to high, e.g. by using an
external PLC, the amplifier is armed to function as
a loop controller.
The comparator monitors the actual value signal.
In the case of pressure controls, mainly using
switching controllers, P21 is preferably used. If the
actual value now exceeds this comparative value,
the control switches on.
Even if the actual value is under the switching
threshold, the control remains active. The signal
at the „Ramp reset“ input is required to switch off
the control. The control remains active until „Reset
ramp“ returns to 0V.
The output of the integral part (P17)
starts at the same time with the value
0. This is why negative oscillations may
occur due to the system.
The remote loop control is activated with E2 = 2.
Then P21 and P22 have the following meanings:
Display
P21
Positive threshold
0.00...9.99V
activates controller
P22 Negative threshold
0.00...9.99V
activates controller
If E2 = 2 and P21 and P22 = 0, the control can be
directly activated with the “Reset ramp“ input. This
permits a selective external activation and deactiva-
tion of the control.
If E2 = 2, actual value U11 is used directly as a com-
parative value. This is different from the “Standard
comparator function”, where the control difference
U12 is decisive.
The Effects of the Time Delay P23 and P24:
P23 with remote loop controller must
always be set = 0.00. Other values give
no function.
P24 for a delay when switching in the
control with a switching controller. The control is
switched on after a time delay of the preset time.
Input
Reset
Ramp
Ratio of
actual value/
switching
threshold
Control loop
LED
RESET
RAMP
0
smaller 1
ooen
off
1
smaller 1
open
on
1
larger 1
closed
flashing
Avoid instability of the control loop dur-
ing the experimentation. This may cause
damage to the drive or machine.
The status is displayed with the LED “Reset
Ramp“.