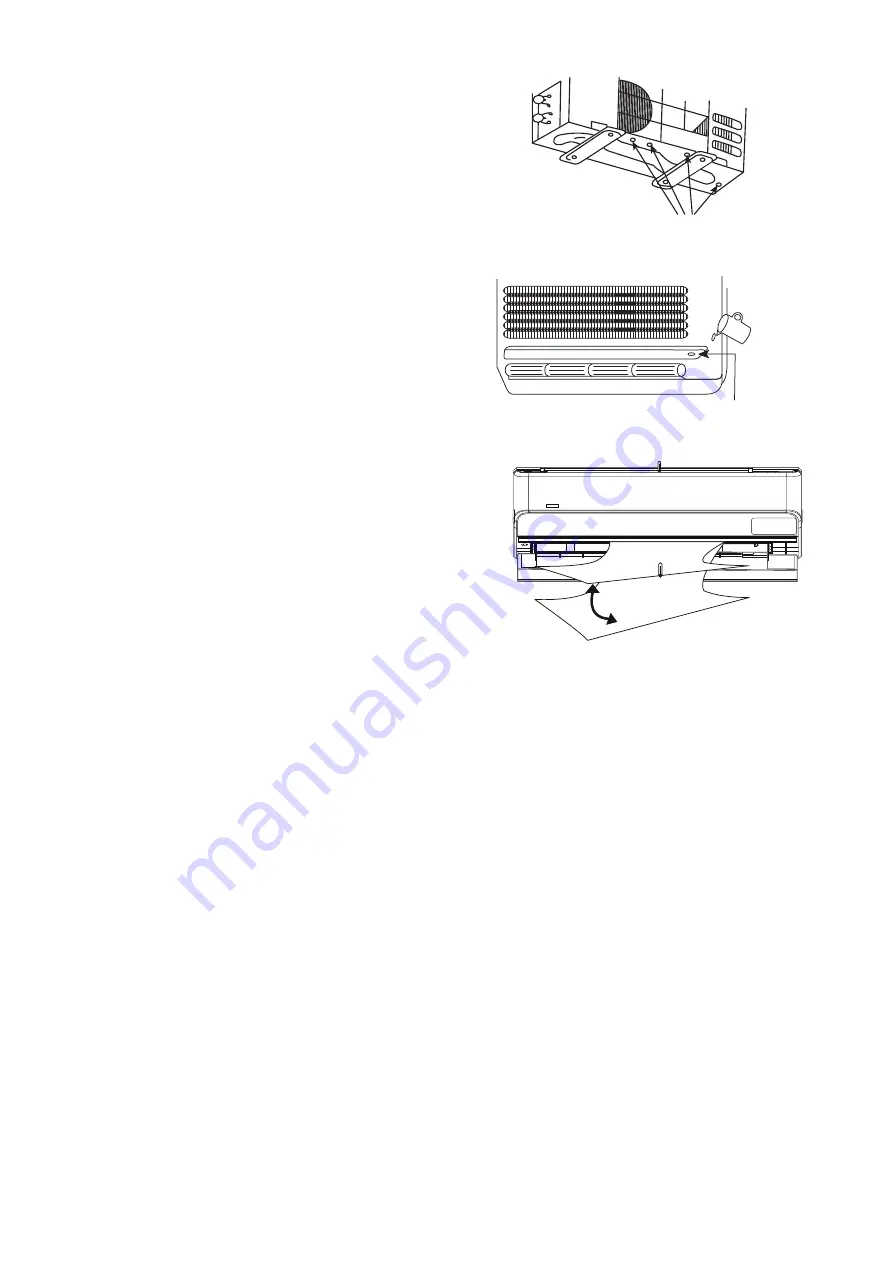
34
12.3.9 Outdoor Unit Drain Water
Water will drip from the basepan hole area during
defrost function.
To avoid water dripping, do not stand or place
objects at this area.
Hose
12.3.10 Check the Drainage
Open front panel and remove air filters.
(Drainage checking can be carried out without
removing the front grille.)
Pour a glass of water into the drain tray-styrofoam.
Ensure that water flows out from drain hose of the
indoor unit.
Drain tray-styrofoam
12.3.11 Evaluation of the Performance
Operate the unit at cooling/heating operation
mode for fifteen minutes or more.
Measure the temperature of the intake and
discharge air.
Ensure the difference between the intake
temperature and the discharge is more than 8°C
during Cooling operation or more than 14°C
during Heating operation.
Discharge air