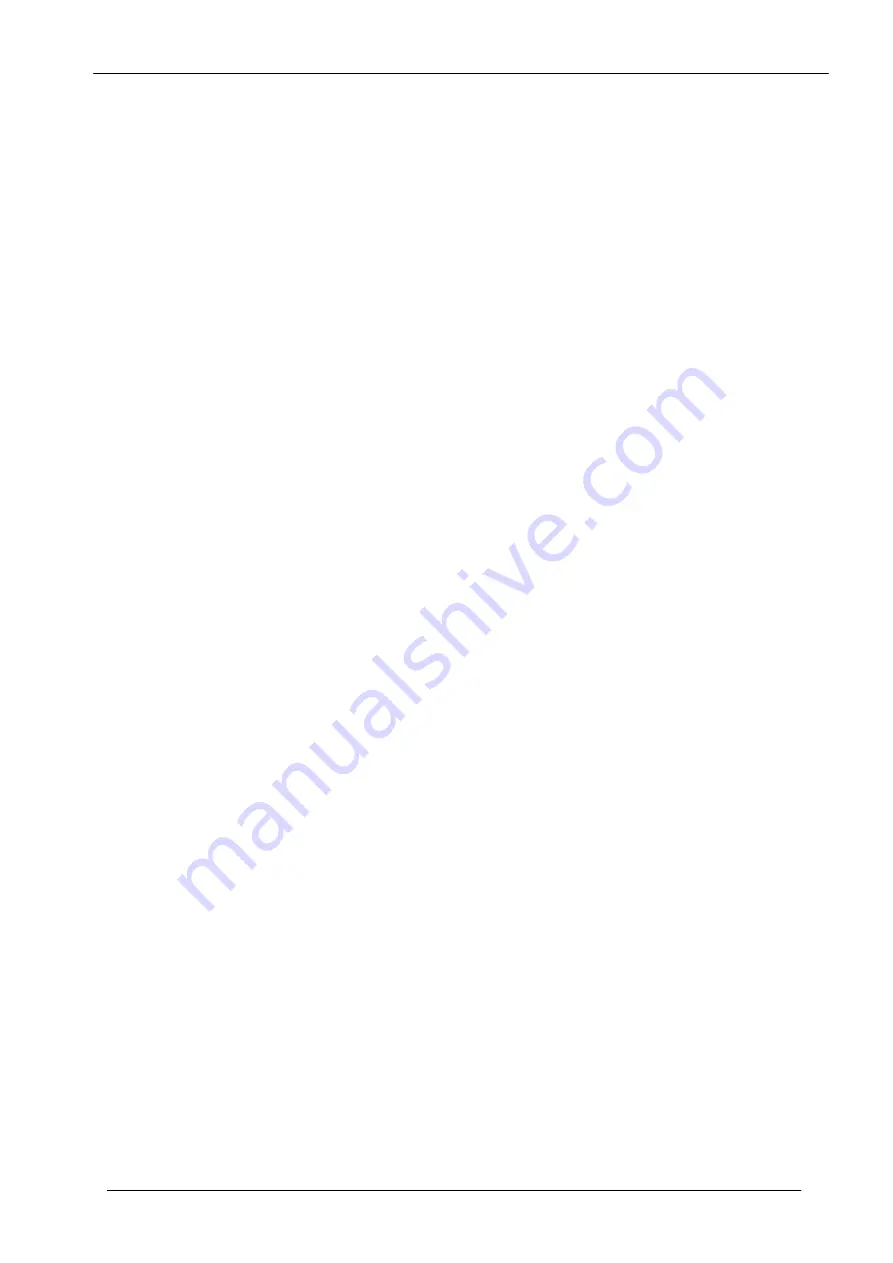
Technical Manual
P&B Engineering
ISSUE 7 28/9/99
Page
1
1. Introduction
The Goldstart Motor Protection Controller is a highly sophisticated microprocessor based motor
protection and control unit, specifically designed to be used on motors with full load currents upto 2000 Amps, at any
voltage and as an integral part of any type or manufacture of Motor Control Centre. All of the latest features are
included in the to allow total control, protection and monitoring of motor starters either by direct hard
wire inputs or via the RS485 serial port.
The can be used to control Direct on Line, Star-Delta, Reversing and Two Speed motor starters and by
the use of RMS current sampling, enables the to be used in conjunction with A.C. Variable speed drives
or Soft Starters, without any affect on the protection performance . The control of circuit breakers can also be
accomplished using the .
The monitors current, voltage and temperature inputs to provide the most comprehensive motor
protection package ever produced by P & B Engineering. This combined with all the necessary control and
monitoring functions and a high speed communications facility all within a small easily installed package at a cost
which is less than previously charged for a sophisticated microprocessor motor protection relay, make the
the most attractive Motor Protection and Control device available today.
All hard wired control inputs are connected to, the via optically isolated inputs to enable all starting,
stopping and tripping commands to be carried out by the . Status of all individual hard wired contacts is
also provided both locally via the liquid crystal display and remotely via the RS485 communications port.
All setting parameters are programmed independently for each unit via the integral keypad and liquid
crystal display on the front plate or via the RS485 communications port and the IBM PC based MPCSET software
package available with the .
During operational conditions the LCD also gives access to accurate running, statistical and fault data such as; Phase
Volts, Phase Amps, thermal capacity, Time to Trip, Phase unbalance, Motor hours run, number of starts and many
more.
Light Emitting Diodes mounted on the front plate give visual indication of the motor status such as Motor Running,
Motor Stopped, Alarm or Trip conditions etc.
Flexible high speed control via PLC or DCS systems is obtained through the 's RS485 communications
port, allowing computer access to full control and monitoring of motor data, including : running data, motor statistical
data and control input status.
All protective functions can be individually configured to enable or disable tripping and alarm functions,
enabling protection to be simplified for the very lowest motor ratings. In addition each protective function can be set
to allow self or manual reset after alarm or trip and manual reset can be set to allow resets after an alarm or trip to be
made locally, remotely or by authorised personnel only.
A unique '
Protection Only
' mode enables the to be installed for protection only purposes, this requires
only conventional current transformer and trip output wiring, enabling simple installation into existing equipment with
minimum wiring modifications. This allows users to take full advantage of the enhanced protective capability and the
RS485 communication facilities provided by the .
Содержание MPC2000+
Страница 4: ......