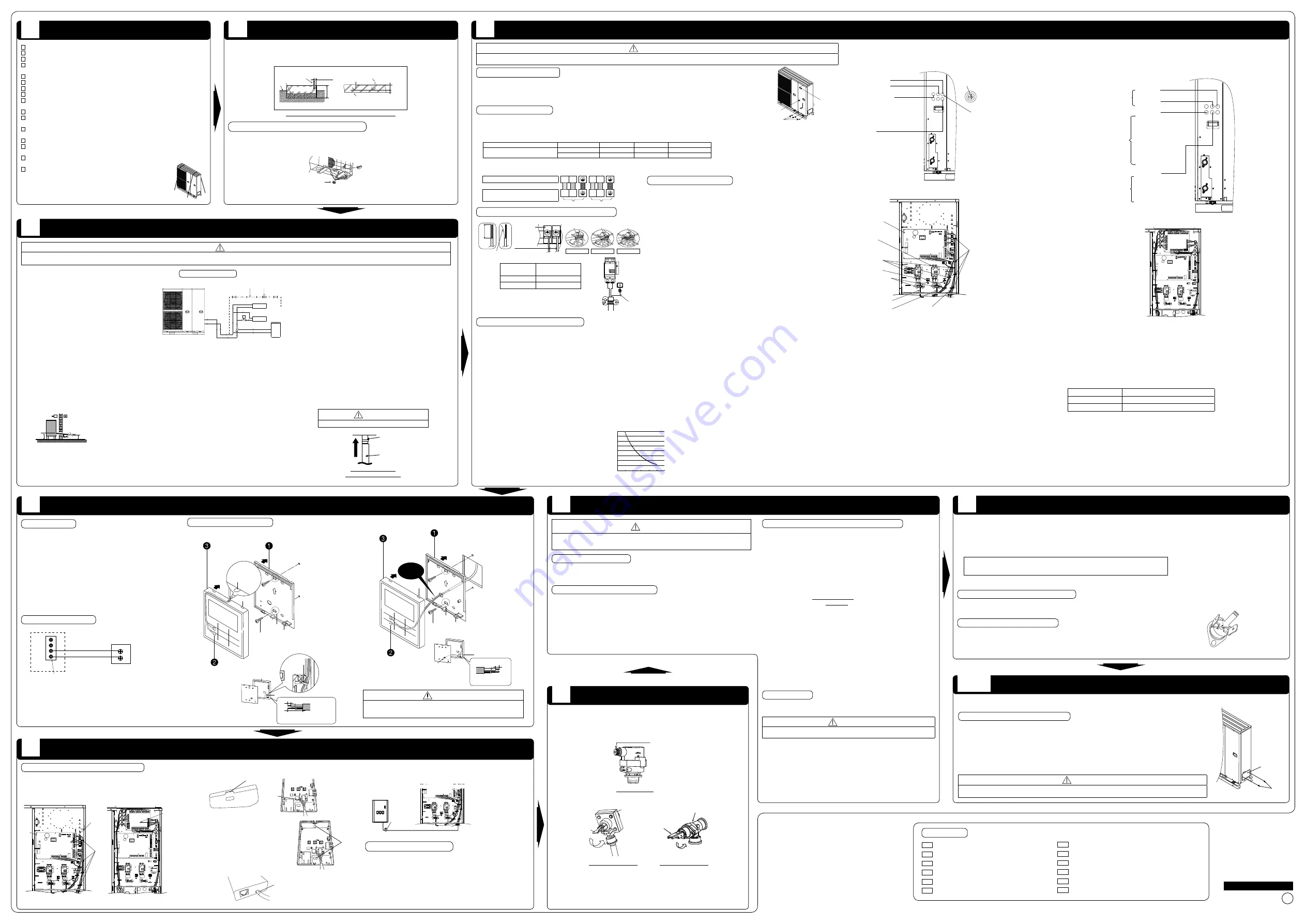
TEST RUN
1. Before test run, make sure below items have been checked:-
a) Pipework are properly done.
b) Electric cable connecting work are properly done.
c) Mono bloc unit is fi lled up with water and trapped air is released.
2. Antifreeze agent must be added into water circuit to prevent freezing of water when outdoor ambient temperatures is low. Recommended antifreeze:
Propylene glycol: 40% (equivalent to -20°C)
3. Set ON to the Mono bloc unit and RCCB
2
. Then, for remote control operation please refers to (Mono bloc) Air-to-Water Heatpump’s operation instruction.
Note:
•
During winter, turn on the power supply and standby the unit for at least 15 minutes before test run.
Allow suffi cient time to warm up refrigerant and prevent wrong error code judgement.
4. For normal operation, Water Pressure Gauge
4
reading should be in between 0.05 MPa and 0.3 MPa.
5. After test run, please clean the Magnetic Water Filter Set
c
. Reinstall it after fi nish cleaning.
CHECK WATER FLOW OF WATER CIRCUIT
Confi rm the maximum water fl ow during main pump operation not less than 15 l/min.
*Water fl ow can be check through service setup (Pump Max Speed)
[Heating operation at low water temperature with lower water fl ow may trigger “H75” during defrost process.]
RESET OVERLOAD PROTECTOR
0
Overload Protector
0
serves the safety purpose to prevent the water over heating. When the Overload Protector
0
trip
at high water temperature, take below steps to reset it.
1. Take out the cover.
2. Use a test pen to push the centre button gently in order to reset the Overload Protector
0
.
3. Fix the cover to the original fi xing condition.
TEST RUN
9
Use test pen to push this
button for reset Overload
Protector
0
.
Mono bloc unit will become heavy when fi lled with water. Please install the unit on a strong concrete fl oor and consider the
weight of the unit and water.
•
Fix Mono bloc unit on the concrete fl oor with M12 anchor bolt at 4 locations.
•
Pull-out strength of these anchor bolts must be above 15000N.
Grip anchor bolt
Embedded anchor bolt
Broken stone
Anchor bolt
60mm
or more
300mm
or more
Floor
Concrete
Anchor bolt
Floor slab (concrete)
Above
20mm
80mm
•
Compress strength of concrete is above 18MPa {180kgf/cm
2
}
Illustration of grip type and embedded type anchor bolt
DISPOSAL OF MONO BLOC UNIT DRAIN WATER
•
When a Drain elbow
1
is used, please ensure to follow below:
-
The unit should be placed on a stand which is taller than 50mm.
-
Cover the 8 holes (ø20mm) with Rubber cap
2
(refer to illustration below)
-
Use a tray (fi eld supply) when necessary to dispose the Mono bloc unit drain water.
Drain elbow
1
Rubber cap
2
x 8
•
If the unit is used in an area where temperature falls below 0°C for 2 or 3 consecutive days, it is recommended not to use
the Drain elbow
1
and Rubber cap
2
, for the drain water freezes and the fan will not rotate.
MONO BLOC UNIT INSTALLATION
2
PIPING INSTALLATION
3
WARNING
This section is for authorized and licensed electrician / water system installer only. Work behind the Cabinet Front Plate
f
secured by screws must only be carried out under supervision of qualifi ed contractor,
installation engineer or service person.
Temporary connection to be
removed immediately after filling
Servicing
Valve
Fan Coil Unit
2-Way Valve
Tank
Radiator /
Floor Heater
Servicing
Valve
Main Water
Supply
Double Check Valve assembly
is acceptable in house
Typical Piping Installation
Please engage a licensed water circuit installer to install this water circuit.
•
This water circuit must comply with relevant European and national regulations (including EN61770), and local building regulation codes.
•
Ensure the components installed in the water circuit could withstand water pressure during operation.
•
Do not apply excessive force to piping that may damage the pipes.
•
Use Rp 1¼" nut for both water inlet and water outlet connection and clean all piping with tap water before connecting to the Mono bloc unit.
•
Cover the pipe end to prevent dirt and dust when inserting it through a wall. If an existing tank is to be connected to this Mono bloc unit, ensure the pipes are clean before water pipe installation is carried out.
•
Choose proper sealer which can withstand the pressures and temperatures of the system.
•
Make sure to use two spanners to tighten the connection. Tighten the nuts with torque wrench: 117.6 N•m.
•
If non-brass metallic piping is used for installation, make sure to insulate the piping to prevent galvanic corrosion.
•
Do not use pipes that are crushed or deformed. If these inferior pipes are used, it may cause unit malfunction.
•
Make sure to insulate the water circuit piping (insulator thickness : 20mm or more) to prevent condensation during cooling operation and reduction of heating capacity, as well as avoid freezing of the outdoor
water circuit piping during winter season.
•
After installation, check the water leakage condition in connection area during test run.
•
In case of a power supply failure or pump operating failure, drain the system (as suggested in the fi gure below).
H
< H
When water is idle inside the system,
freezing up is very likely to happen
which could damage the system.
Drainage piping installation
•
Use a drain hose with inner diameter of 15 mm.
•
The hose must be installed in a continuously downward direction and left open to the frost-free atmosphere.
•
If drain hose is long, use a metal support fi xture along the way to eliminate the wavy pattern of drain tube.
•
Water will drip from this hose, therefore the outlet of this hose must be installed in an area where the outlet cannot become blocked.
•
Do not insert this hose into sewage or drain pipe that may generate ammonia gas, sulfuric gas, etc.
•
If necessary, use a hose clamp to tighten the hose at drain hose connector to prevent it from leaking.
CAUTION
Do not over tighten, over tightening cause water leakage.
Illustration of how to fi x
drain hose to Mono bloc unit
Drain hose
connector
Drain hose
INSTALLATION OF NETWORK ADAPTOR AND BASE PAN
HEATER
INSTALLATION OF NETWORK ADAPTOR AND BASE PAN HEATER
6
INSTALLATION OF REMOTE CONTROLLER
Mounting The Remote Controller
For exposed type
Preparation:
Make 2 holes for screws using a driver.
UP
Cut here with
a nipper and
remove the burr
with a fi le.
Mount the top case.
•
Align the claws of the top
case and then align the claws
of the bottom case.
Hole for screw
Screw
(fi eld supply)
Claw (2 places)
Pass through
the hole
Bottom case
(Back side)
Top case
(Back side)
Remote controller terminal board
Remove the coating. Approx. 6 mm
Remove the sheath. Approx. 180 mm.
Make sure the wiring connection is in the
correct direction.
Clamper
(fi eld supply)
Claw (2 places)
Wall to which
the remote
controller is
fi xed
Mount the bottom case to
the wall.
Connect the remote control
wiring
•
Arrange the wires along the groove
of the case.
For embedded type
Preparation:
Make 2 holes for screws using a driver.
UP
Avoid the wire
being caught.
Mount the top case.
•
Align the claws of the top
case and then align the claws
of the bottom case.
Hole for
screw
Screw
(fi eld supply)
Claw (2 places)
Bottom case
(Back side)
Top case
(Back side)
Remote controller
terminal board
Remove the coating.
Approx. 6 mm
Make sure the wiring
connection is in the correct
direction.
Claw (2 places)
Mount the bottom case
to the wall.
•
Pass the wire through the hole
in the centre of the bottom case.
Connect the remote
control wiring
WARNING
This section is for authorized and licensed electrician only. Work behind the Cabinet
Front Plate
f
secured by screws must only be carried out under supervision of qualifi ed
contractor, installation engineer or service person.
INSTALLATION OF REMOTE CONTROLLER
5
Installation Location
•
Install at the height of 1 to 1.5 m from the fl oor (Location where average room
temperature can be detected).
•
Install vertically against the wall.
•
Avoid the following locations for installation.
1. By the window, etc. exposed to direct sunlight or direct air.
2. In the shadow or backside of objects deviated from the room airfl ow.
3. Location where condensation occurs (The Remote Controller is not
moisture proof or drip proof.)
4. Location near heat source.
5. Uneven surface.
•
Keep distance of 1 m or more from the TV, radio and PC. (Cause of fuzzy
image or noise)
Remote Controller
3
Wiring
1
2
Terminal for Remote Controller wiring
Remote Controller
Mono bloc unit
Remote Controller
wiring (fi eld supply)
•
No polarity
•
Remote Controller cable shall be (2 x min 0.3 mm²), of double insulation PVC-
sheathed or rubber sheathed cable. Total cable length shall be 50 m or less.
•
Be careful not to connect cables to other terminals (e.g. power source wiring
terminal). Malfunction may occur.
•
Do not bundle together with the power source wiring or store in the same metal
tube. Operation error may occur.
CONNECT THE CABLE TO MONO BLOC UNIT
4
•
In order to ensure optimal performance of the unit, seasonal inspections on the unit, functional check of RCCB, fi eld wiring and piping have to be carried
out at regular intervals. This maintenance should be carried out by authorized dealer.
Maintenance for Magnetic Water Filter Set
c
1. Remove the Cover
g
by loosening the mounting screws to access to the Magnetic Water Filter Set
c
.
2. Turn OFF power supply.
3. Set the two valves for the Magnetic Water Filter Set
c
to “CLOSE”.
4. Take off the clip, then gently pull out the mesh. Beware of small amount water drain out from it.
5. Clean the mesh with warm water to remove all the stain. Use soft brush if necessary.
6. Reinstall the mesh to the Magnetic Water Filter Set
c
and set back the clip on it.
7. Set the two valves for the Magnetic Water Filter Set
c
to “OPEN”.
8. Turn ON power supply.
9. After cleaning, reinstall the Cover
g
by tightening the mounting screws properly.
WARNING
Do not add or replace other than R32 type. It may cause product damage, burst, injury and etc. Use compatible
R32 tools for refrigerant piping work and refrigerant charging during installation or servicing.
MAINTENANCE
10
RECONFIRMATION
8
WARNING
Be sure to switch off all power supply before performing each of the below checkings. Before
obtaining access to terminals, all supply circuits must be disconnected.
CHECK WATER PRESSURE
*(0.1 MPa = 1 bar)
Water pressure should not lower than 0.05 MPa (with inspects the Water Pressure Gauge
4
). If
necessary add tap water into the water circuit.
CHECK PRESSURE RELIEF VALVE
a
•
Check for correct operation of Pressure Relief Valve
a
by turning on the lever to become
horizontal.
•
If you do not hear a clacking sound (due to water drainage), contact your local authorized dealer.
•
Push down the lever after fi nish checking.
•
In case the water keeps drained out from the unit, switch off the system, and then contact your
local authorized dealer.
EXPANSION VESSEL
7
PRE PRESSURE CHECKING
[Upper limit water volume of the system]
The Mono bloc unit has a build-in Expansion Vessel with 10 L air capacity and initial
pressure of 1 bar.
•
Without antifreeze agent condition
Total amount of water in the system should be below 200 L.
If the total amount of water is more than 200 L, please add expansion vessel (fi eld supply).
•
With antifreeze agent condition
In the case of using antifreeze agent, expansion rate
з
is different depending on its maker.
Please refer to the antifreeze agent maker for the expansion rate
з
before calculate the
upper limit water volume of the system.
The expansion vessel capacity required for the system can be calculated from the
formula below.
V : Required gas volume <expansion vessel volume L>
Vo
: System total water volume <L>
: Expansion rate 5
60˚C
= (depends on antifreeze agent used)
P
1
: Expansion tank fi lling pressure
= (100) kPa
P
2
: System maximum pressure
= 300 kPa
-
( ) Please confi rm at actual place
-
The gas volume of the sealed type expansion vessel is presented by <V>.
It’s advised to add 10% margin for required gas volume of calculation.
V =
x Vo
1 -
98 + P
1
98 + P
2
з
з
[Adjustment of the initial pressure of the expansion vessel when there is a difference in
installation height]
If the height difference between the Mono bloc unit and the highest point of the system
water circuit (H) is more than 7m, please adjust the initial pressure of the expansion
vessel (Pg) according to the following formula.
Pg= (H*10+30) kPa
CHECK RCCB
2
Ensure the RCCB
2
set to “ON” condition before check RCCB
2
.
Turn on the power supply to the Mono bloc unit.
This testing could only be done when power is supplied to the Mono bloc unit.
WARNING
Be careful not to touch parts other than RCCB test button when the power is supplied
to Mono bloc unit. Else, electrical shock may happen.
•
Push the “TEST” button on the RCCB
2
. The lever would turn down and indicate “0”,
if it functions normal.
•
Contact authorized dealer if the RCCB
2
malfunction.
•
Turn off the power supply to the Mono bloc unit.
•
If RCCB
2
functions normal, set the lever to “ON” again after testing fi nish.
This product contains fl uorinated greenhouse gasses.
Refrigerant type : R32 (GWP=675)
For WH-MXC09J3E5 and WH-MXC12J6E5
Amount : 1.6kg (1.080 ton CO
2
equivalent)
Install the Mono bloc unit in outdoor locations only.
Avoid installations in areas where the ambient temperature may drop below -20°C.
The Mono bloc unit must be installed on a fl at, solid surface.
A place removed from any heat source or steam which may effect the operation of the
Mono bloc unit.
A place where air circulation is good.
A place where drainage can be easily done.
A place where Mono bloc unit’s operation noise will not cause discomfort to the user.
A place which is accessible for maintenance.
Ensure to keep minimum distance of spaces as illustrated, from wall, ceiling, or other
obstacles.
A place where fl ammable gas leaking might not occur.
A place where the Mono bloc unit’s piping and wiring lengths come within reasonable
ranges.
If an awning is built over the unit to prevent direct sunlight or rain, be careful that heat
radiation from the condenser is not obstructed.
Do not place any obstacles which may cause a short circuit of the discharged air.
Avoid installing the Mono bloc unit at a location where suction side may be exposed
directly to wind.
If Mono bloc unit installed near sea, region with high content of sulphur or oily location
(e.g. machinery oil, etc.), it lifespan maybe shorten.
When installing the product in a place where it will be affected by
typhoon or strong wind such as wind blowing between buildings,
including the rooftop of a building and a place where there is no
building in surroundings, fi x the product with an overturn prevention
wire, etc. (Overturn prevention fi tting model number: K-KYZP15C)
SELECT THE BEST LOCATION
1
CHECK ITEMS
Is the connecting cable fi xed to terminal board fi rmly?
Is the connecting cable clamped fi rmly?
Is the earth wire connection properly done?
Is water pressure higher than 0.05 MPa?
Is the Pressure Relief Valve
a
operation normal?
Is the RCCB operation normal?
Is the power supply voltage within the rated voltage range?
Is there any abnormal sound?
Is the heating operation normal?
Is the thermostat operation normal?
Is the remote control LCD operation normal?
Is the Mono bloc unit water leak free on test run?
(1) Remove the 4 mounting screws as shown in the illustration.
(2) Slide the cabinet front plate
f
downward to release the pawls. Then, pull it toward
front to remove it.
Remove The Cabinet Front Plate
f
Mounting screws
Mounting
screws
Cabinet front plate
f
Fixing of Power Supply Cord
(REFER TO WIRING DIAGRAM AT UNIT FOR DETAIL)
1. An isolating device must be connected to the power supply cable.
•
Isolating device (Disconnecting means) should have minimum 3.0 mm contact gap.
•
Connect the approved polychloroprene sheathed power supply 1 cord and power supply 2 cord and type designation 60245 IEC 57 or heavier cord to the terminal board, and to the
other end of the cord to isolating device (Disconnecting means). See below table for cable size requirement.
Model
Power Supply Cord
Cable Size
Isolating Devices
Recommended RCD
WH-MXC09J3E5 and WH-MXC12J6E5
1
3 x min 4.0 mm
2
30A
30mA, 2P, type A
2
3 x min 4.0 mm
2
30A
30mA, 2P, type AC
2. To avoid the cable and cord being damaged by sharp edges, the cable and cord must be passed through the designated holes before being connected to the terminal block.
3. Secure the cable onto the control board with the holder (clamper).
Connecting with external device (optional)
•
All connections shall
follow to the local national wiring standard.
•
It is strongly recommended to use manufacturer-recommended parts and accessories for installation.
•
For connection to main PCB
1
1. Two-way valve shall be spring and electronic type, refer to “Field Supply Accessories” table for details. Valve cable shall be (3 x min 1.5 mm
2
), of type designation 60245 IEC 57 or
heavier, or similarly double insulation sheathed cable.
* note:
-
Two
-
way Valve shall be CE marking compliance component.
-
Maximum load for the valve is 9.8VA.
2. Three-way valve shall be spring and electronic type. Valve cable shall be (3 x min 1.5 mm
2
), of type designation 60245 IEC 57 or heavier, or similarly double insulation sheathed cable.
* note:
-
Shall be CE marking compliance component.
-
It shall be directed to heating mode when it is OFF.
- Maximum load for the valve is 9.8VA.
3. Room thermostat cable must be (4 or 3 x min 0.5 mm
2
), of type designation 60245 IEC 57 or heavier cord, or similarly double insulation sheathed cable.
4. Maximum output power of booster heater shall be
≤
3 kW. Booster heater cable must be (3 x min 1.5 mm
2
), of type designation 60245 IEC 57 or heavier.
5. Extra pump cable shall be (2 x min 1.5 mm²), of type designation 60245 IEC 57 or heavier.
6. Boiler contact cable / defrost signal cable shall be (2 x min 0.5 mm²), of type designation 60245 IEC 57 or heavier.
7. External control shall be connected to 1-pole switch with min 3.0 mm contact gap. Its cable must be (2 x min 0.5 mm
2
), double insulation layer of PVC-sheathed or rubber-sheathed cable.
* note:
-
Switch used shall be CE compliance component.
- Maximum operating current shall be less than 3A
rms
.
8. Tank sensor shall be resistance type, please refer to graph below for the characteristic and details of sensor. Its cable shall be (2 x min 0.3 mm
2
), double insulation layer (with insulation
strength of min 30V) of PVC-sheathed or rubber-sheathed cable.
-30
-20 -10
0
10
20
30
16000
14000
12000
10000
8000
˚C
6000
4000
2000
0
Tank sensor characteristic
Resistance
Tank Sensor Resistance Vs Temperature
9. Room sensor zone 1 cable shall be (2 x min 0.3 mm²) double insulation layer of PVC-sheathed or rubber-
sheathed.
10. Outdoor air sensor cable shall be (2 x min 0.3 mm²) double insulation layer of PVC-sheathed or rubber-sheathed.
11. Tank OLP cable must be (2 x min 0.5 mm
2
), double insulation layer of PVC-sheathed or rubber-sheathed cable.
Optional cables:
•
External control cable
•
Tank sensor cable
•
Room sensor zone 1
•
Outdoor air sensor cable
•
Tank OLP cable
•
Power Supply 1 cord
Apply cut
Bushing
e
x 6
•
Power Supply 2 cord
•
Remote controller cable
Optional cables:
•
3-way valve cable
•
2-way valve cable
•
Room thermostat zone 1 cable
•
Booster heater cable
•
Extra pump cable
•
Boiler contact cable /
Defrost signal cable
How to guide optional cables and power supply cords to Bushing
e
A
L
N
L1
WARNING
ABCDEFGHJMFLG
ABCDEFGHJMFLG
ABCDEFGHJMFLG
ABCDEFGHJMFLG
POWER SUPPLY 1
POWER SUPPLY 2
N1
B
CAUTION
240-250V
Bind all lead
wires with
these bands
PCB
1
Power supply 2
RCCB
Bind all lead wires
with these bands
Power supply 1
RCCB
Holder
(Clamper)
•
Power Supply 1 cord
•
Power Supply 2 cord
Optional cables:
•
3-way valve cable
•
2-way valve cable
•
Room thermostat zone 1 cable
•
Booster heater cable
•
Extra pump cable
•
Boiler contact cable /
Defrost signal cable
•
Remote controller cable
Optional cables:
•
External control cable
•
Tank sensor cable
•
Room sensor zone 1
•
Outdoor air sensor cable
•
Tank OLP cable
How to guide optional cables and power supply cords
(view without internal wiring)
•
For connection to optional PCB
4
1. By connecting optional PCB, 2 Zone temperature control can be achieved. Please connect mixing valves,
water pumps and thermistors in zone 1 and zone 2 to each terminals in optional PCB.
Temperature of each zone can be controlled independently by remote controller.
2. Pump zone 1 and zone 2 cable shall be (2 x min 1.5 mm²), of type designation 60245 IEC 57 or heavier.
3. Solar pump cable shall be (2 x min 1.5 mm²), of type designation 60245 IEC 57 or heavier.
4. Pool pump cable shall be (2 x min 1.5 mm²), of type designation 60245 IEC 57 or heavier.
5. Room thermostat zone 1 and zone 2 cable shall be (4 x min 0.5 mm²), of type designation 60245 IEC 57
or heavier.
6. Mixing valve zone 1 and zone 2 cable shall be (3 x min 1.5 mm²), of type designation 60245 IEC 57 or heavier.
7. Room sensor zone 1 and zone 2 cable shall be (2 x min 0.3 mm²), double insulation layer (with insulation
strength of minimum 30V) of PVC-sheathed or rubber-sheathed cable.
8. Buffer tank sensor, pool water sensor and solar sensor cable shall be (2 x min 0.3 mm²), double insulation
layer (with insulation strength of minimum 30V) of PVC-sheathed or rubber-sheathed cable.
9. Water sensor zone 1 and zone 2 cable shall be (2 x min 0.3 mm²), double insulation layer of PVC-sheathed
or rubber-sheathed cable.
10. Demand signal cable shall be (2 x min 0.3 mm²), double insulation layer of PVC-sheathed or rubber-sheathed
cable.
WARNING
This section is for authorised and licensed electrician only. Work behind the cabinet front plate
f
secured by screws must only be carried out under supervision of qualifi ed contractor,
installation engineer or service person.
11. SG signal cable shall be (3 x min 0.3 mm²), double insulation layer of PVC-sheathed or rubber-sheathed cable.
12. Heat/Cool switch cable shall be (2 x min 0.3 mm²), double insulation layer of PVC-sheathed or rubber-
sheathed cable.
13. External compressor switch cable shall be (2 x min 0.3 mm²), double insulation layer of PVC-sheathed or
rubber-sheathed cable.
Optional cables:
•
Mixing valve zone 1 cable
Optional cables:
•
Mixing valve zone 2 cable
from
optional
PCB
Optional cables:
•
Pump zone 1 cable
•
Pump zone 2 cable
•
Solar pump cable
•
Pool pump cable
•
Error signal cable
•
Room thermostat zone 1 cable
•
Room thermostat zone 2 cable
from
optional
PCB
Optional cables:
•
Room sensor zone 1 cable
•
Room sensor zone 2 cable
•
Buffer tank sensor cable
•
Pool sensor cable
•
Water sensor zone 1 cable
•
Water sensor zone 2 cable
•
Demand signal cable
•
Solar sensor cable
•
SG signal cable
•
Heat/Cool switch cable
•
External Compressor
switch cable
from
optional
PCB
How to guide optional cables to bushing
e
A
L
N
L
1
WARNING
CAUTION
240-250V
ABCDEFGHJMFLG
ABCDEFGHJMFLG
ABCDEFGHJMFLG
ABCDEFGHJMFLG
POWER SUPPLY 1
POWER SUPPLY 2
N
1
B
•
Pump zone 1 cable
•
Pump zone 2 cable
•
Solar pump cable
•
Pool pump cable
•
Error signal cable
•
Room thermostat zone 1 cable
•
Room thermostat zone 2 cable
•
Mixing valve zone 1 cable
•
Mixing valve zone 2 cable
•
Room sensor zone 1 cable
•
Room sensor zone 2 cable
•
Buffer tank sensor cable
•
Pool sensor cable
•
Water sensor zone 1 cable
•
Water sensor zone 2 cable
•
Demand signal cable
•
Solar sensor cable
•
SG signal cable
•
Heat/Cool switch cable
•
External Compressor switch cable
How to guide optional cables (view without internal wiring)
Terminal screw on PCB
Maximum tightening torque cN•m {kgf•cm}
M3
50 {5.1}
M4
120 {12.24}
CONNECTING REQUIREMENT
WH-MXC09J3E5
•
This equipment’s Power Supply 1 complies with IEC/EN 61000-3-12 provided that the short circuit power
S
sc
is greater than or equal to 1900kW at the interface point between the user’s supply and the public
system. It is the responsibility of the installer or user of the equipment to ensure, by consultation with
the distribution network operator if necessary, that the equipment is connected only to a supply with a
short circuit power S
sc
greater than or equal to 1900kW.
•
The equipment’s Power Supply 1 complies with IEC/EN 61000-3-11 and shall be connected to a suitable
supply network, having services current capacity
100A per phase. Please liaise with supply authority
that the service current capacity at the interface point is suffi cient for the installation of the equipment.
•
The equipment’s Power Supply 2 complies with IEC/EN 61000-3-2.
•
The equipment’s Power Supply 2 complies with IEC/EN 61000-3-3 and can be connected to current
supply network.
WH-MXC12J6E5
•
This equipment’s Power Supply 1 complies with IEC/EN 61000-3-12 provided that the short circuit power
S
sc
is greater than or equal to 1900kW at the interface point between the user’s supply and the public
system. It is the responsibility of the installer or user of the equipment to ensure, by consultation with
the distribution network operator if necessary, that the equipment is connected only to a supply with a
short circuit power S
sc
greater than or equal to 1900kW.
•
The equipment’s Power Supply 1 complies with IEC/EN 61000-3-11 and shall be connected to a suitable
supply network, having services current capacity
100A per phase. Please liaise with supply authority
that the service current capacity at the interface point is suffi cient for the installation of the equipment.
•
This equipment’s Power Supply 2 complies with IEC/EN 61000-3-12.
•
The equipment’s Power Supply 2 complies with IEC/EN 61000-3-11 and shall be connected to suitable
supply network, with the following maximum permissible system impedance Z
max
= 0.193 ohm (
) at
the interface. Please liaise with supply authority to ensure that the Power Supply 2 is connected only
to a supply of that impedance or less.
Terminal on the Mono bloc unit
L
N
L
1
N
1
(Power Supply Cord)
Terminals on the isolating device from
power supply (Disconnecting means)
L
N
L
1
N
1
Power Supply 2
Power Supply 1
Terminal screw
Tightening torque
cN•m {kgf•cm}
M4
157~196 {16~20}
M5
196~245 {20~25}
*1 - Earth wire must be longer than other cables
for safety reasons.
Power Supply Cord
*1
WIRE STRIPPING AND CONNECTING REQUIREMENT
5 mm or
more
(gap between wires)
Terminal
board
Wire stripping
No loose strand
when insert
10 ± 1 mm
ACCEPT
Conductor
over insert
Conductor not
fully insert
Conductor
fully insert
PROHIBITED
PROHIBITED
Network Adaptor
6
and
7
Installation (Optional)
1.
Open the Cabinet front plate
f
, then connect the Network Adaptor Cable
7
to the CN-CNT connector on the printed circuit board.
•
Pull the cable out of the Mono bloc unit so that there is no pinching.
•
If an optional PCB has been install in the Mono bloc unit, connect the CN-CNT
connector to Optional PCB
4
.
5.
Use the included cord clamp to
fi
x the CN-CNT cable to the wall.
Pull the cable around as shown in the diagram so that external forces cannot
act on the connector in the adaptor. Use the included cable tie to fi x the cables
together.
A
L
N
L1
WARNING
ABCDEFGHJMFLG
ABCDEFGHJMFLG
ABCDEFGHJMFLG
ABCDEFGHJMFLG
POWER SUPPLY 1
POWER SUPPLY 2
N1
B
CAUTION
240-250V
Cord clamp
Cable tie
Base Pan Heater
5
(Optional)
•
It is strongly recommended to install a Base Pan Heater
5
(optional) if the Mono
bloc unit is installed in cold climate area. Refer the Base Pan Heater
5
(optional)
installation instruction for details of installation.
2.
Insert a
fl
at head screwdriver into the slot on the top of the adaptor and
remove the cover. Connect the other end of the CN-CNT cable connector to
the connector inside the adaptor.
Slot
Connector
3.
On the wall near the Mono bloc unit, attach
the adaptor by screwing screws through the
holes in the back cover.
4.
Pull the CN-CNT cable through the hole in
the bottom of the adaptor and re-attach the
front cover to the back cover.
CN-CNT cable
(Take care not to
pinch the cable)
Screws
A
L
N
L
1
WARNING
ABCDEFGHJMFLG
ABCDEFGHJMFLG
ABCDEFGHJMFLG
ABCDEFGHJMFLG
POWER SUPPLY 1
POWER SUPPLY 2
N
1
B
CAUTION
240-250V
Network
Adaptor
cable
Bind all
lead wires
with these
bands
PCB
1
A
L
N
L
1
WARNING
CAUTION
240-250V
ABCDEFGHJMFLG
ABCDEFGHJMFLG
ABCDEFGHJMFLG
ABCDEFGHJMFLG
N
1
B
POWER SUPPLY 1
POWER SUPPLY 2
Network
Adaptor
cable
Without Optional PCB
With Optional PCB
CHARGING THE WATER
7
•
Make sure all the piping installations are properly done before carry out below steps.
1. Open Cabinet front plate
f
to access to the Pressure Relief Valve
a
and Air Purge Valve
b
2. Turn the plug on the Air Purge Valve
b
outlet anticlockwise by one complete turn from
fully closed position.
Air purge valve
b
Plug (turn
anticlockwise by
one complete
turn)
3. Set the Pressure Relief Valve
a
level “DOWN”.
Pressure relief valve
a
Pressure
relief valve
a
Lever
Turn down
or
Pressure relief
valve
a
Lever
Turn down
Pressure relief valve
a
4. Start fi lling water (with pressure more than 0.1 MPa (1 bar)) to the Mono bloc unit via water
inlet. Stop fi lling water if the free water fl ow through Pressure Relief Valve
a
drain hose.
5. Turn ON the power supply and make sure Water Pump
5
is running.
6. Check and make sure no water leaking at the tube connecting points.
7. Reinstall the Cabinet front plate
f
by tightening the 2 mounting screws.
Mounting
screws
Cover
g
ENGLISH
ACXF60-41770-AA
PRINTED IN MALAYSIA
2/36