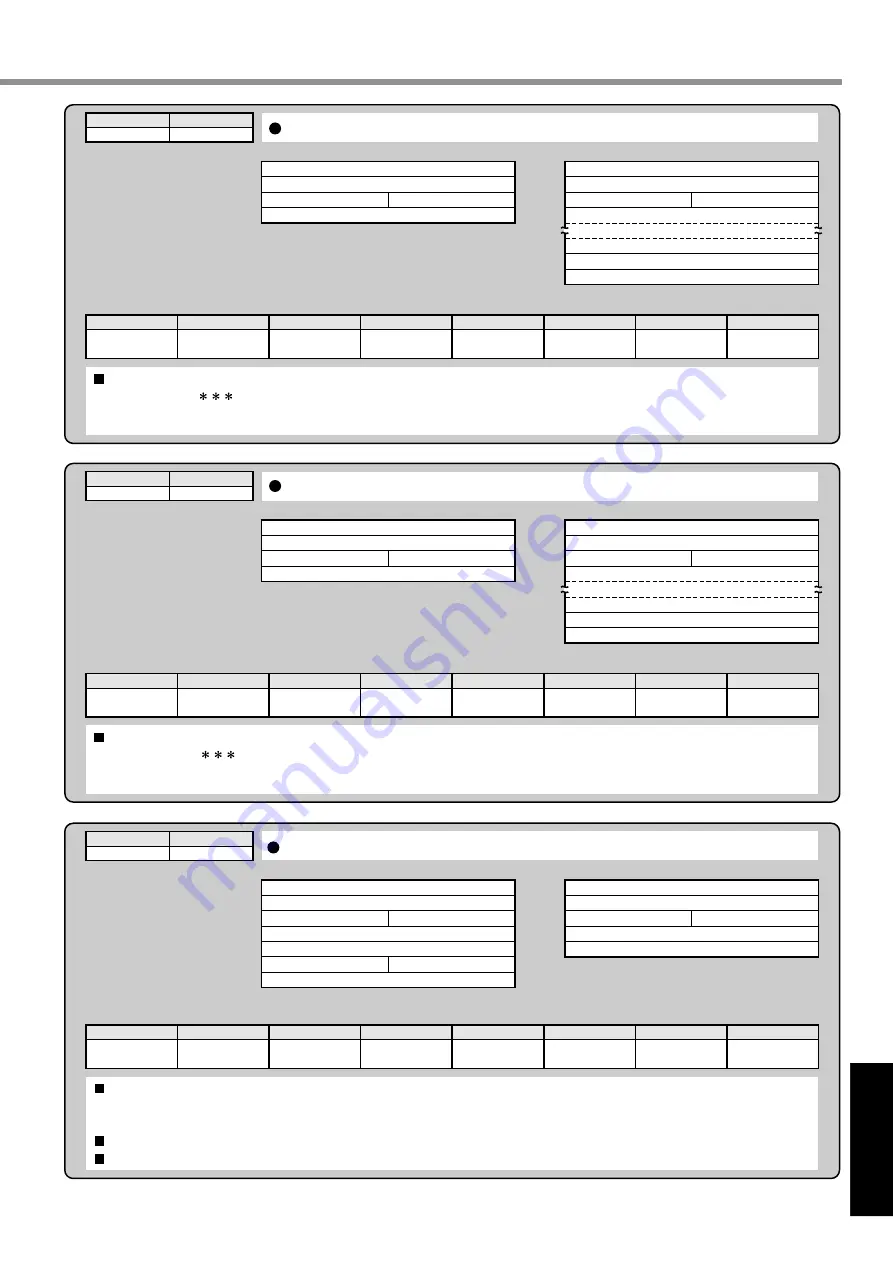
167
[Reference]
Reference
command
1
mode
1
Setting of RS232C protocol parameters
Received data
3
axis
T1
T2
checksum
1
1
RTY
M/S
Error code
Transmitted data
Setting of the previous protocol parameters remains valid until execution of this command completes. The updated parameter setting will be
valid from a next command after execution of this command.
M/S=0 indicates "SLAVE" mode, while M/S=1 indicates "MASTER".
The RTY code is 4 bit and M/S is 1 bit.
Unit of T1 and T2 are 0.1 second and 1 second, respectively.
bit7
0 : Normal
1 : Error
6
5
Command error
4
3
RTY error
2
T2 error
1
T1 error
0
M/S error
1
axis
Error code
checksum
1
1
command
0
mode
5
Readout of the driver model name
Received data
0
axis
checksum
0
5
Error code
Transmitted data
The driver model name is 12 characters and transmitted by ASCII code.
ex. "MKDET1505 "
bit7
0 : Normal
1 : Error
6
5
Command error
4
3
2
1
0
0Dh
axis
Driver Model Name (high order)
Driver Model Name (low order)
Error code
checksum
0
5
command
0
mode
6
Readout of the motor model name
Received data
0
axis
checksum
0
6
Error code
Transmitted data
The motor model name is 12 characters and transmitted by ASCII code.
ex. "MUMA012P1 "
bit7
0 : Normal
1 : Error
6
5
Command error
4
3
2
1
0
0Dh
axis
Motor Model Name (high order)
Motor Model Name (low order)
Error code
checksum
0
6
Buy: www.ValinOnline.com | Phone 844-385-3099 | Email: [email protected]
Содержание Minas E Series
Страница 6: ...6 MEMO Buy www ValinOnline com Phone 844 385 3099 Email CustomerService valin com ...
Страница 64: ...64 MEMO Buy www ValinOnline com Phone 844 385 3099 Email CustomerService valin com ...
Страница 215: ...215 Reference Reference MEMO Buy www ValinOnline com Phone 844 385 3099 Email CustomerService valin com ...