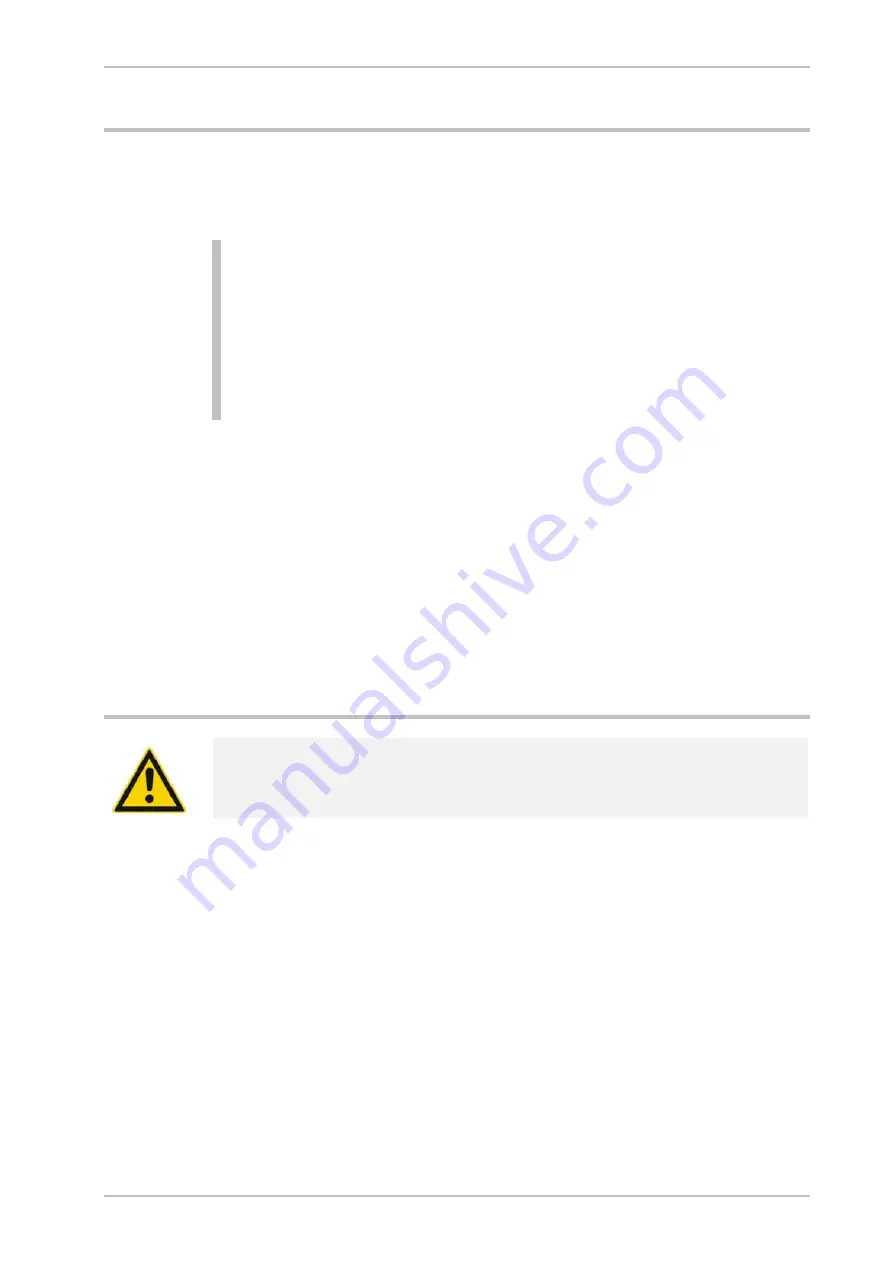
WVM_BASIS_EN_03—07/2016
13
Intended use of the dryer
The dryer is exclusively intended for drying compressed air. Depending on
defined input conditions, it dries compressed air for industrial use.
The dryer is designed for compressed air, which is free from aggressive water,
oil, and solid matter constituents.
Note:
Never operate the dryer without upstream filter. For this reason, the
operator must install an appropriate upstream filter (degree of
filtration < 0.01 µm, residual oil contents < 0.001 mg/m³).
We recommend that you install an additional downstream filter to
protect the downstream compressed air network against desiccant
residues.
Suitable filter solutions can be obtained from the manufacturer.
As standard, the dryer is intended to be sited within a building and protected
against the weather. When it is sited in the open air (option), the instructions on
page22 must be complied with.
The dryer may be operated only in accordance with the data on the type plate
and in accordance with the contractual conditions.
Suspected misuse
The dryer must not be misused as a climbing aid! Pipes, valves, and similar
fittings have not been designed for such loads. They could fracture, tear off, or
become damaged in another way.
General safety notes
For your own safety, when carrying out any work on the dryer comply with
all applicable national safety regulations!
Personnel qualification
Only authorized and qualified specialist personnel may be tasked with the work
on the dryer described in these operating instructions. The electropneumatic
switch cabinet in particular must be opened and serviced by an instructed trained
electrician only.
Conversions and modifications
Without prior approval by the manufacturer, no conversions and modifications
must be made to the dryer! Any non-approved modifications may restrict the
operational safety of the dryer and cause damage to property or personal injury.