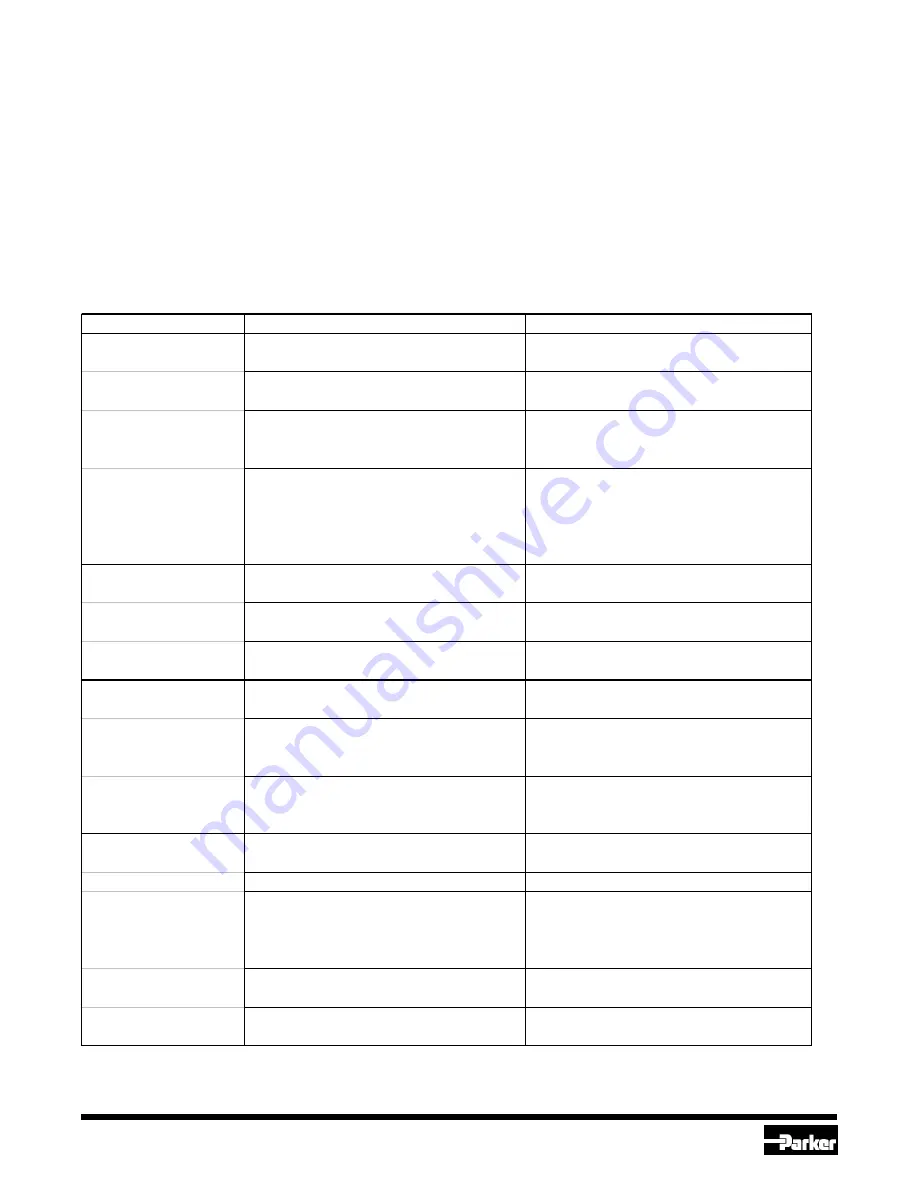
5
Refrigerating Specialties Division
valves isolating such sections should be marked,
warning against accidental closing, and must not be
closed until the liquid is removed. Check valves
must never be installed upstream of solenoid valves,
or regulators with electric shut-off, nor should hand
valves upstream of solenoid valves or downstream of
check valves be closed until the liquid has been
removed. It is advisable to properly install relief
devices in any section where liquid expansion could
take place.
Avoid all piping or control arrangements which might
produce thermal or pressure shock.
For the protection of people and products, all refriger-
ant must be removed from the section to be worked
on before a valve, strainer, or other device is opened
or removed.
Flanges with ODS connections are not suitable for
ammonia service.
SYMPTOM
PROBABLE REASON
CORRECTION
Regulator does not
shut off flow
Diaphragm or seat dirty, damaged or
frozen
Clean or replace. Clean strainer
Diaphragm follower stuck or damaged
Clean or replace. Install follower
carefully
Piston jammed with excess dirt
Remove and polish piston and bore
with crocus cloth. Clean valve and
strainer
Modulating plug leaking due to excess
dirt or damaged
Clean or replace. If used on liquid,
check for erosion due to excessive
flash gas by subcooling or by reducing
pressure drop across valve by providing
restriction at valve outlet.
Regulator does not
open
Pressure Regulator Diaphragm
ruptured or badly deformed
Replace. Make sure 2 diaphragms are
installed.
Diaphragm follower stuck, damaged or
frozen
Clean or replace. Install follower
carefully
Piston worn, too much clearance
Replace piston. Check for reason. If
used or liquid, check for flash gas.
Regulator Operation
erratic
Diaphragm or seat dirty, damaged.
Clean or replace. Clean strainer
Diaphragm follower has dirt on the
outside diameter or outside diameter is
damaged.
Clean or replace
Regulator too far oversized.
Check load. Replace with smaller
regulator or investigate use of Reduced
Capacity Plug Kit.
Pressure drop across
regulator too high
Inlet or outlet restricted
Check for restriction. Clean strainer.
Regulator too small
Replace with proper size regulator
Large amount of flash gas in liquid line Reduce flash gas by subcooling.
Reduce line restriction by increasing
line size, particularly at the regulator
outlet. Replace with larger regulator.
High pressure drop causes high rate of
expansion of gas at regulator outlet
Increase pipe size at the outlet of the
regulator
Regulator does not open all the way.
Check piston for wear. Replace, if
needed.