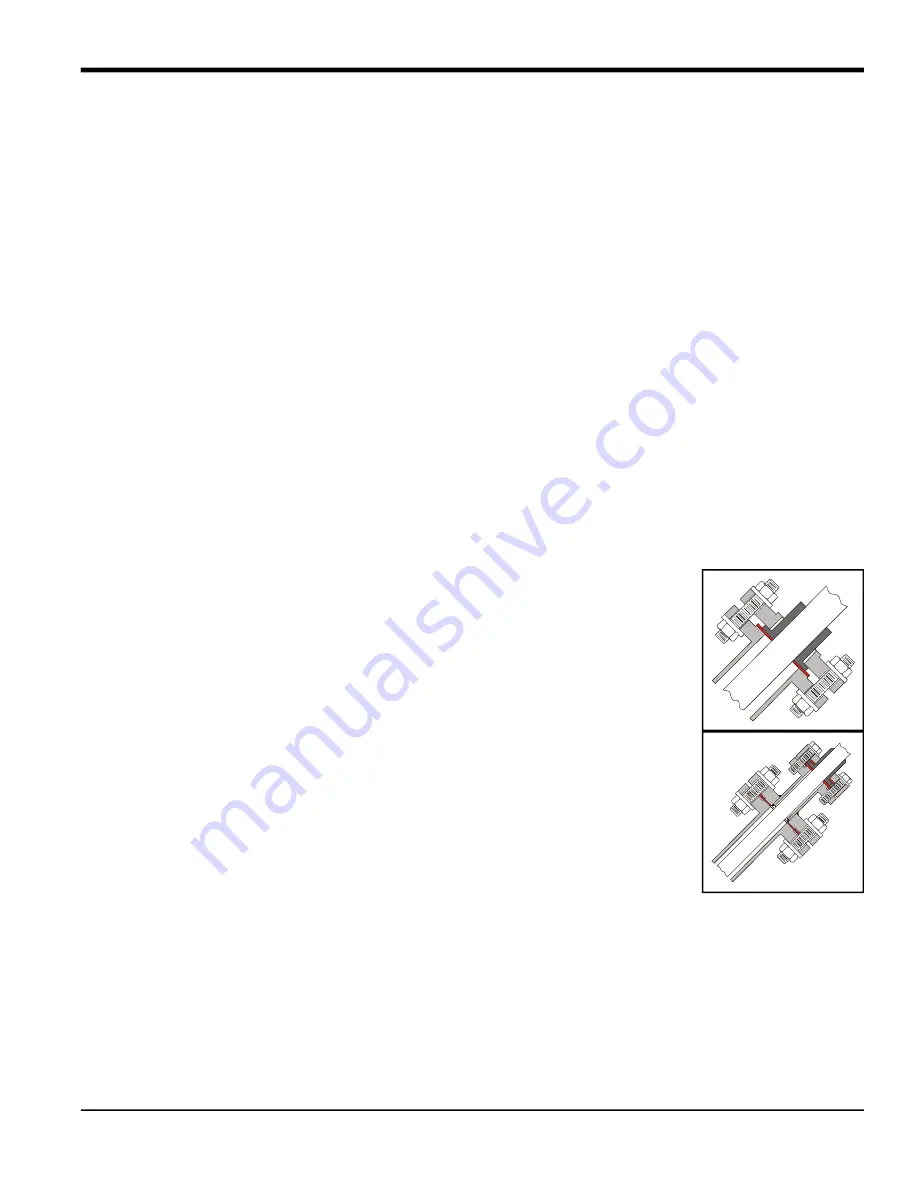
BWT™ System Installation Guide
1
Chapter 1. General Information
Chapter 1. General Information
1.1
Introduction
Installing the Bundle Waveguide Technology™ (BWT
TM)
System consists of creating a meter body, installing the
transducer buffer, and then mounting transducers into the buffer. Panametrics offers a variety of buffers and meter
bodies for liquid and gas applications. This section consists of general information for the following topics:
• Types of BWT buffers (see
• General guidelines for transducer position and location (see
• BWT meter body (see
• Handling and installing a meter body (see
• Meter body requirements when flushing (see
IMPORTANT:
If the BWT buffers and transducers are used in a PanaFlow HT system, you must follow all instructions in
the PanaFlow HT User’s Manual (910-294U) and Safety Manual (917-025).
1.2
Types of BWT Buffers
Buffers are used to protect the BWT transducers from temperature extremes. Since they mount directly into the pipe
coupling or nozzle, they also act as barriers against the process, making it possible for the transducers to be
removed without interrupting the process or emptying the pipe.
IMPORTANT:
The buffers also ensure that the service temperature of the transducers remains at ambient.
There are three BWT buffer types available for transducers for liquid and gas applications:
• Standard BWT Buffer (part number
FTPA
) - is used for liquid and gas applications. The
buffer has a flanged process connection and is available in two lengths:
2 in.
(temperatures up to 600
o
F/315
o
C) and
6 in.
(temperatures up to 1,100
o
F/600
o
C).
• Acoustic Isolation BWT Buffer (part number
FIPA
) - is used for gas applications at
lower pressures. The buffer has a flanged isolation section that reduces acoustic
short circuits. The outer buffer has a flanged process connection and is available in
two lengths
:
2 in.
(temperatures up to 600
o
F/315
o
C) and
6 in.
(temperatures up to
1,100
o
F/600
o
C).
Содержание BWT System
Страница 1: ...panametrics com Flow 916 058 F July 2021 BWT System Installation Guide ...
Страница 2: ......
Страница 4: ...ii no content intended for this page ...
Страница 8: ...Contents BWT System Installation Guide ...
Страница 16: ...Chapter 1 General Information 8 BWT System Installation Guide no content intended for this page ...
Страница 52: ...Chapter 5 Specifications 44 BWT System Installation Guide no content intended for this page ...
Страница 54: ...46 BWT System Installation Guide no content intended for this page ...
Страница 57: ......