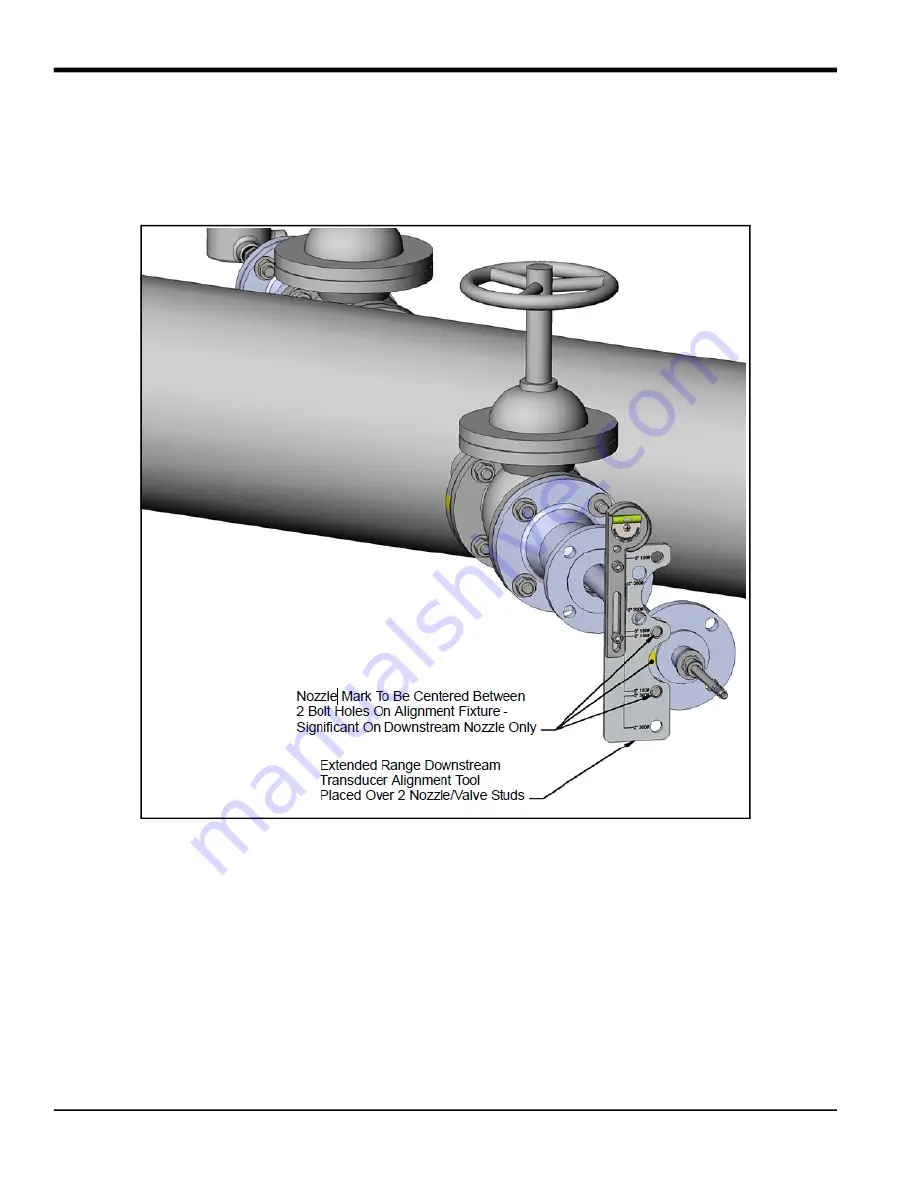
Chapter 4. Inserting T17 Transducers into the Pipe
46
Model T17 Installation Guide
4.2.3 Aligning the Downstream Transducer (cont.)
8.
Place the alignment fixture over the two studs in the flange at the top of the barrel assembly, and rotate the
barrel flange until the bubble aligns between the tick marks on the vial. Slowly press the flange toward the
insertion mechanism flange until the gasket and raised faces of both flanges are mated. The studs should also
engage the holes in the insertion mechanism flange. If desired, the barrel flange can be rotated slightly to
maintain the bubble alignment on the gauge.
9.
Remove the fixture and install the remaining studs, washers, and nuts. Tighten them to the correct torque.
10.
Place a tag on the isolation valve stating the following:
DO NOT OPERATE (CLOSE) WHEN
TRANSDUCER IS INSERTED INTO PIPE.
11.
Refer to the flowmeter
Startup Guide
to make the transducer electrical connections.
Содержание T17
Страница 1: ...panametrics com Flow 916 128 C August 2021 Model T17 Ultrasonic Flow Transducer Installation Guide...
Страница 2: ......
Страница 4: ...ii no content intended for this page...
Страница 7: ...Model T17 Installation Guide v Chapter...
Страница 8: ...Chapter vi Model T17 Installation Guide no content intended for this page...
Страница 10: ...Contents viii Model T17 Installation Guide...
Страница 11: ...Model T17 Installation Guide ix Contents...
Страница 12: ...Contents x Model T17 Installation Guide...
Страница 46: ...Chapter 3 Installing an Isolation Valve 34 Model T17 Installation Guide...
Страница 64: ...Chapter 4 Inserting T17 Transducers into the Pipe 52 Model T17 Installation Guide...
Страница 70: ...Chapter 6 Specifications 58 Model T17 Installation Guide...
Страница 72: ...Warranty 60 Model T17 Installation Guide no content intended for this page...
Страница 74: ...2 Model T17 Installation Guide...
Страница 75: ......