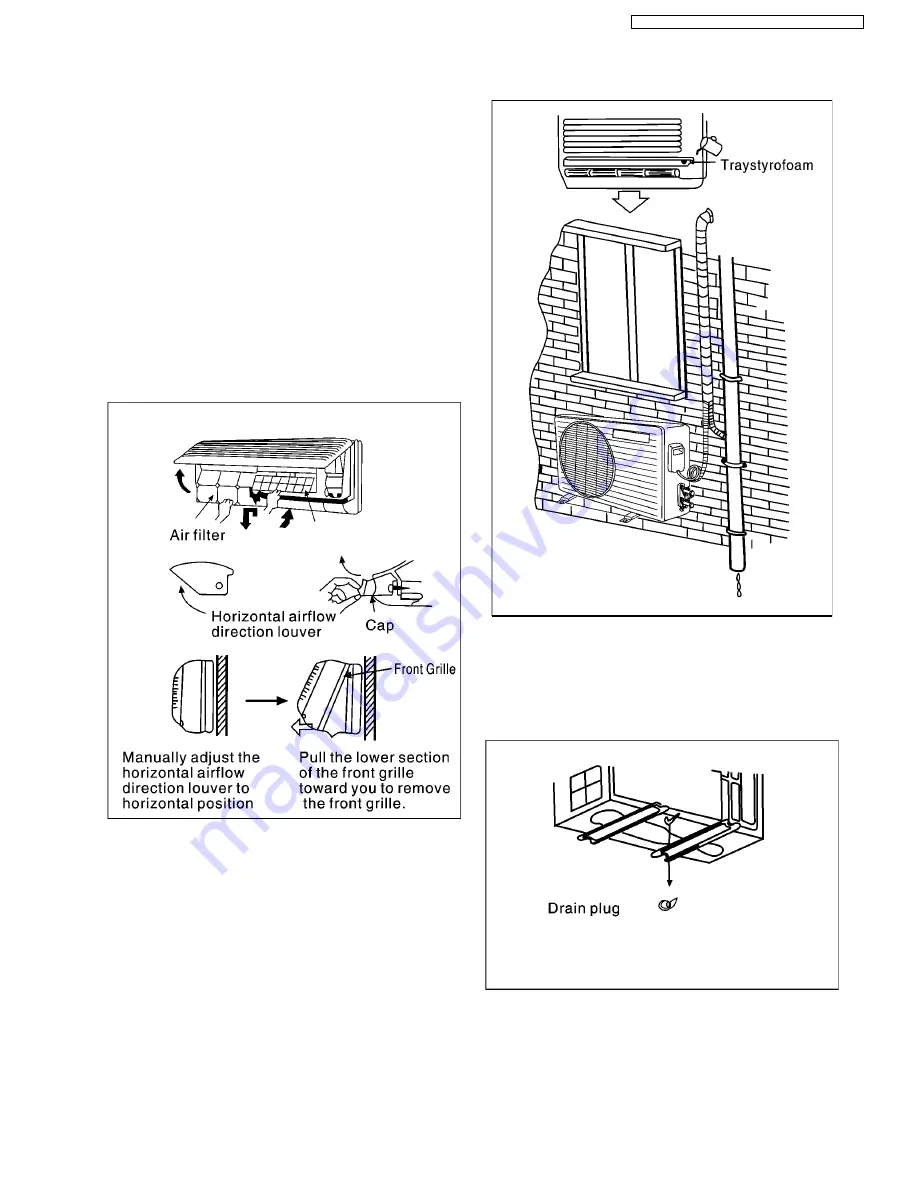
8.8.1. Checking the drainage
1. Remove the front grille from the cabinet
When removing the front grille for maintenance purposes,
etc, carry out by the following procedures.
a. Set the vertical airflow direction louver (1) to the
horizontal position.
b. Remove the two caps on the front grille as shown in the
illustration at right, and then remove the two mounting
screws.
c. Pull the lower section of the front grille toward you to
remove the front grille.
When reinstalling the front grille, first set the vertical airflow
direction louver to the horizontal position, and then carry out
by steps 3 and 2 in that order. At this time check to sure that
the fixing tabs on the top inside edge of the front grille are
securely inserted into the respective slots.
2. Checking the drainage
•
•
•
•
Pout a glass of water into the drain train traystyroform.
•
•
•
•
Ensure water flow out from drain hose of indoor unit.
3. Drainage control for outdoor unit
•
•
•
•
If a drainage plug is applied, the outdoor unit should at
least be 3 centimeters high from the floor.
•
•
•
•
If is better not to use the drainage plug if the
temperature is lower than 0°C, since icing of the
condensed water may block the water flow.
8.8. Checking the drainage and connecting the cable to indoor unit
37
CS-SA9CKP CU-SA9CKP5 / CS-SA12CKP CU-SA12CKP5
Содержание CS-SA12CKP
Страница 9: ...3 Dimensions 9 CS SA9CKP CU SA9CKP5 CS SA12CKP CU SA12CKP5 ...
Страница 10: ...10 CS SA9CKP CU SA9CKP5 CS SA12CKP CU SA12CKP5 ...
Страница 11: ...4 Refrigeration Cycle Diagram 11 CS SA9CKP CU SA9CKP5 CS SA12CKP CU SA12CKP5 ...
Страница 12: ...5 Block Diagram 12 CS SA9CKP CU SA9CKP5 CS SA12CKP CU SA12CKP5 ...
Страница 13: ...6 Wiring Diagram 13 CS SA9CKP CU SA9CKP5 CS SA12CKP CU SA12CKP5 ...
Страница 17: ...Time Graph for soft dry operation 17 CS SA9CKP CU SA9CKP5 CS SA12CKP CU SA12CKP5 ...
Страница 26: ...26 CS SA9CKP CU SA9CKP5 CS SA12CKP CU SA12CKP5 ...
Страница 55: ...13 Exploded View CS SA9CKP CS SA12CKP 55 CS SA9CKP CU SA9CKP5 CS SA12CKP CU SA12CKP5 ...
Страница 57: ...15 Exploded View CU SA9CKP5 CU SA12CKP5 57 CS SA9CKP CU SA9CKP5 CS SA12CKP CU SA12CKP5 ...
Страница 61: ...17 1 REMOTE CONTROL 61 CS SA9CKP CU SA9CKP5 CS SA12CKP CU SA12CKP5 ...
Страница 62: ...17 2 PRINTED CIRCUIT BOARD REMOTE CONTROL 62 CS SA9CKP CU SA9CKP5 CS SA12CKP CU SA12CKP5 Printed in China ...