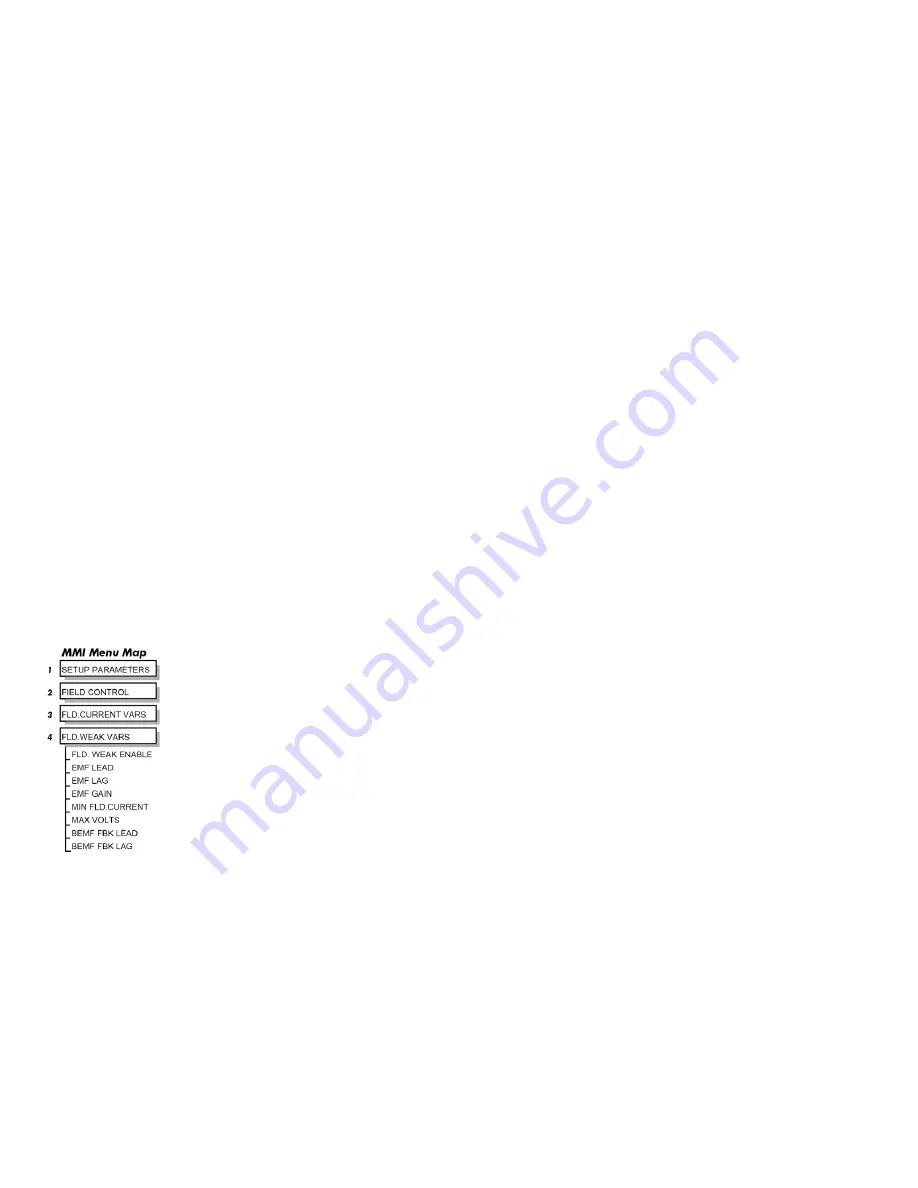
5-6
Control Loops
DC590+ Series DC Digital Drive
Current Control
The field current loop can accept a demand directly from the plant and/or an outside field weakening loop and forms the error signal which is the
difference between demand and feedback. The error signal is fed into a P + I compensator which produces the output of the field loop, i.e. the field
firing angle signal.
The firing angle signal is translated into a certain time delay from the mains zero cross point (obtained via the same Phase-Lock-Loop as for the
armature) and this results into a firing command being issued to the field bridge every 1/2 of a mains cycle in steady-state.
Voltage Control
This offers the facility of an open-loop voltage control for motors which do not provide in the nameplate the field current rating. The field voltage is
controlled by the specified FLD. VOLTS RATIO which defaults to 90.0%. This is the maximum dc Volts that can be obtained for a given ac RMS
input in a single-phase rectifier, i.e. 370V dc for 415V ac supply. The specified ratio determines directly the firing angle at which the controller
operates and therefore the thermal effects on the field resistance as well as mains voltage variations are not compensated for. It is also worth noting
that in this mode the field overcurrent alarm is not active (since there is no current scaling) and therefore this mode is not recommended for use with
supplies much greater than the field voltage rating.
Field Weakening
Motor field weakening is used to extend the speed region of the motor above its base speed (the motor speed resulting at rated armature voltage, rated
armature current and rated field current), in a constant power mode of operation (motor torque reducing with increasing speed).
Note that the motor should be rated for field-weakened operation, in terms of rotational speed and reduced field current, before utilising this mode.
The drive includes a field weakening loop that, above base speed, can control the field current demand to the correct level required to maintain motor
back-EMF at a pre-defined level.
NOTE
Field weakening is not possible when running with Armature Volts feedback. Although field weakening can be “Enabled” in this
instance, a software interlock clamps the field demand at 100% and will not allow the field weakening to reduce it.
When the back-EMF measurement is higher than the MAX VOLTS setting (default 100%) the excess voltage is presented to the field weakening gain-
limited PI controller as an error, and this controller reduces the field current demand accordingly.
The gain-limited controller is tuned as follows:
1.
Ensure that the armature current, speed and field current loops are correctly tuned.
2.
Enable field weakening control (FLD. WEAK ENABLE = ENABLE), with analogue tachogenerator, encoder or microtach speed feedback,
correctly installed and configured for extended speed operation.
3.
Run the drive and slowly increase the speed demand so that the field is being weakened by the gain-limited PI controller. Change the MAX
VOLTS parameter down and up by 10% to generate field current transients.
4.
Alternately increase the P gain (using the dc-gain parameter EMF GAIN) and reduce the integral time-constant (parameter EMF LEAD) until
the loop is correctly tuned (see the Current Loop "Tuning Hints" above).
Содержание 590+ series
Страница 2: ......
Страница 14: ...Cont 12...
Страница 16: ...DC590 Series DC Digital Drive...
Страница 20: ......
Страница 32: ...2 12 Product Overview DC590 Series DC Digital Drive...
Страница 34: ......
Страница 110: ...3 76 Installing the Drive DC590 Series DC Digital Drive Figure 3 29 Frame 2 40A 165A Stack Assembly...
Страница 111: ...Installing the Drive 3 77 DC590 Series DC Digital Drive Figure 3 30 Frame 3 180A Stack Assembly Drg No HG466427...
Страница 112: ...3 78 Installing the Drive DC590 Series DC Digital Drive Figure 3 31 Frame 3 270A Stack Assembly Drg No HG466428...
Страница 113: ...Installing the Drive 3 79 DC590 Series DC Digital Drive Figure 3 32 Frame 4 380 830A Stack Assembly Drg No HG466700U001...
Страница 130: ...3 96 Installing the Drive DC590 Series DC Digital Drive...
Страница 132: ......
Страница 164: ...4 32 Operating the Drive DC590 Series DC Digital Drive...
Страница 166: ......
Страница 174: ...5 8 Control Loops DC590 Series DC Digital Drive...
Страница 176: ......
Страница 202: ......
Страница 222: ...7 20 Trips and Fault Finding DC590 Series DC Digital Drive...
Страница 224: ......
Страница 242: ......
Страница 272: ...DC590 Series DC Digital Drive...
Страница 288: ...B 16 Certification DC590 Series DC Digital Drive...
Страница 290: ......
Страница 342: ...C 52 Parameter Specification Tables DC590 Series DC Digital Drive...
Страница 344: ......
Страница 365: ...Programming D 21 DC590 Series DC Digital Drive Functional Description...
Страница 494: ...D 150 Programming DC590 Series DC Digital Drive Programming Block Diagram Sheet 1...
Страница 495: ...Programming D 151 DC590 Series DC Digital Drive Programming Block Diagram Sheet 2...
Страница 496: ...D 152 Programming DC590 Series DC Digital Drive Programming Block Diagram Sheet 3...
Страница 497: ...Programming D 153 DC590 Series DC Digital Drive Programming Block Diagram Sheet 4...
Страница 502: ...D 158 Programming DC590 Series DC Digital Drive...
Страница 504: ......
Страница 506: ...E 2 Technical Specifications DC590 Series DC Digital Drive...
Страница 507: ...Technical Specifications E 3 DC590 Series DC Digital Drive...